近年来,随着增材制造技术的普及和应用,金属增材制造技术作为增材制造领域的一个重要分支,在制造领域大放异彩,并迅速发展[1-2]。金属增材制造是以高能束(激光、电子束、电弧等)为加热源,金属粉末/丝材为原料,辅助计算机三维数据模型,直接制造新型金属构件的技术方法,特别适合小批量、个性化、形状复杂零件的制造。
随着航空领域使用要求和设计水平的不断提高,新型航空飞行器不断向性能高、寿命长、成本低、可靠性好等方向发展,航空零件逐渐趋于结构复杂化和整体化。金属增材制造由于其加工周期短、材料利用率高、设计更自由等优势,能够满足航空零件制造的低成本、短周期需求,在航空制造领域得到了广泛的应用。金属增材制造技术是满足现代航空零件快速低成本研制的重要手段,同时也是满足航空超规格、复杂金属结构制造的关键技术之一[3]。
1 、典型金属增材制造技术及其应用
金属增材制造技术在多年的发展中形成了多种工艺,在航空领域中应用较为广泛的主要有选区激光熔融技术(Selective Laser Melting,SLM)[4]、激光熔化沉积技术(Laser Melting Deposition,LMD)[5]、电子束熔化成形技术(Electron Beam Melting,EBM)[6,9]、电子束自由成形制造技术(ElectronBeam Freeform Fabrication,EBF)[7,9]、电弧增材制造技术(Wire and Arc Additive Manufacturing,WAAM)[8]及其他高能热源或复合热源的快速成形技术等,下文将对这几种增材制造方式进行简要说明。
按增材形式,主要分为铺放金属粉末和同步送粉/送丝两种增材制造方式。表1 和表2 分别进行了成形方式、应用对象和特点等的归纳和对比。
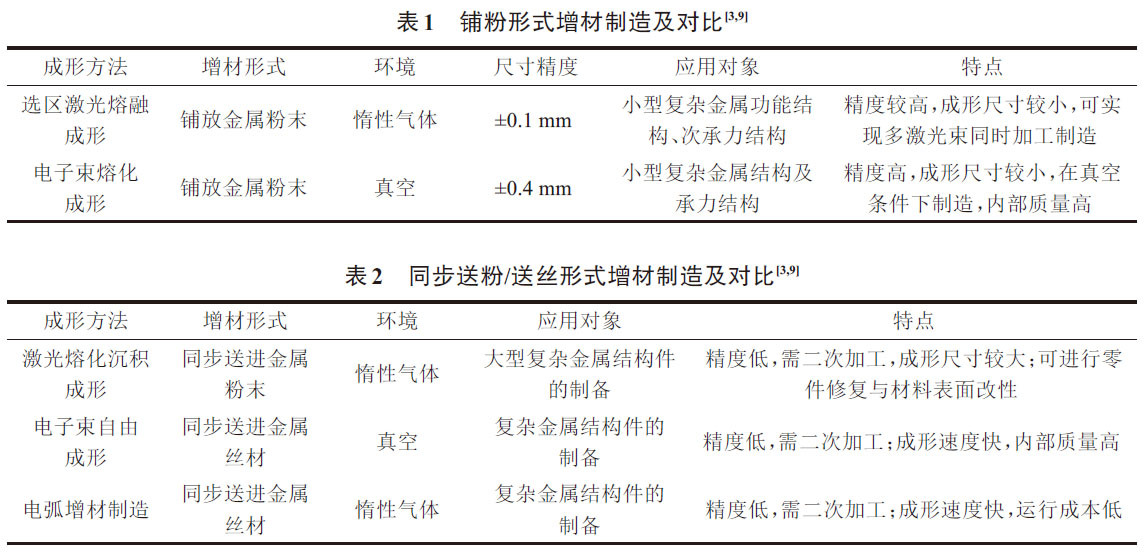
1.1 选区激光熔融技术(SLM)
选区激光熔融技术是通过专业计算机软件对零件三维数模进行分层切片,形成截面轮廓信息后,利用高能激光束逐层选择性烧结金属粉末,凝固堆积零件实体的制造方式,技术原理如图1 所示。
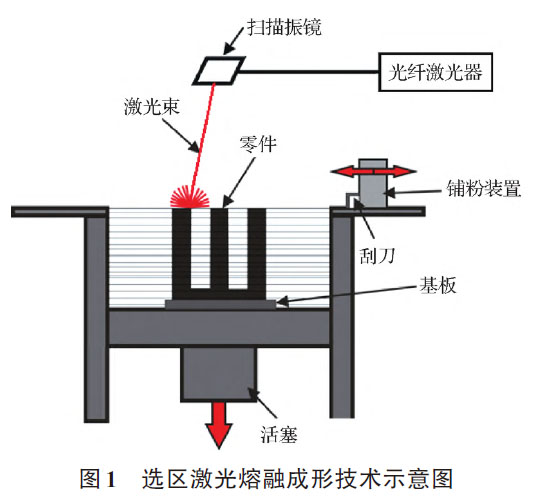
SLM加工精度较高,只需表面规整处理,特别适合直接成形小、中型精密复杂典型构件[10]。
1995 年,德国Fraunhofer 研究所首次提出SLM技术,经过不断的技术研究,在2002 年成功利用SLM技术制造出了材料致密、成形度高、性能优良的金属零件,并进行了商业推广。相对其他金属增材制造技术,SLM技术较为成熟,且已研制出商用设备。其中德国的EOS、SLM Solution、ConceptLaser 公司、英国的Reinishaw 公司等都研制了各种
不同尺寸的SLM成形设备。目前在航空领域,英国的BAE、Roll-Royce、Airbus 公司,美国的Boeing、Lockheed Martin、GE公司等,都投入大量的人力、财力进行SLM成形技术的研究工作,制造了包括航空发动机燃油喷嘴、发动机低压涡轮、涡轮进气口等多种复杂航空零件。SLM技术能使这些原来由多个部件组装的零件整体成形,大大节省了质量、加工工时和制造成本。如图2(a)所示,GE 公司采用SLM技术生产的燃油喷嘴,生产周期较原来缩短了2/3,生产成本降低了50%[9]。同时,新型航空结构对轻量化及特殊功能结构有着迫切的需求,SLM技术都能实现类似结构的生产。Airbus 公司对A320 飞机钛合金铰链支架进行拓扑优化设计,采用SLM技术制造的零件减重60%以上,还能满足疲劳测试强度要求[9,11,18]。空客的飞机隔离舱依据创成式建模方式,采用Scalmalloy 生物结构,用SLM 技术制造复杂网格结构,最大限度的减少了材料的使用[2,12],如图2(b)所示。国内的西北工业大学、华中科技大学等的研究水平也已接近世界前列,不但制造了如航空支架、格栅、吊挂等的多种复杂异形航空结构零件,还实现了材料的成形工艺、几何尺寸和力学性能的全面提高,使这些零件的使用性能都能达到航空设计要求,并已实现批量的装机应用[13]。
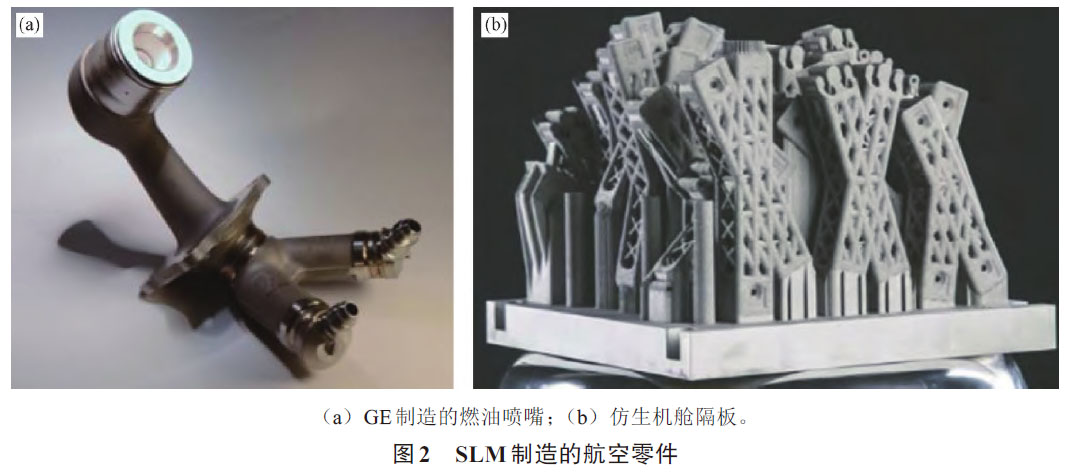
1.2 激光熔化沉积技术(LMD)
20 世纪90 年代,致密金属零件的激光熔化沉积技术在西方发达国家迅速发展[14],其示意图如图3所示。激光熔化沉积技术采用激光作为能量源,按照软件生成的加工路径,同步送粉并逐层熔化金属粉末,快速凝固逐层堆积成零件毛坯,后续仅需少量机加。
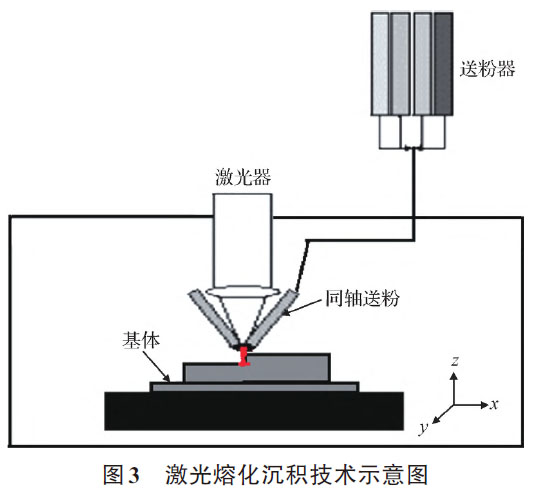
美国、德国、瑞士、英国等国的研究机构都开展了高性能航空金属零件的激光熔化沉积研究。美国Optomec Design 公司与美国Sandia 国家实验室合作,最早推出了基于激光熔化沉积技术的商业化设备。目前,美国DM3D、RPM Innovations、德国Trumpf、DMG Mori、法国BeAM、日本MHI、韩国InssTek 等都开发了相关设备[15]。激光熔化沉积技
术可灵活加工制造航空零部件,比如美国GE 公司和英国TWI 制造了压气机叶片钛合金进气边、大型整体框梁结构件等。美国AeroMet 公司为F/A-18E/F 验证机试制了飞机钛合金发动机舱推力梁、机翼翼梁等,F-22 战斗机机翼接头等次承力结构件,构件疲劳强度达到设计要求,实现了装机应用[16]。美国Sandia 国家实验室,开展了钛合金、不锈钢、高温合金等的激光熔化沉积成形技术研究,其成形零件的塑性和强度均高于锻件水平[17]。另外,该技术还能应用其熔覆沉积功能进行零件修复,美国军方最先将激光修复技术实用化,主要用于修复整体叶盘、钛合金支架、钛合金框梁、航空发动机涡轮以及重要的武器装备等[5]。美国的AeroMet 公司采用激光成形技术完成了F15 战斗机中钛合金机翼梁的检修,使检修周期缩短为1 周[18];美国Optomec Design公司应用LMD技术对T700 海军飞机涡轮叶盘和叶片的磨损部位进行修复,修复后性能满足使用要求[19];瑞士的洛桑理工学院采用激光熔化沉积技术修复航空发动机单晶涡轮叶片等[20]。我国已经用激光熔化沉积和修复制造了多种钛合金大型复杂关键金属零件,在多种型号飞机中实现装机应用,解决型号研制“瓶颈”问题[21]。其中,西北工业大学激光熔化沉积的钛合金中央翼缘条,为C919 国产大飞机的研制提供了技术储备,助力成功首飞。北京航空航天大学用激光熔化沉积技术制造的飞机大型钛合金关键结构件如图4 所示,获得2012 年度“国家技术发明奖一等奖”。
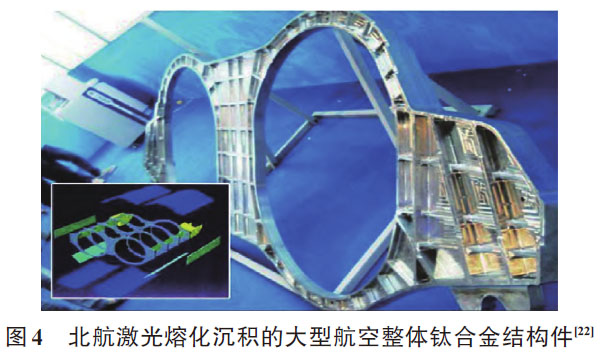
1.3 电子束熔化成形技术(EBM)
电子束熔化成形技术的成形机理与选区激光熔融技术相似,不同的是前者是在真空条件下,以电子束为能量源[23],如图5 所示。相比于SLM 和LMD技术,电子束熔化成形具有能量利用率高、加工材料广泛、无反射、加工速度快、真空环境无污染、零件内部质量较高和成形残余应力小等优点,而且在活性和脆性难加工金属复杂零部件的制造方面具有无可比拟的优势,适合成形高性能复杂金属结构功能一体化零件[24]。
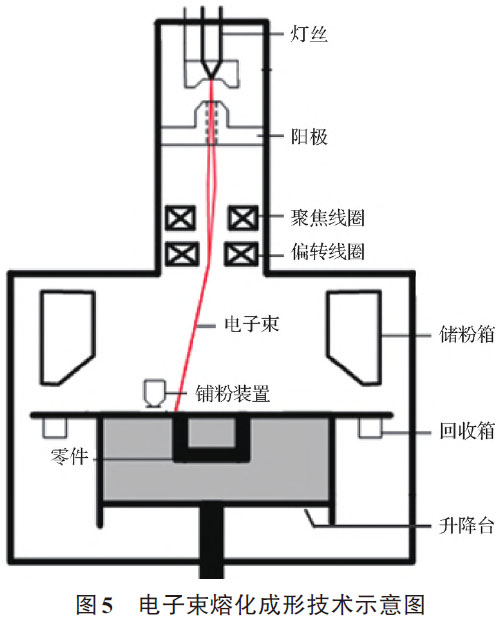
20 世纪90 年代,瑞典Arcam 公司最早开展了EBM成形设备的研究,并于2001 年申请了基于电子束进行粉床选区熔化逐层制造零件的国际专利[24-25]。目前,Arcam公司以制造EBM设备为主,产品已经商用并兼顾成形技术开发。电子束熔化成形技术在航空领域得到了广泛的应用和认可,在金属零件成形精度、效率、成本及零件性能方面有独特的优势。美国Boeing、CalRAM 公司、GE 旗下的意大利Avio 公司等针对航空发动机喷管、承力支座、起落架零件、发动机叶片等开展了大量研究,部分的零件已批量应用[26]。新型的航空飞机,常应用EBM技术成形TiAl 基金属间化合物和钛合金材料,代替传统的镍基高温合金,来达到减重的目的。
Avio 公司应用EBM技术成形脆性的TiAl 基材料,制造了结构复杂的发动机空心涡轮叶片,如图6 所示,已在新一代的航空发动机上应用,质量约为传统镍基高温合金叶片的一半,每叶片的平均制造时间仅为7 h,大量减少燃油消耗[27-29]。针对电子束选区熔化技术的开发应用,国内的清华大学和西北有色金属研究院等研制了相应的成形设备,开发了用于EBM技术的多种金属粉末,克服了零件成形过程中的粉末吹粉、球化现象和翘曲变形等问题,并制造了航空发动机增压涡轮部件和钛合金叶轮等。
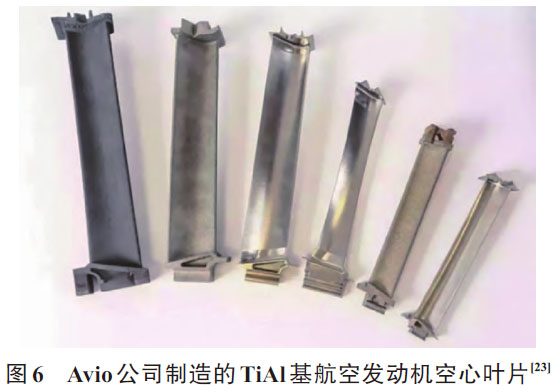
1.4 电子束自由成形制造技术(EBF)
电子束自由成形制造技术是利用高能量的电子束在真空条件下轰击金属丝材,使其熔化并按照规划的路径逐层凝固堆积,形成具有致密冶金结合的金属零件或毛坯[3],如图7 所示。电子束自由成形技术相对于铺粉和送粉增材制造技术来说,具有沉积效率高(最高可达15 kg/h),内部质量好,成形零件应力小等优点,但成形精度相对较低。可应用于
电子束自由成形的航空线材有钛合金、铝合金、不锈钢和镍基合金等。
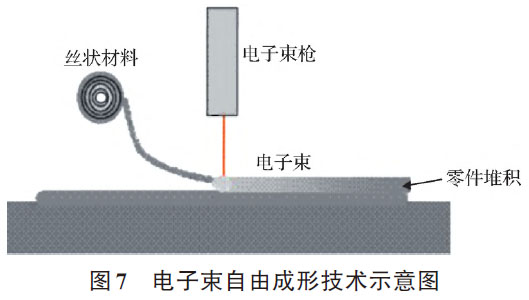
电子束自由成形制造思想最初由美国麻省理工V. R. Dave 等提出[30],美国航空航天局兰利研究中心进行开发,兰利中心应用EBF 技术制造典型的航空航天用钛合金零件,并且研制了相应的成形设备,美国Sciaky 公司将电子束自由成形设备实现商用化。Sciaky 公司将质量控制和层间实时成像与传感系统结合,能够精确感知和调整金属沉积。这种技术使Sciaky 公司能制造零件性能优良、结构形状一致的增材零件。
Sciaky 公司还联合Lockheed Martin 公司等应用EBF 技术高速打印了大型钛合金航空结构零件,如图8 所示。Lockheed Martin 公司还选定了F-35 飞机的襟副翼梁,准备用电子束熔丝沉积成形代替锻造,预期零件成本降低30%~60%[31]。国内虽与国外存在一定的研究差距,但北京航空制造工程研究所等科研机构奋起直追,不但独立研发了国内首台
电子束自由成形设备,还应用多种牌号钛合金制备了大量的航空零件和试验件,并在国内实现了装机应用[3]。
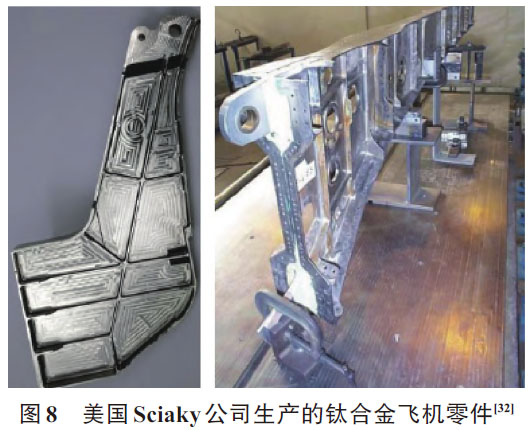
1.5 电弧增材制造技术(WAAM)
电弧增材制造是以金属丝材为原料,通过电弧提供热源熔化丝材,并逐层堆积从而形成金属复杂结构零件毛坯的近净成形技术,如图9 所示。具有沉积效率高(沉积钛和铝合金可达1 kg/h,沉积不锈钢和高强钢可达4 kg/h)、力学性能好、能量消耗低、绿色环保等优点,因此,非常适合沉积制造大型复杂金属结构零件[33]。
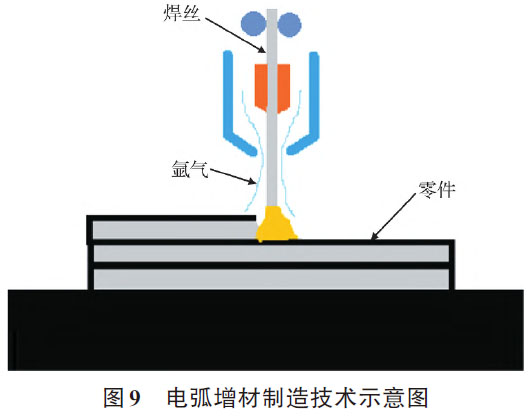
电弧增材制造思想始于20 世纪,美国人Baker利用电弧堆焊成形制造3D 打印花瓶和花篮。德国、美国、英国等发达国家随后开展了相关的研究,在计算机控制、自动化焊接和材料工艺等方面都有较高的提高和突破。开展电弧增材制造技术研究的机构包括英国克兰菲尔德大学、挪威的Norsk Titanium公司等。目前,克兰菲尔德大学开展了大量应用于航空领域的铝合金和钛合金WAAM技术研究,采用WAAM技术制造的2219 和2024 铝合金经过热处理后,克服了气孔和热裂纹的影响,性能超过了同成分的锻件水平[34]。同时,采用层间碾压可以抑制TC4 柱状晶生长,改变碾压工艺参数,可以使晶粒得到细化[35-36]。Norsk Titanium公司主要从事开发商业化的WAAM设备,并且该技术已经取得了美国联邦航空管理局(FAA)TRL8 级认证[37]。英国著名航空发动机公司罗尔洛伊斯与克兰菲尔德大学焊接工程中心开展合作,制造成形了Inconel 718飞机发动机模拟零件、钛合金机翼翼梁和起落架外翼肋等零件,图10 为克兰菲尔德大学制造的Ti6Al4V 合金机翼翼梁。近年来,电弧增材制造技术逐渐引起了国内科研机构的重视,华中科技大学、哈尔滨工业大学、首都航天机械有限公司等单位都相应开展了铝合金和钛合金的电弧增材制造研究,开发了超声波辅助电弧增材制造等新工艺,并沉积制造了航空航天用支座、框梁等典型复杂结构零件[37]。
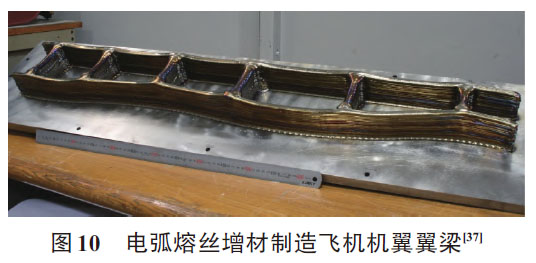
目前,世界各大著名航空公司等都大力发展和应用金属增材制造技术。比如Boeing 公司已经在无人机,F-18、F-22 战斗机上应用了增材制造技术;Lockheed Martin 公司也将要在F-35 上应用多达900多种的增材制造零件;Airbus 公司开展了集成机翼计划,并且致力于结构设计引领增材制造技术发展;美国GE公司收购了Morris 公司和Avio 公司,拥
有数百台金属增材制造设备,开展了大量关于增材制造技术的研究实验[9]。根据上文,总结了各国研究机构在航空领域应用金属增材制造的情况,如表3 所示。
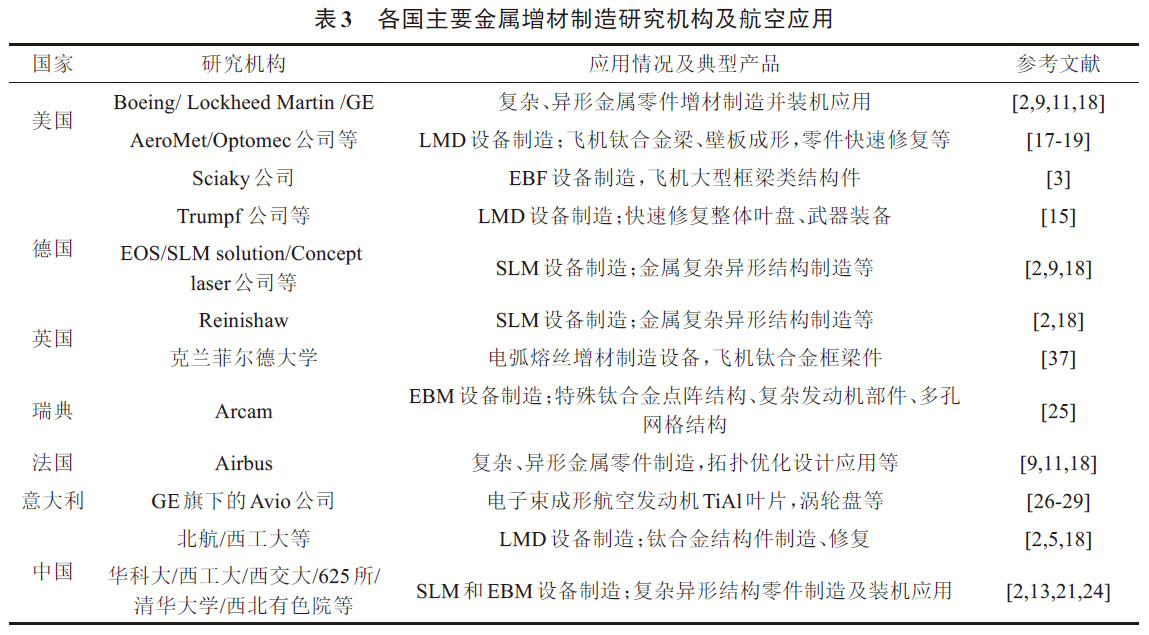
2、金属增材制造技术对航空制造业发展的重要性
金属增材制造支撑、助推航空制造业快速发展,主要体现在支撑创新设计、复杂异形结构制造、快速研制和缺陷修复等4 个方面,并具有巨大的应用前景。
(1)支撑创新设计:多年以来,在航空制造领域内制造能力决定设计结构已经成为制造业不可逾越的“潜规则”,优秀的设计方案因为制造能力不满足而不能实现的情况时有发生。理想化的最优结构,最轻质量,最小成本的结构设计通常只能存在于三维建模当中,导致最优化结构设计多年来鲜有重大突破。因此寻找一种真正意义上的柔性制造方法,为航空构件的设计制造理念插上自由翱翔的翅膀具有重大的划时代意义。金属增材制造技术突破传统制造的瓶颈,不受零件复杂程度限制,设计出即可制造出,零件设计可依据“功能最优化”原则开展,可实现航空零件的轻量化制造、点阵结构制造和多部件整体制造等[38-40]。图11 为采用金属增材制造的具有空心网格结构的航空发动机叶片和经过拓扑优化后的航空结构件。金属增材制造使这些优化的设计方案得以实现,达到减少航空材料使用量,降低制造时间和成本的作用。
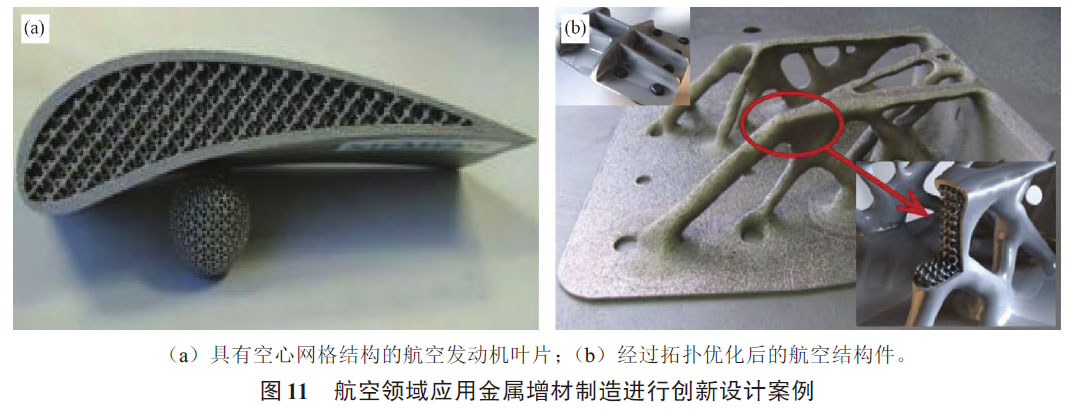
(2)复杂异形结构制造:复杂构件通常外形复杂,整体工艺刚性较差,同时对力学性能也要求很高,导致采用传统加工制造技术制备成形非常困难。采用铸造技术,尽管可以满足成形需求,但是性能通常都不太理想,难以满足先进飞机关键承力件的设计要求。采用锻造技术,整体制造航空零件则成形难度大,后续需要大量的机械加工,总体生产制造周期非常长。而增材制造不受零件外形轮廓和复杂程度约束,成形零件的强度也能够基本满足航空零件的设计要求[41-42]。另外,一些需多个部件配合的航空零件,增材制造可以整体一体成形,因此减小了机械配合带来的零件磨损和应力集中现象。图12 为英国制造技术中心MTC采用电子束熔化成形技术整体成形的航空航天复杂异形液压歧管,采用增材制造技术显著减少了零件的整体质量,提高了液体流动效率,减少了泄露风险。
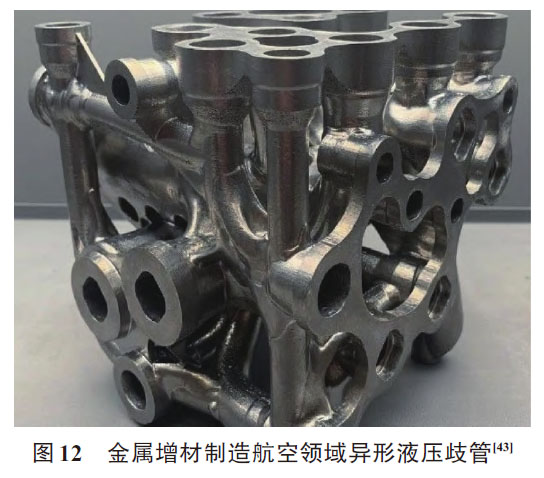
(3)实现产品快速研制:增材制造技术是一项制造周期短、成形效率高、无需模具、近净成形、可实现数字化快速制造的先进技术,能够直接根据数模快速成形一体化制造多材料、高性能的航空航天难加工复杂构件,具有快速响应的优势。现代新型飞机为减轻机体质量和提高机体寿命,常采用大型整体金属结构。传统的锻造辅助机械加工制造方式,即使花费高昂的模具费和较长的制造周期也难以满足新研机型的研制需求[44]。金属增材制造在研制过程中无需模具,大大降低研制成本,解决了航空航天构件快速研制的急迫技术问题。图13 为C919 大型客机及其Ti-6Al-4V 钛合金主风挡窗框,原始制造周期2 年(欧洲公司),需要200 万美元模具费。北航利用激光增材制造技术仅55 天就制造完成该部件,并已经实现装机验证应用[5,45]。由此可见,为保证研制速度,同时适应研制阶段设计不断更改、试验方案需要验证的情况,新型飞机研制急需增材制造这种无模具制造技术。
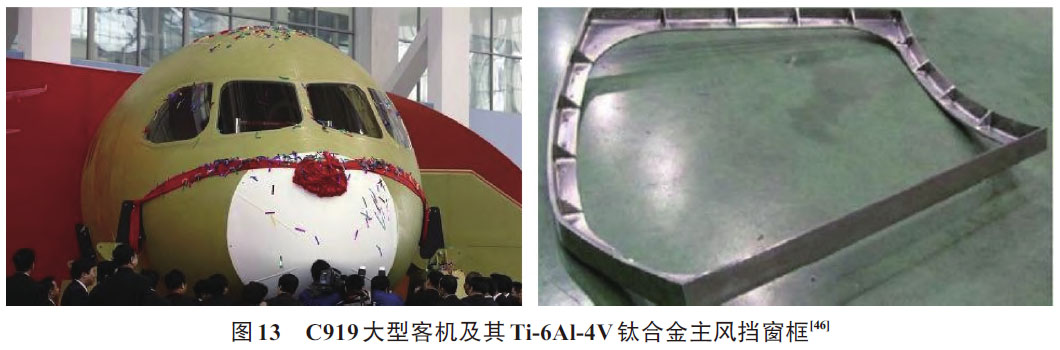
(4)零件修复:航空航天结构件不断大型化、整体化,零件价值高,如飞机整体钛合金框仅毛坯就数百万,在加工过程中,常常因为铣刀掉刀产生失误造成报废,造成巨大的经济损失。还有的飞机零件在使用和服役过程中因承受较大载荷而产生磨损和腐蚀等缺陷,应用LMD 技术都可以得到快速修复。采用激光修复损伤加工缺陷,对于航空航天企业来说是提高经济效益的重要手段。随着激光修复技术的发展,现在已经成功应用于形状更加复杂、工作环境和可靠性要求更高的航空零件上,如大型钛合金框梁、接头结构件,发动机叶片、叶盘,镍基合金高压涡轮,不锈钢起落架等的修复[47]。其中,北京航空材料研究院采用激光修复技术,针对第三代战机、伊尔76 飞机的超高强度钢起落架、不锈钢轴颈、钛合金襟翼滑轨等承力构件开展修复研究工作,修复的部分零件已经通过装机评审和应用[48]。
如图14 所示,经过修复的伊尔76 飞机超高强度钢起落架,修复后状态良好,已经获得批量应用。
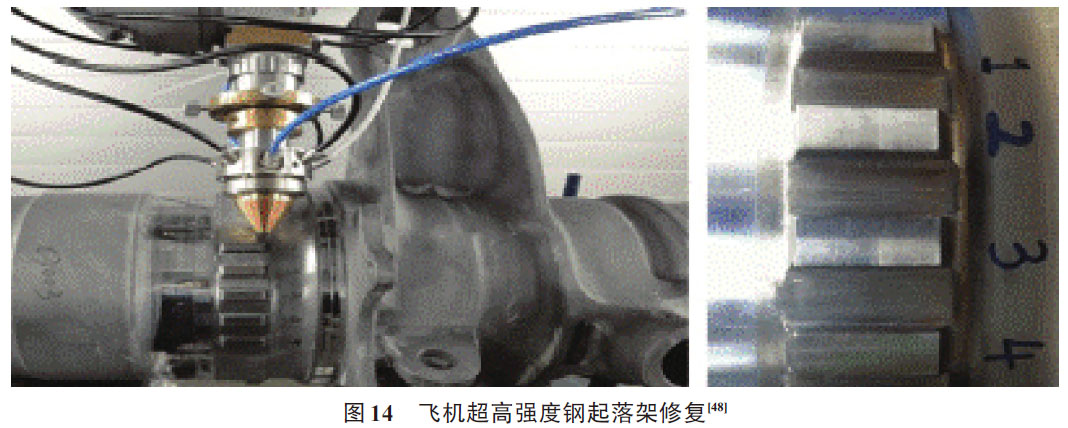
3 、结论与展望
金属增材制造技术改变了传统的制造方式,能够直接、快速制造金属结构功能零件,尤其对难加工复杂异形结构的制造具有巨大优势,在国内外航空制造加工领域得到了迅速发展,对我国航空工业的发展具有重要的价值和意义。
为了推进增材制造技术在航空领域的深入应用,促进协作交流,我国航空领域更应该对金属增材制造技术投入大量技术创新和资金支持,并在以下方面进行筹备:
(1)推进“产学研结合”,从原材料、设计、制造、检测等全方面入手,形成航空领域面向增材制造的全流程技术体系。拓展金属增材制造技术在航空制造领域的应用范围,延伸产业链,提高产业化程度;
(2)加强金属增材制造设备和材料、工艺等基础机理和科学问题研究,制定与完善相关标准规范。进而降低成本、提高成形精度和性能、增加材料种类和使用范围,最终提升航空产品的性能和服役时间;
(3)从航空制造领域设计的源头出发,在满足航空零件性能和服役条件的情况下,实现功能性优先的设计,使金属零件向轻量化和整体化方向发展,设计引领并推动增材制造技术不断突破和发展。
参考文献:
[ 1 ] 刘铭, 张坤, 樊振中. 3D打印技术在航空制造领域的应用进展[J]. 装备制造技术, 2013,(6):232.
[ 2 ] 顾东东, 张红梅, 陈洪宇, 等. 航空航天高性能金属材料构件激光增材制造[J]. 中国激光, 2020,47(5):1.
[ 3 ] 巩水利, 锁红波, 李怀学.金属增材制造技术在航空领域的发展与应用[J].航空制造技术, 2013,(13):66.
[ 4 ] Kumar S, Selective Laser Sintering/Melting[J]. ComprehensiveMaterials Processing, 2014,10:93.
[ 5 ] 王华明. 高性能大型金属构件激光增材制造:若干材料基础问题[J]. 航空学报, 2015,35(10):2690.
[ 6 ] Murr L E, Gaytan S M. Electron Beam Melting[J]. ComprehensiveMaterials Processing, 2014,10:135.
[ 7 ] Taminger K M B, Hafley R A. Electron Beam Freeform Fabrication:A Rapid Metal Deposition Process[C]//Proceedings ofthe 3rd Annual Automotive Composites Conference. Troy:Societyof Plastics Engineers, 2003:1.
[ 8 ] WANG F D, Williams S, Colegrove P, et al. Microstructure andMechanical Properties of Wire and Arc Additive ManufacturedTi-6Al-4V[J]. Metallurgical and Materials Transactions A,2013,44:968.
[ 9 ] 林鑫, 黄卫东. 应用于航空领域的金属高性能增材制造技术[J]. 中国材料进展, 2015,34(9):684.
[ 10 ] 柳朝阳, 赵备备, 李兰杰, 等. 金属材料3D打印技术研究进展[J]. 粉末冶金工业, 2020,30(2):83.
[ 11 ] SHI G H, GUAN C Q, QUAN D L, et al. An aerospace bracketdesigned by thermo-elastic topology optimization and manufacturedby additive manufacturing[J]. Chinese Journal of Aeronautics,2020,33(4):1252.
[ 12 ] 周伟民, 夏张文, 王涵, 等. 仿生增材制造[J]. 微纳电子技术,2018,55(6):438.
[ 13 ] 黄卫东. 材料3D 打印技术的研究进展[J]. 新型工业化, 2016,6(3):53.
[ 14 ] 张安峰, 李涤尘, 卢秉恒. 激光直接金属快速成形技术的研究进展[J]. 兵器材料科学与工程, 2007,30(5):68.
[ 15 ] 杨胶溪, 柯华, 崔哲, 等. 激光金属沉积技术研究现状与应用进展[J]. 航空制造技术, 2020,63(10):14.
[ 16 ] Arcella F G, Froes F H. Producing titanium aerospace componentsfrom powder using laser forming[J]. Journal of Metals,2000,52(5):28.
[ 17 ] Lewis G K, Schlienger E. Practical considerations and capabilitiesfor laser assisted direct metal deposition[J]. Materials andDesign, 2000,21(4):417.
[ 18 ] 林鑫, 黄卫东. 高性能金属构件的激光增材制造[J]. 中国科学:信息科学, 2015,45(9):1111.
[ 19 ] 朱忠良, 赵凯,郭立杰, 等. 大型金属构件增材制造技术在航空航天制造中的应用及其发展趋势[J]. 电焊机, 2020,50(1):1.
[ 20 ] 刘业胜, 韩品连, 胡寿丰, 等. 金属材料激光增材制造技术及在航空发动机上的应用[J]. 航空制造技术, 2014(10):62.
[ 21 ] Abbott D H, Arcella F G. Laser forming titanium components[J]. Advanced Materials and Processes, 1998,153(5):29.
[ 22 ] 杨强, 鲁中良, 黄福亨, 等.激光增材制造技术的研究现状及发展趋势[J]. 航空制造技术, 2013,(13):66.
[ 23 ] 冉江涛, 赵鸿, 高华兵, 等. 电子束熔化成形技术及应用[J]. 航空制造技术, 2016,(12):26.
[ 24 ] 汤慧萍, 王建, 逯圣路, 等. 电子束熔化成形技术研究进展[J].中国材料进展, 2015,34(3):225.
[ 25 ] 郭超, 张平平, 林峰, 等. 电子束选区熔化增材制造技术研究进展[J]. 工业技术创新, 2017,4(4):6.
[ 26 ] 宋文涛, 李晓光, 曲伸, 等. 增材制造技术在航空发动机中的应用展望[J]. 航空制造技术, 2014(增刊):16.
[ 27 ] 王忻凯, 王乾俸. 增材制造及其航空航天领域的发展现状[J].中小企业管理与科技, 2015,(35):230.
[ 28 ] GE 考虑3D 打印波音最新777X 客机发动机部件[EB/OL].[2014-8-7]. http://www. 3dimperial. com/imperial/front/news/informationView/
smallCategoryId/2/id/5036.
[ 29 ] 郭超, 张平平, 林峰. 电子束选区熔化增材制造技术研究进展[J]. 工业技术创新, 2017,4(4):6.
[ 30 ] Dave V R, Matz J E, Eager T W. Electron beam solid freeformfabrication of metal parts[C]//Proceedings of the solid freeformfabrication symposium, East Hart-ford, USA: Pratt & Whitney,1995:64.
[ 31 ] Lockheed Martin and Sciaky, Inc. Enter mentor-protege agreementwith initial focus on electron beam manufacturing of F-35parts[EB/OL]. [2011-10-30]. https://www. prnewswire. com/news-releases/lockheed-martin-and-sciaky-inc-enter-mentorprotege-agreement-with-initial-focus-on-electron-beam-manu ‐
facturing-of-f-35-parts-134752438.
[ 32 ] 关桥. 焊接/连接与增材制造(3D打印)[J]. 焊接, 2014(5):1.
[ 33 ] Willams S W, Martina F, Addison A C, et al. Wire+arc additivemanufacturing[J]. Materials science and technology,2016,32(7):641.
[ 34 ] Martina F, Mehnen J, Williams S W, et al. Investigation of thebenefits of plasma deposition for the additive layer manufacturing of Ti-6Al-4V[J]. Journal of Materials Processing Technology,2012,212(6):1377.
[ 35 ] BAI J Y, FAN C L, LIN S, et al. Mechanical properties and fracturebehaviors of GTA-additive manufactured 2219-Al after an especial heat treatment[J]. Journal of Materials Engineering andPerformance, 2017,26(4):1808.
[ 36 ] GU J L, DING J L, Williams S W, et al. The effect of interlayercold working and post-deposition heat treatment on porosity in additively manufactured aluminum alloys[J]. Journal of MaterialsProcessing Technology, 2016,23(4):26.
[ 37 ] 李权, 王福德, 王国庆, 等. 航空航天轻质金属材料电弧熔丝增材制造技术[J]. 航空制造技术, 2018,61(3):74.
[ 38 ] Heinz A, Haszler A, Keidel C, et al. Recent development in aluminium alloys for aerospace applications[J]. Materials Scienceand Engineering A, 2000, 280:102.
[ 39 ] 胡娟, 高银涛, 冒浴沂, 等. 激光粉末床熔融金属制件孔隙缺陷研究现状[J]. 粉末冶金工业, 2021,31(6):87.
[ 40 ] Panesar A, Abdi M, Hickman D, et al. Strategies for functionally graded lattice structures derived using topology optimisation for additive manufacturing[J]. Additive Manufacturing, 2018(19):81.
[ 41 ] HUANG W D, LIN X. Research progress in laser solid formingof high-performance metallic components at the state key laboratory of solidification processing of China[J]. 3D Printing andAdditive Manufacturing, 2014(1):156.
[ 42 ] 吴文恒, 张亮, 卢林. 选区激光熔化成形Al 系高熵合金的研究进展[J]. 粉末冶金工业, 2021,31(4):1.
[ 43 ] Part-1-深入剖析为增材制造而重新设计的航空航天液压歧管[EB/OL]. [2021-9-30]. https://www. sohu. com/a/493030990_274912.
[ 44 ] Bourell D L, Rosen D W, Leu M C. The roadmap for additive manufacturing and its impact[J]. 3D Printing and Additive Manufacturing,2014,(1):6.
[ 45 ] 胡晓睿. 增材制造技术在国防领域的应用[J]. 全球纵览,2010,8(4):40.
[ 46 ] 张讯, 葛建彪. 激光增材制造技术在民机复杂结构上的应用及研究[J]. 应用激光, 2018,38(6):1022.
[ 47 ] Tancogne-Dejean T, Spierings A B, Mohr D. Additively-manufactured metallic micro-lattice materials for high specific energy absorption under static and dynamic loading[J]. Acta Materialia,2016, 116:14.
[ 48 ] 杨爱民, 秦仁耀, 张国栋, 等. 飞机金属零件焊接及增材制造修复研究与应用现状[J]. 电焊机, 2021,51(8):79.
相关链接