引言
钛金属在地壳中的储量十分丰富。钛及其合金因具有低密度、高比强度、耐高温、耐腐蚀及可焊性好等优点,已被广泛应用于航空航天、能源工业、船舶制造、生物医疗及武器装备等领域[1-2]。特别是在航空航天领域,钛合金凭借其轻质高强的性能优势,拥有比其它金属材料更加重要的地位,并已成功加工制造出航空发动机叶片、飞机弹簧和燃油泵叶轮等关键部件[3-4],如图1a所示。然而随着航空航天工业的进一步发展,钛合金的服役温度从最初的300~400℃逐渐提高至600℃及以上,这对钛合金的结构承载能力提出了更加苛刻的要求。鉴于此,相关科研工作者尝试向钛合金中添加一些其他合金元素,如硅、钼和稀土元素等,用于提高钛合金的服役温度[5-6]。
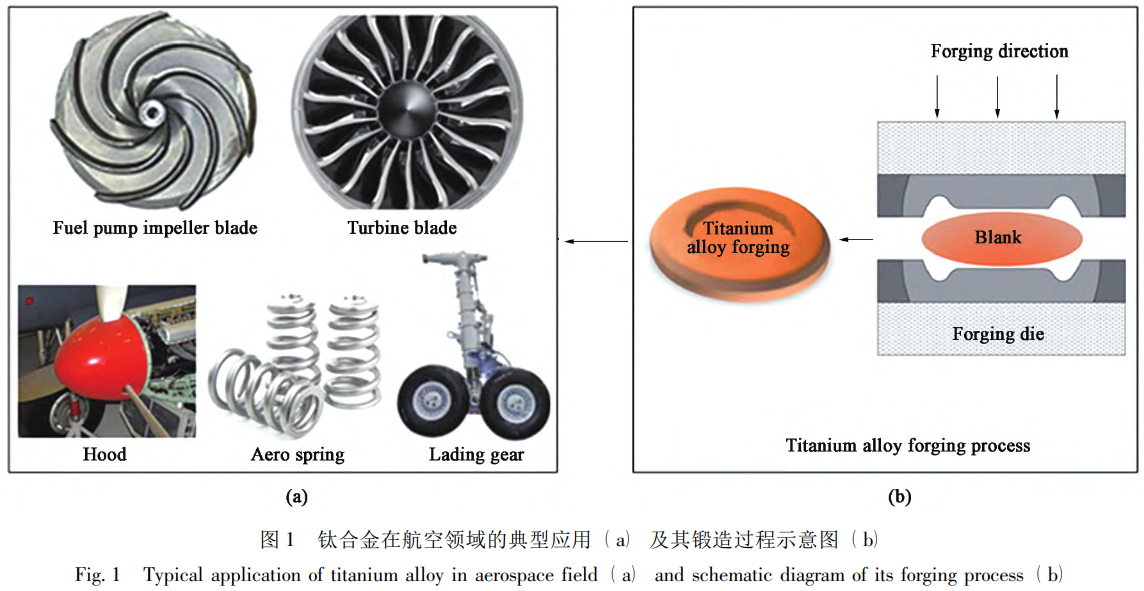
然而研究结果表明仅通过添加元素成分对提升钛合金综合性能具有极大的局限性,且会对钛合金的后续加工及回收产生巨大的影响。考虑到钛合金的成形及性能特点,采用合理且有效的热加工工艺是实现钛合金组织和性能调控的重要手段,也是制造钛合金精密的大型框架结构件的有效途径[7]。
锻造是能够同时实现钛合金控形和控性的成形方式之一[8]。据统计,80%以上的航空发动机钛合金叶片均是由锻造成形而获得[9]。图1b是钛合金典型的锻造过程示意图。钛合金铸锭先被加热到一定温度并保温一段时间,随后将其置入模具中,在外加压力的作用下,一些铸造缺陷在锻造过程中消除。同时,由于钛坯发生剧烈的塑性变形,晶粒变得细化且相对均匀[10]。据文献[11]报道,锻造成形可以使钛合金的晶粒尺度达到微米级甚至亚微米级别,且使其具有优异的力学性能。然而,由于钛合金存在导热性能差、变形抗力高及易高温氧化等问题,增加了其锻造工艺的设计及优化的难度。此外,钛合金成形窗口窄,进一步限制了其锻造工艺的把控,最终导致钛成品件具有极高的生产成本[12]。因此,合理且有效的优化锻造工艺对提高钛合金的实际应用价值具有重要意义。本文将较系统性地综述航空用钛合金锻造工艺研究进展,通过归纳并介绍了钛合金锻造的几种典型工艺,结合钛合金锻造工艺参数对微观组织及力学性能的影响,提出能够兼顾钛合金组织、性能、成本及生产效率的策略及展望,这些方法为钛合金热加工技术的发展提供了重要的研究思路和方向。
1、钛合金的锻造工艺概述
钛合金构件常采用热模锻成形获得。钛坯在锻造时的成形温度一般高于再结晶温度,该情况下钛合金具有较好的流动性及成形能力,且可以有效地克服其变形抗力[13-14]。若根据模具和锻件的温度是否相同将锻造工艺进行分类,可分为非等温锻造和等温锻造。
1.1非等温锻造
非等温锻造包括常见的自由锻、模锻等,以这种锻造方式成形时,模具或砧板温度低于锻件温度,一般约为锻件温度的10%~35%[14]。较低的模具温度不仅可以增加模具材料的选择范围,还能降低模具成本并提高锻造效率。如KIMJY等[15]研究了Ti-6Al-4V钛合金非等温多步锻造及组织演变规律,如图2所示。他们先将Ф40mm×60mm的圆柱形铸锭加热至940℃保温30min,随后将铸锭转移出炉并沿高度方向下压20mm,再经过反复翻转及锻打,获得所需形状,其具体过程如图2a和图2b所示。
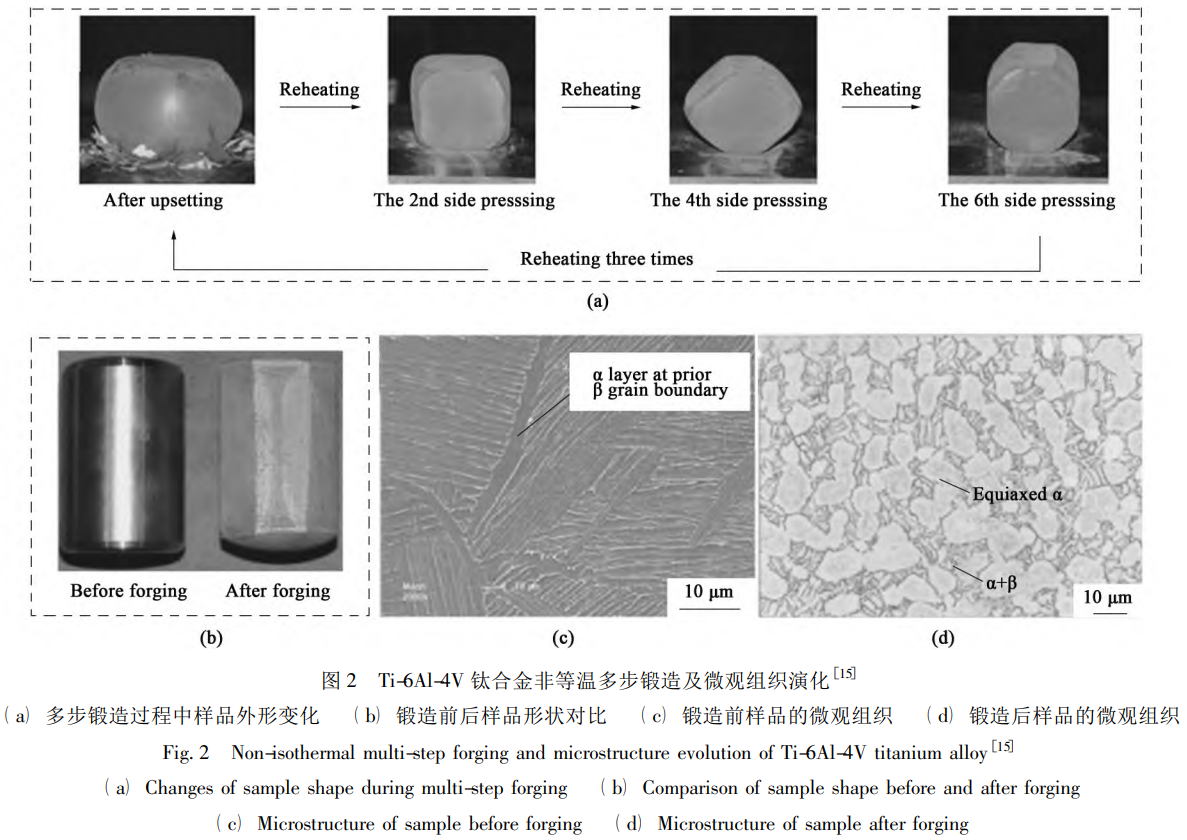
整个锻造过程中模具温度均维持在350℃。由图2c可知,锻造前该合金的微观组织表现出典型的魏氏组织形态,其中原始β晶粒的晶界清晰可见;而锻后的微观组织是由含量超55%的等轴α相、少量粗大片状α相及残余β相所构成的等轴组织,如图2d所示。
在非等温锻造过程中,钛合金坯料上的瞬态温度变化极其复杂,目前尚未有被认可的理论模型用于预测。因锻件及模具的复杂性,将锻件的瞬态温度与时间相关联十分困难。有限元软化的开发与应用对钛合金热模锻工艺的设计及优化起着重要作用,其可以预测合金锻造过程中实时的场域及组织演变过程[16-17]。目前,不少学者将其与一些相关的理论模型相结合,用于制定更加合理的热加工工艺[18-19]。有限元模拟还可以预测钛合金在锻造过程中的残余应力分布,且研究结果表明[20],锻件的径向残余应力沿中心轴呈对称分布,锻件表面受拉应力作用,而心部表现出明显的应力集中,并呈压应力状态,且锻件上的残余应力与锻造温度成反比,与变形量呈正比。
尽管采用非等温锻造而获得的某些钛合金结构件也得到了相对较好的应用,但这种锻造方式易使钛合金锻件表面形成显著的硬脆层[21-23]。这种硬脆层是由富氧α层及钛的氧化皮构成,其会造成钛合金组织均匀性较差且塑性大幅度降低。即使在锻造前锻坯表面涂覆防氧化材料,但仍然会在锻件某些部位形成较厚的硬脆层。此外,某些钛合金在采用非等温锻造成形时还会出现一种典型的组织现象,即冷模组织[24-25],这种组织会导致钛合金性能下降。虽可以在后续的机加工过程中切除了该组织,但这不仅会破坏锻造时的金属流线,还会造成极大地浪费,进而增加了加工成本。钛合金在进行非等温锻造时,坯料与模具各个部位接触时间不同,不同区域的实际变形温度也不同,即使采用有限元仿真模拟也无法十分准确地预测每个区域的温度变化,进而导致这些区域的组织演化和性能改变也无法精准判断。
为避免采用非等温锻造成形的钛合金锻件中出现冷帽、剪切带或不均匀的残余应力等问题[26],故在对钛坯进行非等温锻造成形时常要求工件形状相对简单,同时需降低温度变化梯度且减小预制件的长宽比。然而,较大、大型或超大型钛合金锻件是当前的重要需求,也是未来钛合金发展的主流趋势之一,但考虑到压机承受能力等,单次模锻无法达到预期形状,这类锻件多采用多火次成形才能获得预期形状及尺寸。这种情况下,每一火次的进出炉均需要高昂的加工成本。传统的分割式锻造成形虽无需过高的承载要求,但各部位锻件焊接拼合整体工件时仍存在诸多问题,一体化锻造成形也是当前针对这类锻件的主流之一。
1.2等温锻造
20世纪90年代中期,SALISHCHEVA等[27]提出一种新的锻造方式,即等温锻造。采用该方法可制备出具有超细晶的金属坯料,该工艺在实施时需将模具加热到与坯料相同的变形温度并以较低的变形速率实现锻造成形。与非等温锻造相比,等温锻造可以在比较窄的温度窗口下获得所需锻件,能够一步完成形状复杂、薄壁或高刚度的锻件成形,同时消除冷帽、剪切带和冷模组织等缺陷且大大降低材料应变硬化的影响,实现金属的净成形或近净成形。由等温锻造获得的合金构件显微组织更加均匀,机械性能更好[28]。因此,等温锻造较适用于形变比较困难的金属,如钛合金、γ-TiAl合金等[29],可用于生产发动机等处于高温工况下的构件。根据加载方式的不同,可将等温锻造进一步划分为单向等温锻造和多向等温锻造[22,30-31]。
1.2.1单向等温锻造
单向等温锻造是金属材料沿着同一个方向进行单次或多次等温锻造的工艺。通常,单向等温锻造的应变速率比较小,通过不断增大坯料的变形量,进而获得所需锻件形状及性能[14]。锻造后工件的显微组织及性能均会受合金成分、锻造温度及应变速率的影响。钛合金经单向等温锻造后的微观组织常表现为等轴组织的特征,同时合金的塑性和抗拉强度均有一定的提高[28]。
李凯等[32]研究了锻造温度对TC11钛合金在α+β相区单向等温锻造过程中微观组织演变,结果表明锻后初生α相呈等轴状或近似等轴状,其含量与等温锻造温度呈反比,而β转变组织与等温锻造温度呈正比,这导致锻后该合金经过退火后的塑性及强度均有升高。此外,随着锻造温度的升高,锻后微观组织由等轴组织向双态组织转变,且整体来说,TC11钛合金经等温锻造后,微观组织均匀性明显增强。相比之下,常规单向锻造后微观组织均匀性相对比较弱,与FANGXR等[33]的研究结果一致。此外,单向等温锻造在变形过程中会形成变形织构,造成锻后合金出现各向异性[34],进而限制这种锻造工艺的应用。若锻件尺寸相对较大或形状相对较复杂,仅采用单方向的等温锻造或许无法充分成形,进而造成锻件组织和性能相对不均匀。
1.2.2多向等温锻造
多向等温锻造是一种多应用于大坯料发生超塑性变形的工艺,在该工艺的实施过程中,坯料的加载方向不断发生变化,最终获得所需成品件。该工艺不仅可以有效消除变形“死区”,还能大幅度降低各向异性,进而使成形件在各个方向的组织及性能更加均匀[35-36]。如ZHANGZX等[37]研究了铸态Ti-6Al-4V钛合金在多向等温锻造过程中的微观组织演变及力学性能,发现三步多向等温锻造能够获得均匀且细小的等轴组织,其中α相尺寸约为1.9μm,且锻造过程中组织演变机制为连续动态再结晶和不连续动态再结晶。同时,他们还发现微观组织的再结晶百分数及组织均匀性与锻造翻转次数均呈正相关。此外,经多向等温锻造后,铸态Ti6Al-4V钛合金的室温及400℃的力学性能显著提高,且拉伸断裂机制由锻前的脆性断裂转变为韧性断裂。
多向等温锻造的应用范围相对较广,其不仅适用于合金元素比较少的Ti-6Al-4V钛合金,还适用于铝元素含量超过40%的γ-TiAl合金[14,38-40]。ZHUK等[40]研究了Ti-44Al-4Nb-1.5Cr-0.5Mo-0.2B合金的多向等温锻造过程及组织演变,如图3所示,所采用的具体锻造工艺如下:将Ф60mm×100mm的铸锭升温至1200℃并保温2h,沿高度方向分两次锻造获得高度为40mm的圆坯。为释放锻造过程中产生的内应力,将圆坯在1100℃下保温1h,随后圆坯翻转90℃,并在1100℃的温度下锻造,高度变为30mm,锻造工艺如图3a所示。该合金经第1次多向等温锻后的微观组织由约90.1%的γ相、1.5%的α2相及8.4%的β/B2相组成,如图3b所示(RL、KL、FG和CG分别表示剩余的片层α相、弯曲的片层α相、细小的晶粒和粗大的晶粒),经1100℃退火后,微观组织由长条状转变为等轴状,其中α2相明显增多,如图3c所示。经第2次多向等温锻后,该合金中发生α2+γβ/B2转变,并造成β/B2相含量增加,如图3b和图3d所示。整个锻造过程中,晶粒更加均匀且尺寸明显降低,即由初始的3.6μm减小至1.6μm。
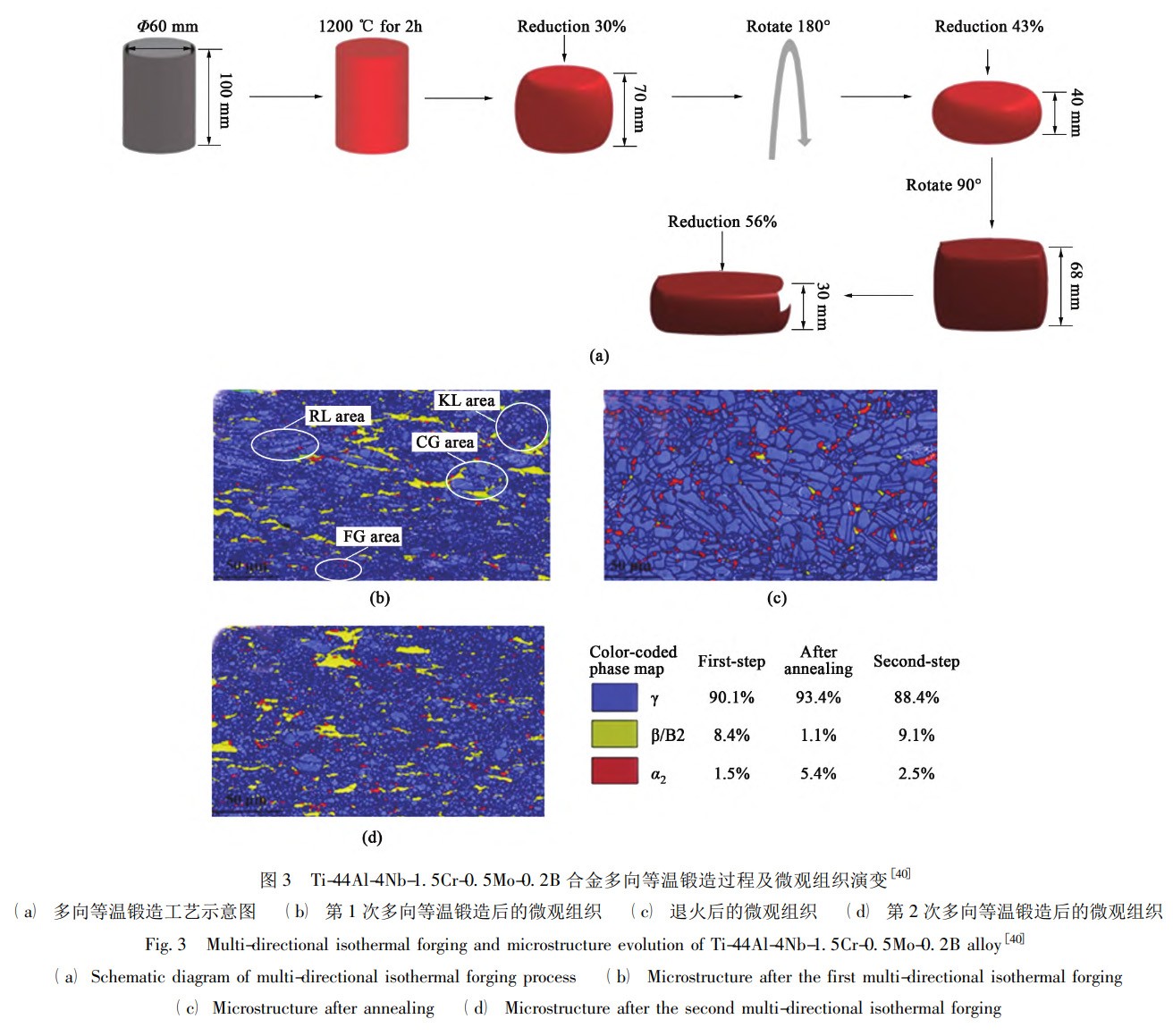
多向等温锻造仅需改变锻件变形方向,即可获得细小且均匀的等轴组织。多方向变形而累积的应变可以加快金属材料的再结晶行为,从而提高材料的性能[37]。多向等温锻造表现出巨大的潜在工业化应用价值,该工艺合理且有效的应用能够为生产精密的高端锻件提供保障[41]。但等温锻造的应用也受到模具材料等限制,较高的锻造温度对模具高温工况下的承载能力也提出了更苛刻的要求,模具的加工制造、维修保养也需投入较多的成本。
2、锻造工艺参数设计
在锻造过程中,影响钛合金锻件微观组织及性能的因素有模具设计、锻造温度、变形量、应变速率及冷却方式等[14,42-43]。合理调控这些锻造工艺参数不仅可以获得良好的微观组织及优异的力学性能,还可以为优化钛合金锻造工艺提供思路及参考。在锻件外形及尺寸确定的情况下,上述参数中锻造温度、变形量和应变速率是影响锻件最终质量的最关键的3个因素。本章将围绕这3个因素的合理选择进行讨论。
2.1锻造温度
钛合金具有很强的温度敏感性,因其热导率较低,故其微观组织极易受到温度的影响[44]。尤其是在变形过程中,变形温度对钛合金流变应力的影响更加明显,而组织状态决定合金性能[43-44],故合理把控变形温度与流变应力及微观组织间的关联关系对设计钛合金锻造工艺窗口具有重要意义。
以钛合金相变点,即β转变温度Tβ为分界点,根据锻造温度的不同,将钛合金锻造方法分为两大类:β单相区锻造及α+β两相区锻造,与之对应的锻造温度范围分别为(Tβ+20)~(Tβ+50)℃及(Tβ-30)~(Tβ-50)℃[45-46]。经前述两种锻造方法所获得锻件的微观组织具有显著的区别。对α+β两相钛合金而言,随着锻造温度的升高,锻件微观组织通常由等轴组织变为网篮组织,最后变为典型的魏氏组织[47]。JACKSONM等[48]采用两种不同的锻造方式研究了Ti-10V-2Fe-3Al钛合金在等温锻造过程中的塑性流动行为及组织演变,结果表明该合金经β单相区锻后微观组织中原始β晶粒的晶界清晰可见,且原始β晶粒内分布着簇状的片状α相及少量的残余β相,该组织也被称为魏氏组织;而经α+β两相区锻造后的微观组织中初生α相形态主要为等轴状及长条状,其含量约为50%。此外,他们继续对两种锻造方法所获得的样品在两相区进行等温压缩进行实验后发现,经β锻的样品峰值应力更大且表现出显著的流变软化现象。
虽然等轴组织具备良好的热稳定性、室温塑性及抗高周疲劳性能,但其断裂韧性、热强性及抗疲劳裂纹扩展能力较差,而双态组织具备比等轴组织更加优异且均衡的综合性能。基于该目的,相关学者提出了近β锻造工艺,即进一步提高α+β两相区锻造温度,使坯料处于约(Tβ-15)℃进行变形,锻后水或油淬[46]。经近β锻后的钛合金中初生α相含量约20%,微观组织为双态组织,也被称为混合组织[14]。
田伟等[49]研究了锻造温度及退火工艺对TC17钛合金微观组织演变规律的影响,如图4所示。结果表明,该合金在α+β两相区锻造时,初生α相呈现出动态再结晶特征,即α相颗粒发生扭曲及碎化等,而高温变形状态下β晶粒受α相颗粒的限制,退火后微观组织为等轴组织,少见原始β晶粒的晶界,如图4a所示;与α+β两相区锻造相比,近β锻造后微观组织呈现出双态组织的特征,其中初生α相含量明显降低,约为20%,而原始β晶粒尺寸相对更大,退火后晶界清晰可见,原始β晶粒中析出大量片层α相,如图4b所示;图4c所示是β单相区锻后的微观组织形态,因锻造过程中引入大量的晶体缺陷,退火过程中片层α相沿特定的晶体学方向析出,并呈现散乱、交错分布的特点。ZHOUYG等[50]通过研究TC11钛合金的近β锻造工艺,使TC11钛合金的强度、塑性及断裂韧性达到平衡状态,且成功将该工艺推广到多种类型钛合金上,并已应用到航空发动机压气机盘、转子及其他飞机部件的生产上。
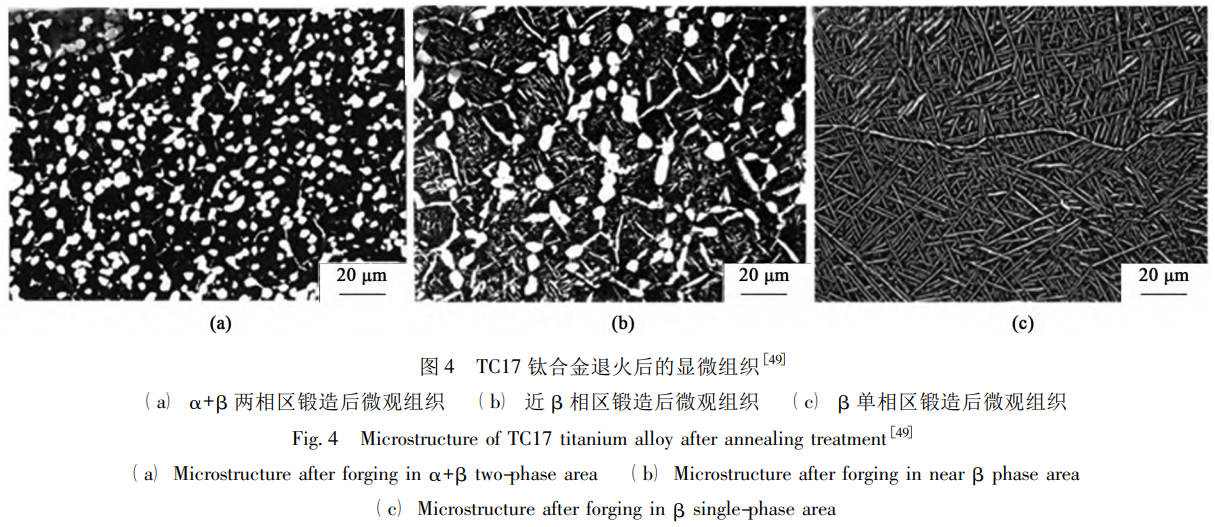
除近β锻造工艺之外,跨相区锻造工艺也开始被大家关注,该工艺一般需要分火次在β相区和α+β两相区进行跨相区多火次锻造成形,适合大型结构模锻件[46,51]。成形件的微观组织受α+β两相区的温度范围及变形程度控制。当变形量较小时,微观组织由片状α相、等轴状α相及残余β相混合构成,且均匀性较差;当变形量较大(超过50%)时,跨相区锻造所获得的组织类似于常规的α+β两相区锻造所获得的组织形态。两者的区别在于:前者中,β晶粒不同部位承受不同的变形,而后者中整个晶粒体积承受相同的变形。故跨β锻造中晶界α相优先在β晶界除形核,故其会更充分地变形,且优先发生破碎、球化[46,52]。黄定辉等[53]研究发现TC18钛合金在跨相区锻造时,其抗拉强度随α+β两相区变形量的增加呈现出先增加后降低趋势,且α+β两相区变形量约20%~30%时达到最大。此外,文中还提出可以获得强度、塑性及冲击韧性优良搭配的工艺,即(Tβ+20)℃且变形量超过35%,(Tβ-30)℃且变形量小于30%。
目前,β单相区锻造及α+β两相区锻造仍是应用较为广泛的两种锻造工艺。针对β单相区锻造而言,锻造温度较高,钛合金的变形抗力较小,锻造过程中所使用的火次也较少,在实际生产中可以加快加工生产效率,进而提高经济效益,但β单相区锻造组织不容易控制。通常,相变点较高的(近)α型钛合金终锻基本不采用β单相区锻造,高合金化的近β钛合金常采用该工艺进行锻造[46]。而α+β两相区锻造虽是钛合金使用最多的一种锻造工艺,但不可避免地出现一些组织及性能问题,而新兴的近β锻造和跨相区锻造凭借优良的表现,在提高钛合金综合性能方面具备极大潜力。目前,这两种锻造工艺仍存在较多的问题,如近β锻造的锻造温度窗口更窄且难以实现准确控温,跨相区锻造后的钛合金需要合金化或其他后续处理进行组织调控。然而,这两种锻造工艺均可获得强度、塑性及韧性等最佳匹配,能够为进一步提高钛合金的综合性能提供研究方向。
2.2应变速率
钛合金除了具有强烈的温度敏感性,还具有较强的应变速率敏感性,变形过程中应变速率的高低会对钛合金的变形抗力及微观组织产生巨大影响[54-56]。一般情况,钛合金采用较低的应变速率进行热变形时,流变应力较低,组织相对均匀;而在高应变速率下热变形时,流变应力较高,组织均匀性相对较差。故低应变速率下变形常被作为提高钛合金加工性能的手段之一[57]。
虽然低应变速率下变形抗力更低,组织也相对均匀,但这是基于温度不变甚至变化很小的前提下。故在实际生产中,选择应变速率前需考虑锻造成形方式。此外,钛合金在热模锻时容易产生残余应力,残余应力容易造成工件出现变形甚至开裂等问题。文献[20]的研究表明,在非等温锻造过程中,随着变形速度的增大,锻件残余应力减小,当变形速度增加到一定程度时,残余应力的影响大幅度降低甚至消失。
而在等温锻造过程中,较低的应变速率下,可以获得更加均匀的组织及优异的性能,尤其是多向等温锻造还可以消除变形死区且进一步提高组织均匀性[14,35]。
SUY等[58]研究了不同锻造工艺参数对DsTi700钛合金变形行为及显微组织演变的影响,如图5所示。研究结果表明,随着应变速率的降低,两相区变形时出现α相球化特征,单相区变形时出现β相动态回复及动态再结晶的特征。而在高应变速率下,该合金出现局部塑性流动的失稳特征,并形成变形带。
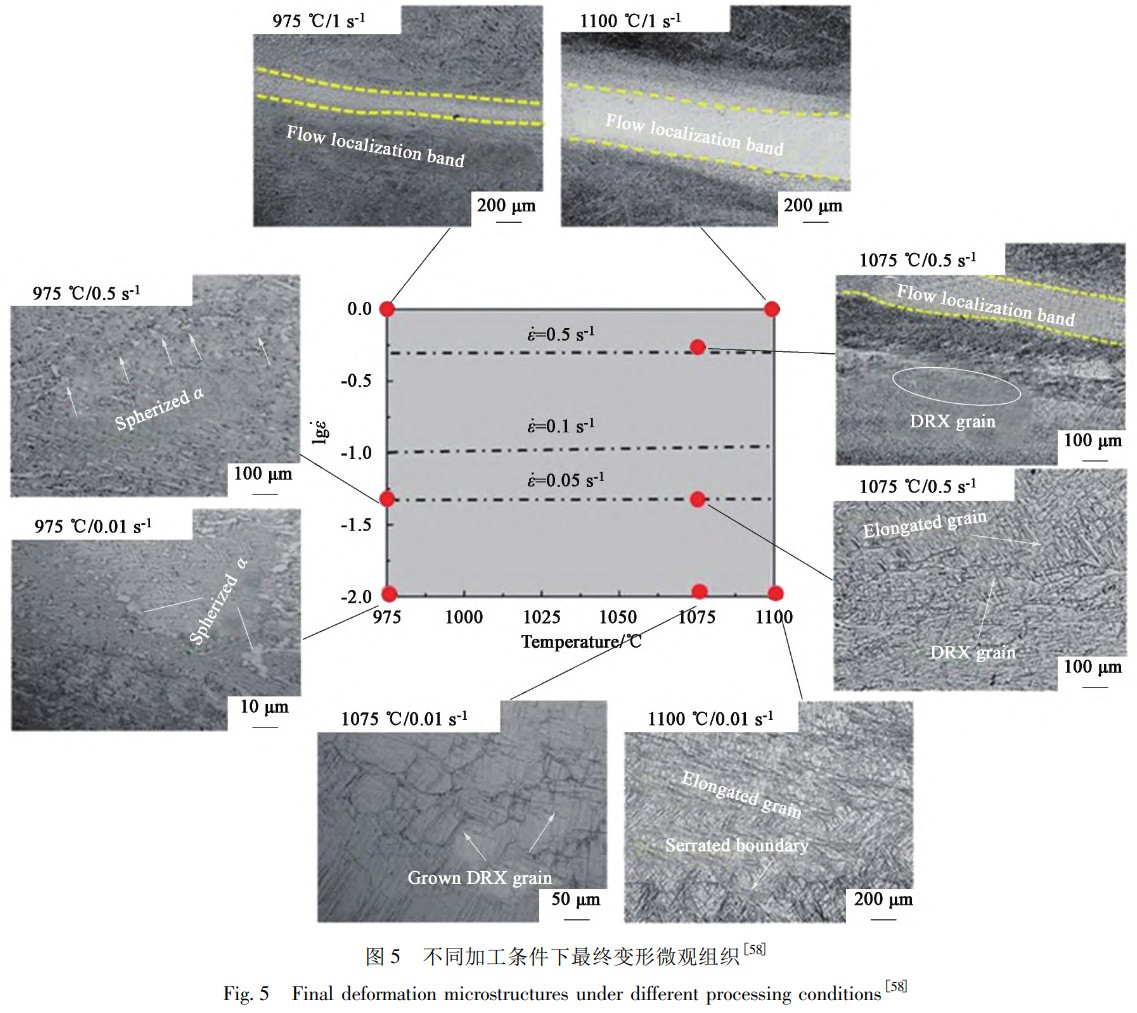
此外,SUY等[58]还发现经多道次热锻法(锻造温度1080℃,应变速率0.05~0.1s-1)获得的具备网篮组织的DsTi700钛合金室温性能明显高于初始铸态网篮组织,尤其是在650℃时的力学性能,该合金抗拉强度超过600MPa,该值十分接近传统近α型钛合金在600℃的抗拉强度。综合分析等温锻造及非等温锻造实验结果可知,钛合金在实际模锻成形时,应变速率不宜选择过高,但也不能太低,需根据实际生产情况进行适当调整。
2.3变形量
变形量也是钛合金锻造过程中的一个重要参量。变形量的改变会影响晶粒度大小,增加变形量可以使晶内组织得到有效细化。据报道,随变形温度的升高,变形量的影响逐渐降低,且变形量对性能(尤其是塑性)影响最明显的区域位于β转变温度以下,由于该状态下α相一直存在,而α相也会发生塑性变形。α相是密排六方结构,为硬相,在高温变形过程中会钉扎位错,增加变形量可以促进钛合金发生动态再结晶[59]。在钛合金工件的生产过程中,两相区上部的热加工是将片状组织结构分解为精细且均匀组织的关键步骤,该工艺在确定最终微观组织和性能中起关键作用。若初始组织为片状组织,增加变形量可以促进片成α相发生动态球化,而动态球化是典型的钛合金动态再结晶现象,是一种几何再结晶,高层错能的钛合金更容易发生动态球化[60]。GAOPF等[61]研究了钛合金两相区上部热加工过程中片状组织演变及流动行为机制,结果表明片状α相的演化与相对于压缩轴的几何取向有关。若片状α相的轨迹与压缩方向平行,则它倾向于扭结;否则片状α相随变形量的增加向较软的方向旋转,并逐渐重新排列其轨迹,使其垂直于压缩方向。与此同时,片状α相发生动态球化,其具体过程为高能缺陷的形成、高能缺陷引起片层失稳及分裂片层结构。
钛合金中等轴状初生α相在热变形过程中也会发生一系列组织演变,如亚结构的形成、再结晶等。
WUC等[62-63]研究发现,TA15钛合金在两相区等温变形过程中亚结构演变对其流动行为具有重要影响,亚结构所占体积分数与变形量呈正比,如图6所示,当变形量由30%增加至70%时,试验测得大角度晶界占比由48%变大至72%,而CA模型预测结果是由44.7%至68.4%;热变形过程中,小角度晶界形成的新亚晶粒与小角度晶界变为的大角度晶界所消耗的亚晶粒间呈竞争关系。变形过程中因位错的涅灭与重排,先形成位错胞进而转变为亚晶粒,且随着变形量的增加,更多的位错聚集在亚晶粒晶界的周围,增加了小角度晶界向大角度晶界转变的驱动力。
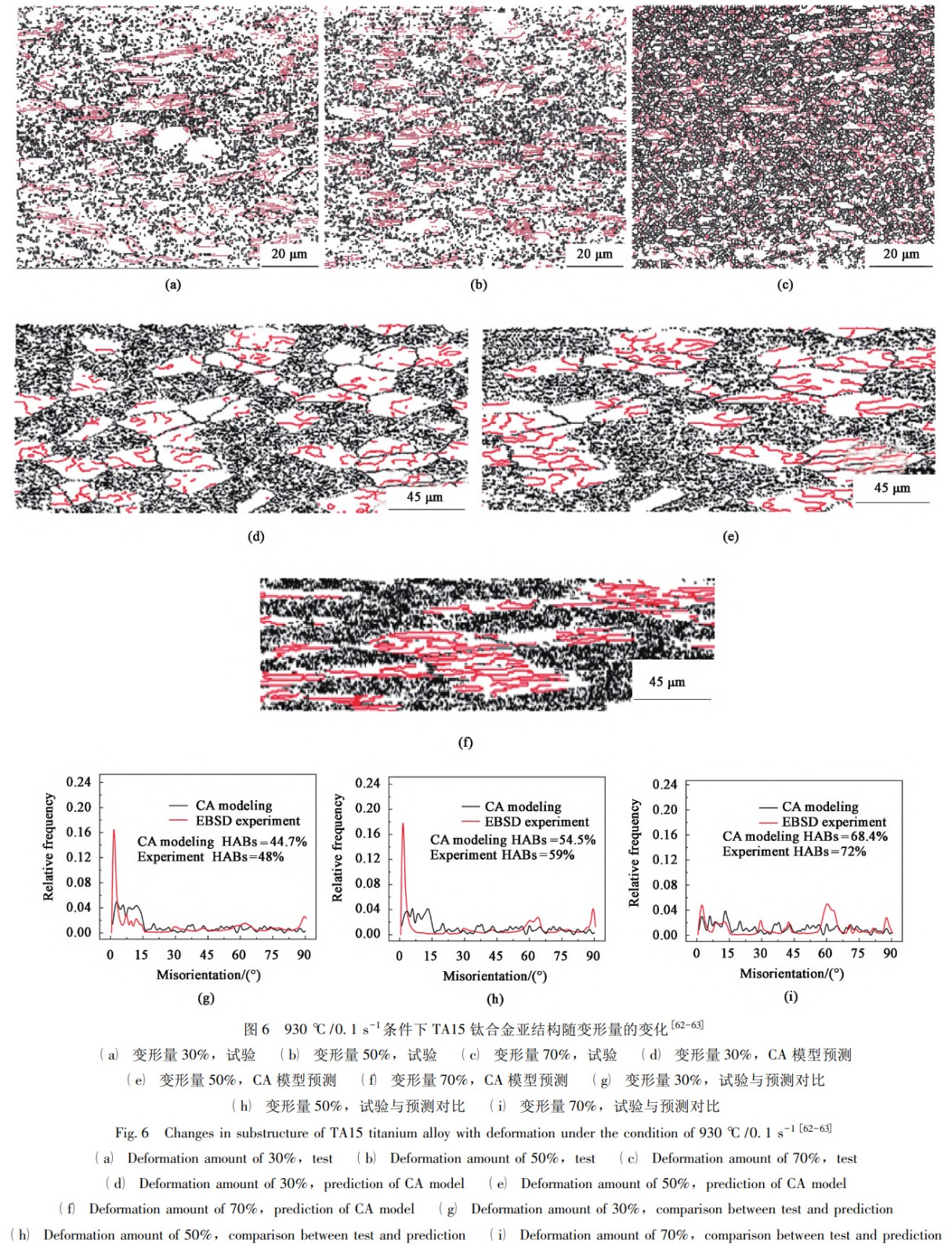
钛合金在两相区热变形过程中,除α相发生一系列变化外,β相也会发生动态回复、动态再结晶等组织演变,且比单相区更容易发生动态再结晶等组织演变机制[59,64]。同时,β晶粒再结晶百分数随着变形量的增加而逐渐增大。针对初始状态不同的钛合金,其在锻造时所选择的变形量也存在一定差异,一般情况下,组织发生明显细化是变形量需超过30%甚至40%,而针对片层组织,通常超过60%的变形量才能充分球化。当然,钛合金实际生产中热加工时变形量的选择并不是越大越好,有报道表明,当变形量超过85%时,某些钛合金会出现晶粒粗化的现象,这是由于变形程度过高,位相接近或一致的晶粒会相互合并长大。故在选择变形量时,首先要考虑锻件的质量要求,然后考虑坯料的组织形态、锻件的尺寸及形态等,最后选择合适的变形量。
3、锻造过程中微观组织演变
钛合金锻件的微观组织与锻造时所采用的工艺参数紧密相关。钛合金部件从铸锭开坯到成形,过程中的晶粒尺寸、相组成及织构分布均会发生显著变化[14]。此外,针对一些较大型的钛合金锻件,不同部位的应变状态、摩擦因数及冷却速度等均有所差异,这会造成钛合金锻件各个部位组织出现一定的不均匀性。故掌握钛合金在热加工过程中微观组织演变规律对设计并优化钛合金成形工艺具有重要作用。
3.1晶粒尺寸演变规律
钛合金构件性能受其微观组织形态及尺寸的控制,不同应用场合所需钛合金构件性能不同。为了方便研究微观组织对性能的影响,常对组织的各种参数进行量化处理。钛合金微观组织中晶粒大小与变形工艺参数息息相关,一般情况下,微观组织中晶粒细匀化越强,钛合金部件性能越好。而晶粒细化是钛合金加工过程中显微组织变化最明显的特征。
ZHANGZX等[65]提出了钛合金在等温锻造过程中的晶粒细化机制,并认为动态再结晶是造成钛合金晶粒细化的主要机制。如前所述,钛合金在两相区热加工过程中片状α相动态球化的过程是一种连续再结晶,热成形过程中引入的高密度位错逐渐演变成亚晶界及大角度晶界的过程属于连续再结晶。而不连续动态再结晶一般发生在较高的应变速率下,其主要特征是变形过程中原始晶界受位错的影响出现明显的锯齿状现象。对于层错能较低的γ-TiAl基合金,其主要变形机制为孪生,且随着变形量的增加,会出现多重变形孪晶,孪晶之间相互作用,出现孪生切割现象,进而产生大量孪晶界,这些新界面是动态再结晶的形核点。γ-TiAl合金在多向锻造和等温压缩过程发生α2/γ相片层转变为γ和β相的现象,且在γ相中发生连续动态再结晶和不连续动态再结晶,而在β相中以动态回复为主[66]。
纪小虎等[67]研究了TA15钛合金在多向等温锻造过程中的组织演变规律,如图7所示,经过第1道次变形后,部分长条的初生α相发生破碎,且初始片状α相被拉伸或扭曲,如图7a和图7b所示。
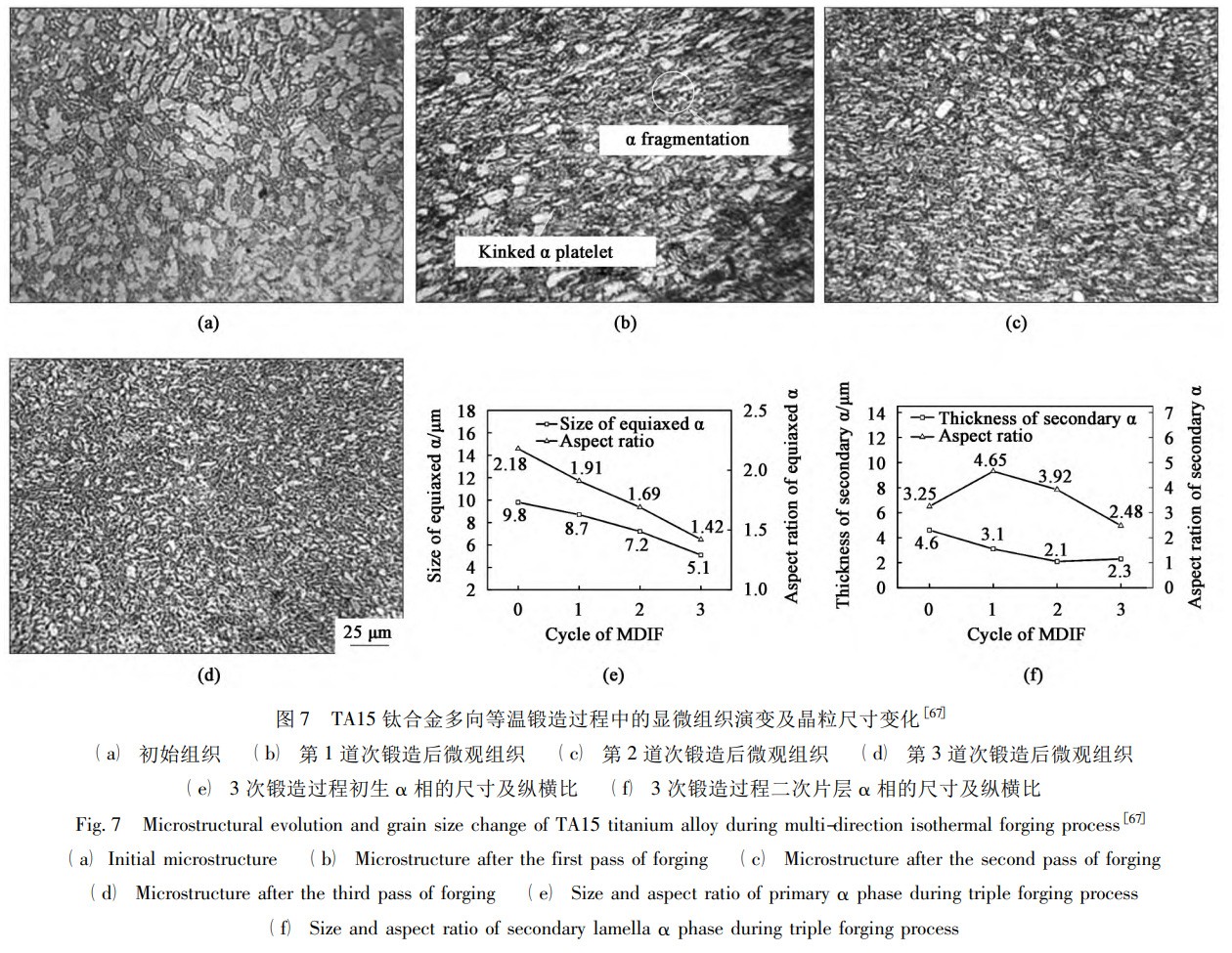
与第1道次变形后相比,第2道次变形后原始初生α相及片层α相仍有少量剩余,如图7c所示。在第3道次变形后,初生α相充分破碎,同时片状α相也明显碎化,如图7d所示。图7e和图7f显示了初生α相和片成α相晶粒尺寸及轴比的变化。由图7e可知,初生α相晶粒尺寸及轴比与变形道次呈反比,即其值随变形道次的增加而减小,且初生α相尺寸由最初的约9.8μm被细化至约5.1μm;而轴比由约2.18减小到约1.42,该现象表明多向锻造会使钛合金晶粒细化且提高其均匀性。片状α相厚度与变形道次接近呈反比,与初生α相晶粒尺寸变化不同的是片状α相厚度随变形道次的增加呈先减小后趋于稳定。多向等温锻造过程中,片状α相轴比却随变形道次的增加表现出先增加后降低的趋势。
3.2相组分演变规律
钛合金构件的相组分与初始组织形态、锻造工艺参数、锻后冷却方式以及锻后退火工艺参数等均紧密相关[68]。相变是钛合金相组分发生变化的重要原因,且其对变形前保温时间、变形温度、应变速率、变形量及冷却速度等均参数均敏感。钛合金在锻前升温及保温过程中会发生αβ相变、变形过程会发生αβ动态相变及冷却过程中会发生βα相变,每种相变形式均会造成相组分的变化,进而使钛合金锻件性能发生变化。
张启飞等[69]研究了TA15钛合金模锻件成形过程中的宏微观组织变化规律,结果表明双相区变形过程中会出现动态相变,造成α相含量降低,β相含量升高,进而促进β晶粒长大并形成低倍清晰晶。此外,他们进一步系统性地分析了动态相变对相组分的影响,并基于JMA理论建立了不同变形温度及应变速率下的相变动力学模型,进而预测了热变形过程中相组分的变化[70]。而LUOSY等[71]研究了摩擦因数m对Ti-6Al-4V钛合金涡轮叶片在热锻造过程中的相变特性,如图8所示。涡轮叶片锻前的三维模型及锻后宏观形态如图8a和图8b所示,其中,叶片毛坯长1220mm,锻造温度为950℃。图8c和图8d分别为叶片锻件中P1及P2处的微观组织,由图可知,锻件微观组织是由剩余初生α相及β转变组织构成,且P2处的初生α相含量明显高于P1处的。他们认为造成不同部位相组分差异的原因是不同部位所对应的摩擦因数不同,且采用有限元进一步系统性研究了不同摩擦因数对相组分变化规律的影响,结果表明,初生α相含量对摩擦因数敏感,且其值均分布0%~27.2%。同时,初生α相含量最高区域均分布在锻件心部而最低区域分布在飞边周围,且随摩擦因数的变大,初生α相含量最高区域逐渐减小,如图8e所示。
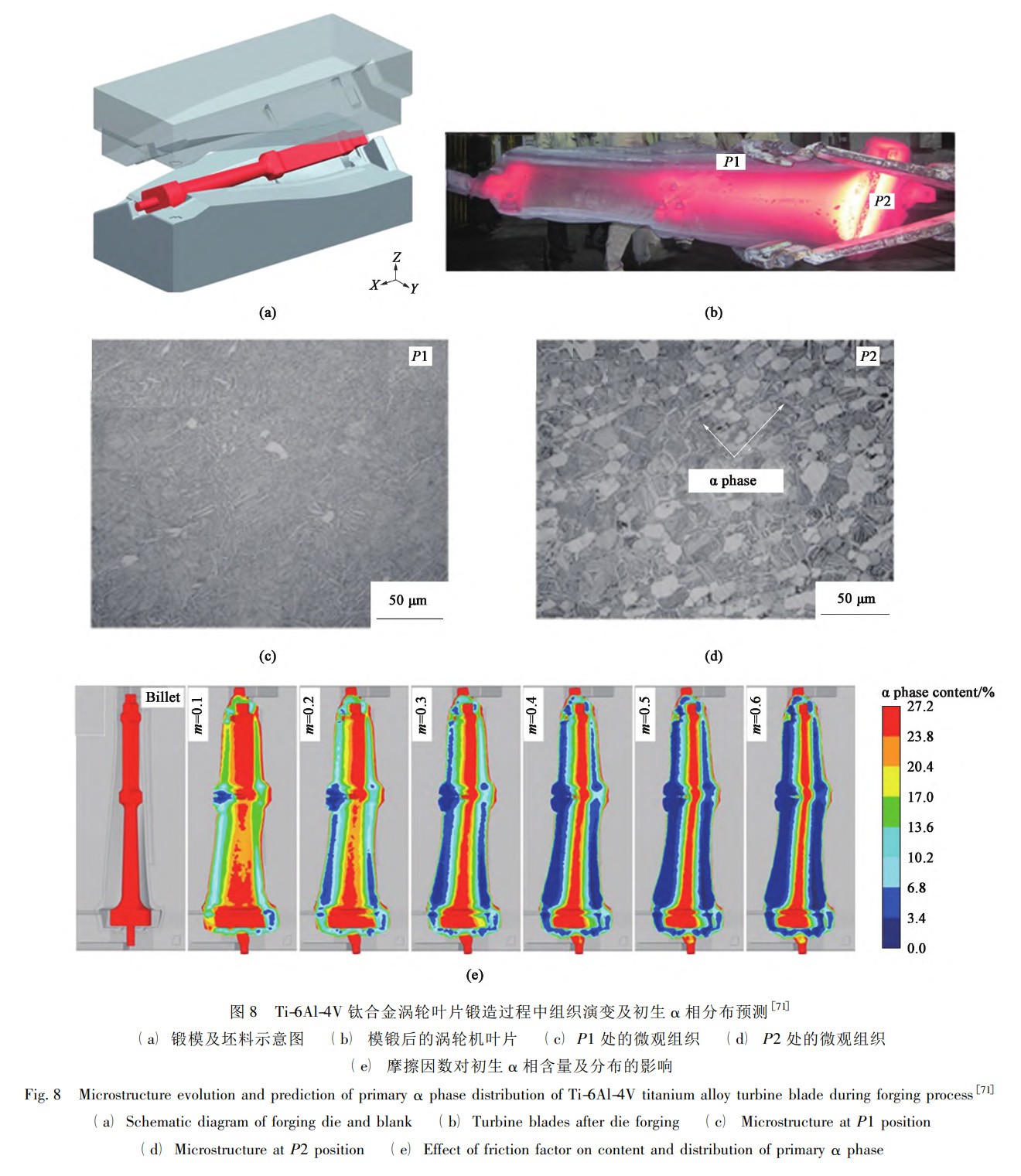
3.3织构演变规律
钛合金的性能和微观组织与织构密切相关,而织构会受到不同变形模式的影响。钛合金在锻造过程会导致应变分布不均匀,进而造成钛合金锻件微观组织和织构的复杂演变,尤其是初生α相、次生α相及β
晶粒等演变,对钛合金锻件性能产生极大影响[36,72-73]。TANGB等[36]采用XRD及EBSD研究了Ti-6Al-4V钛合金多道次锻造过过程中应变分布对织构演变的影响,结果表明应变分布初生α相的形貌及含量有显著影响,且随锻造道次的增加,初生α相含量显著增加,而织构强度逐渐降低。MENGL等[73]研究了Ti-6246钛合金在β锻造及跨相区锻造过程中α和β织构的影响规律,结果表明β晶粒在锻造过程中会形成典型的{001}和{111}织构,且因动态再结晶的作用,{001}织构强度随变形量的增加而显著增强。而在跨相区锻造过程中,随着α相的析出,β晶粒{001}织构强度随变形量的增加而降低,且没有发生动态再结晶。此外,新析出的α相表现出强烈的的{11-20}相变织构,同时α相以{10-10}<11-20>锥滑移系为主,并与{110}<111>β滑移系平行。α相的析出增加了α相和β相间的滑移传递,提高了β相的{110}<111>滑移活性,降低了α相析出后{001}β织构强度,进而提高了材料的性能。图9是锻造温度及变形量对Ti-6246钛合金α相织构强度的影响。由图可知,所有锻造条件下均出现较强的{11-20}织构,且其强度随着锻造比的增大而增强。此外,在920和950℃下,该合金锻造时出现较弱的{2-1-12}织构。
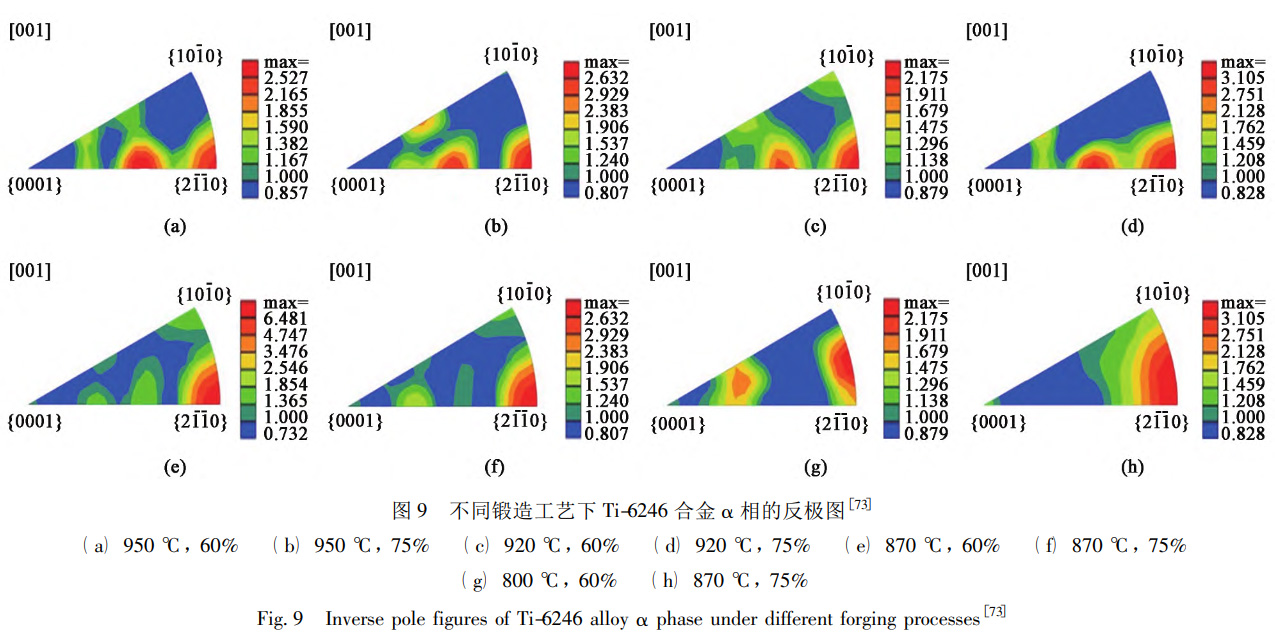
4、锻造过程对钛合金力学性能的影响
钛合金锻件的质量主要由锻造工艺决定,而锻造工艺决定钛合金微观组织结构,微观组织结构控制钛合金力学性能,且每种结构均有所对应的性能优势和劣势[46,68]。随航空航天工业的迅速发展,对现代航空飞行材料的综合服役条件要求越来越高,尤其是对性能的要求更加苛刻。目前,可通过新型号研发及工艺创新等手段获得组织最佳化的钛合金,从而获得最优的综合力学性能。
本节以单轴拉伸性能及周期载荷下的疲劳性能为例进行分析。
4.1单轴拉伸性能
单向拉伸实验是表征材料力学行为最基本的实验方法,拉伸实验所获得的抗拉强度、屈服强度及伸长率等是材料力学性能的基本指标。一般情况下,钛合金魏氏组织的室温强度最高,网篮组织次之,双态组织较低,等轴组织最低;而室温塑性呈相反的规律。研究表明,钛合金室温拉伸时除等轴组织的断裂机制为韧性断裂外,其余3种类型微观组织结构均为(准)解离断裂机制,其中双态组织的综合性能最佳[46]。SUNZ等[74]采用6种不同锻造工艺(图10)研究了局部加载条件下TA15钛合金锻件组织及性能的影响,结果表明,工件2区域A的室温强度明显高于区域B,见表1(Rm为抗拉强度,Rp0.2为屈服强度,Z为断面收缩率,A为断裂伸长率),这是由于区域B在锻造过程中形成β粗晶,造成性能下降;而工件1的力学性能优于工件2,这是由于TA15钛合金在α+β锻造初生α相含量较高;同时,通过对比工件3和工件4、工件5和工件6还发现锻后水冷的力学性能明显比空冷的情况下好,其中工件6是所有锻造工艺中室温性能最好的一组,且工件6上区域A、区域B和区域C的抗拉应力分为1053、1033和1040MPa,屈服应力分为990、950和968MPa。这是由于该组工件采用近β锻造,初生α相含量控制在约20%,其中细小的次生α相可以有效地阻碍位错运动。同时,他们还表明不同锻造工艺下室温冲击性能差异不大,且工件2及5的断裂韧性较好,工件6处于中等水准,这与微观组织中次生α相的含量及形貌有关。此外,他们还研究了TA15钛合金500℃下的力学性能,见表2,其中,工件6的高温强度最好,工件5的屈服最低,这是由于空冷过程中形成大量的成簇的次生α相,拉伸时较早地出现显著的滑移带,导致裂纹提前形成并扩展,进而造成该材料屈服降低。
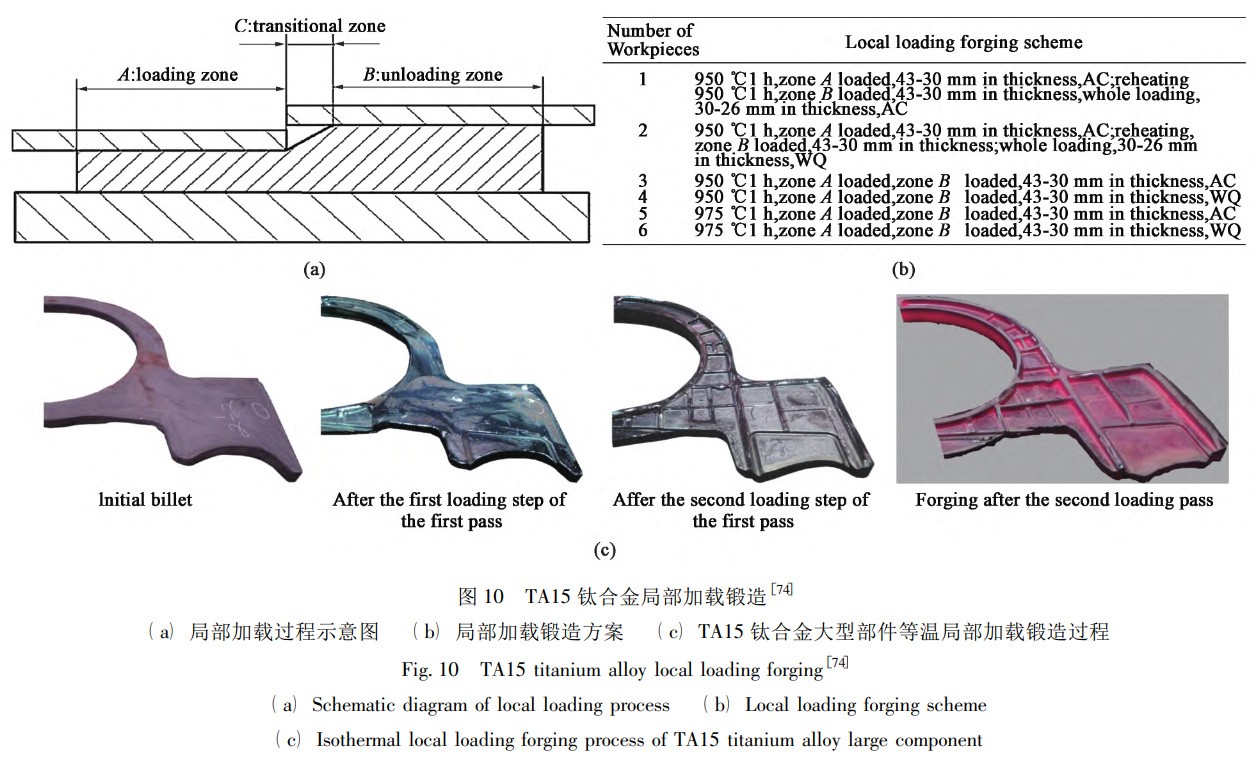
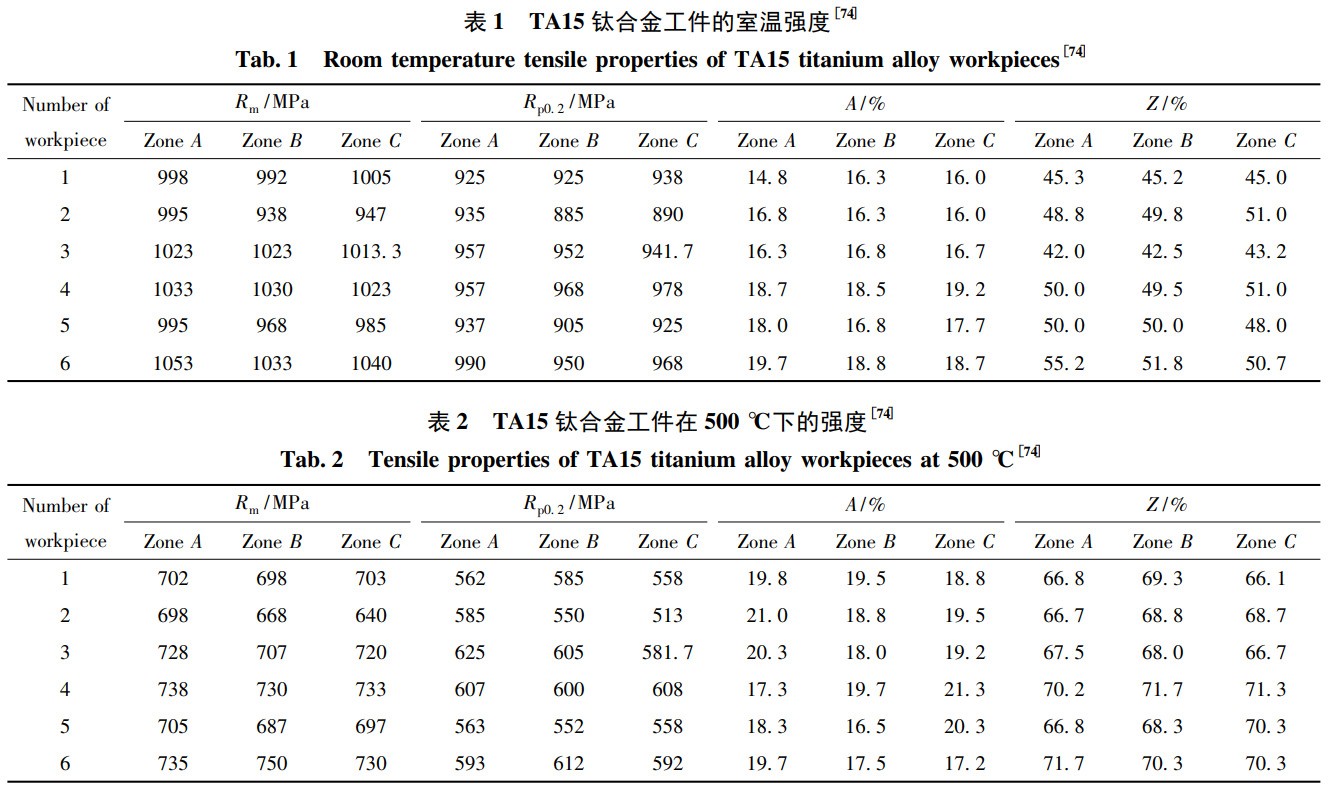
胡轶嵩等[75]系统地研究了β锻造工艺参数对TC17钛合金力学性能的影响,如图11所示(KIC为断裂韧性)。研究结果表明,室温和高温强度及塑性随锻造温度的升高而降低,如图11a和图11b所示,这是由于该合金在β锻造时,β晶粒显著长大且后续次生α相片层厚度较粗,进而造成强度和塑性随变形温度的升高均呈降低的趋势。此外,该合金随着锻造温度的升高,断裂韧性逐渐增大,如图11c所示,这是由于裂纹形核抗力随β晶粒尺寸变大而变大,且裂纹沿变厚的不同晶体取向的次生α相集束扩展并倾斜,进而造成裂纹前沿发生钝化现象,最终能够储存额外的裂纹扩展能。他们还发现TC17钛合金经β锻造后室温和高温强度及塑性随变形量的增加而变大,断裂韧性则与之相反,如图11d~图11f所示,造成这种想象的原因是加大变形量可以使原始β晶粒及晶界α相破碎,从而增加α相形核率,使滑移距离更小,降低晶界处的位错塞积应力,进而使空洞形核及扩展速度被降低,变形程度增大有利于破碎原始β晶粒和晶界α相,而且初生α相形核率增加,可获得均匀的网篮组织,滑移间距小,晶界处位错塞积应力小,延缓了空洞的形核和扩展。
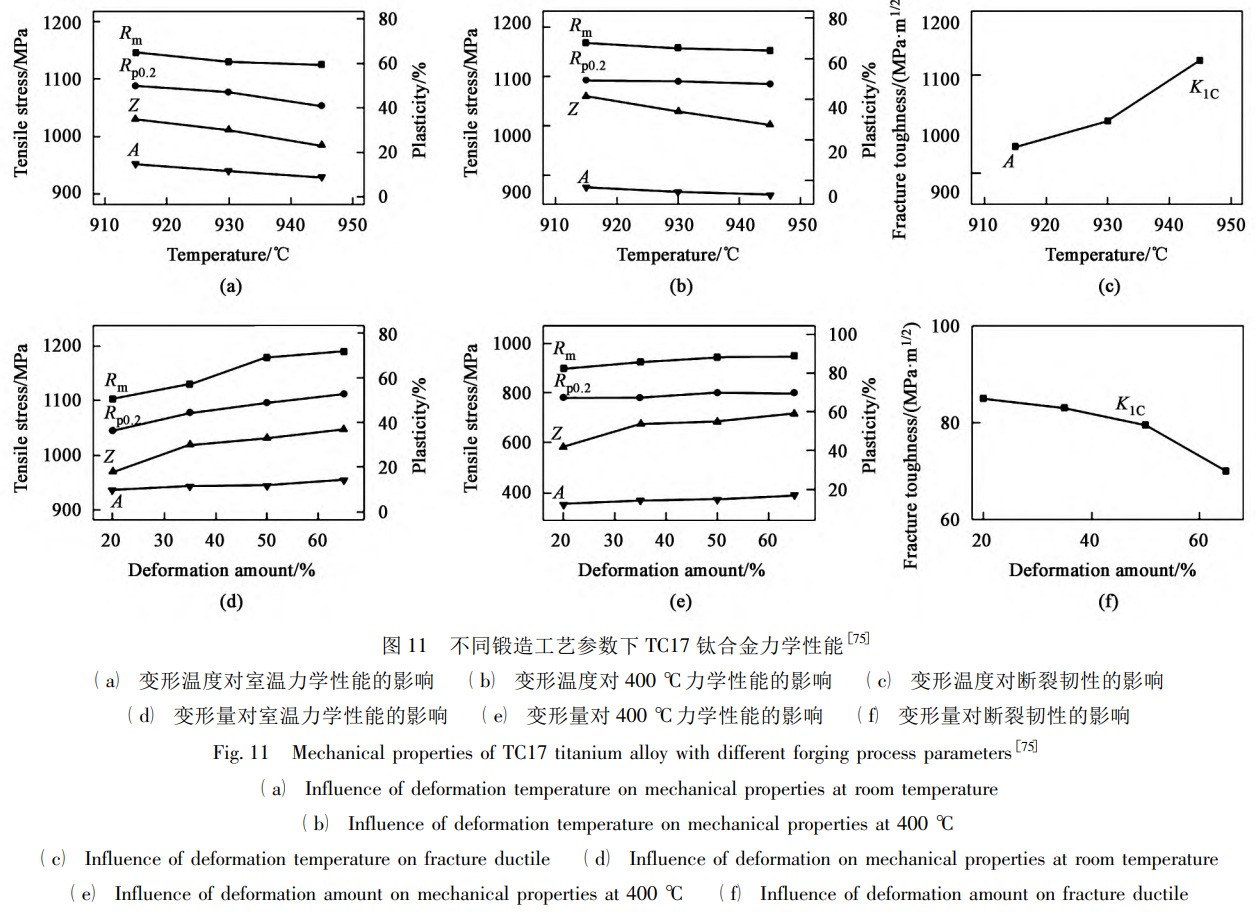
不同类型的钛合金适用场合也不同,每种场合所要求的组织形态亦存在差异。不管是变形工艺参数、还是变形后热处理工艺参数的选取都会影响钛合金服役时的力学性能,参数的合理选择是获得所需性能、组织的前提。在确定钛合金所需的组织状态后,力求通过调整变形或变形后热处理工艺参数获得强度、塑性或韧性匹配最佳的力学性能。
4.2疲劳性能
疲劳指的是合金材料在交变载荷的作用下,由累计损伤引起的失效断裂。其特点是材料承受的应力小于屈服强度,属于低应力脆性断裂,也存在裂纹的形成及扩展,且疲劳破坏是一个长期的累计过程。据统计,疲劳,特别是高周疲劳是钛合金航空发动机叶片失效的最主要方式[76],因发动机叶片承受高频振动及其本身结构特性决定,容易发生微动损伤,进而大幅度降低疲劳性能,存在巨大的安全隐患[77]。故探索材料疲劳性能与变形机制间关系具有重要意义。
目前,疲劳性能已被当作结构部件或其他部件的关键强度之一,且受到的关注越来越多。研究表明,钛合金疲劳性能对微观组织十分敏感,即α相含量及尺寸、组织类型及其特征参数等因素均会对疲劳裂纹扩展速率产生巨大影响。疲劳强度与α相尺寸及片层厚度呈反比,即较粗大的晶粒尺寸利于抑制疲劳裂纹萌生,且片层组织有助于降低裂纹扩展速率[78-79]。此外,有学者发现具备等轴或双态组织的钛合金高周疲劳性能优于网篮或片层组织,即含有初生α相的钛合金高周疲劳性能比片层组织更好[80]。张赛飞等[81]研究了近β锻TC17钛合金的高周疲劳特性,并总结了几种不同钛合金的力学性能及疲劳性能,如表3所示。
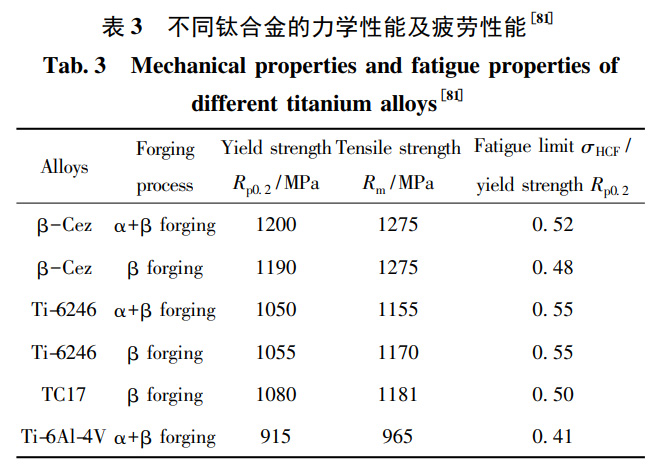
研究结果表明,具备网篮组织的TC17钛合金具有较高的疲劳强度,能满足整体发动机叶片对高周疲劳性能的要求。
ZHANGSF等[82]通过控制BT25钛合金(Ti6.5Al-2.2Mo-2.2Zr-1.8Sn-0.7W-0.2Si)等温锻造及热处理工艺,获得了3种不同的微观组织形态,研究了微观组织对高周疲劳特性的影响,如图12所示(S为最大疲劳应力,N为疲劳循环次数)。其中,BT25钛合金在α+β两相区(979℃)等温锻造且964℃固溶2h+550℃时效5h能获得初生α相含量约65.5%的等轴组织(图12a)。经979℃等温锻造且994℃/2h+550℃/5h处理后得到初生α相含量约33.2%、片层厚度约1.21μm的双态组织(图12b)。单相区等温锻后固溶时效处理可以获得全片层组织,片层厚度约2.05μm(图12c)。研究结果表明,双态组织的抗拉及屈服强度最高,等轴组织次之,片层组织最低(图12g)。断裂韧性的大小与初生α相及片层α相有关,全片层断裂韧性最大,等轴组织的最小,如图12h所示。而疲劳性能与前述研究类似,等轴及双态组织比片层组织具有更高的高周疲劳强度(图12i)。与微观组织相关的有效滑移长度和晶体的固有强度共同控制着BT25钛合金的疲劳裂纹萌生,而疲劳裂纹的萌生对微观组织的依赖性是高周疲劳性能具有微观组织敏感性的原因,3种微观组织的疲劳裂纹(图12d~图12f)形成区域均处于约30~300mm处的亚表层区域。
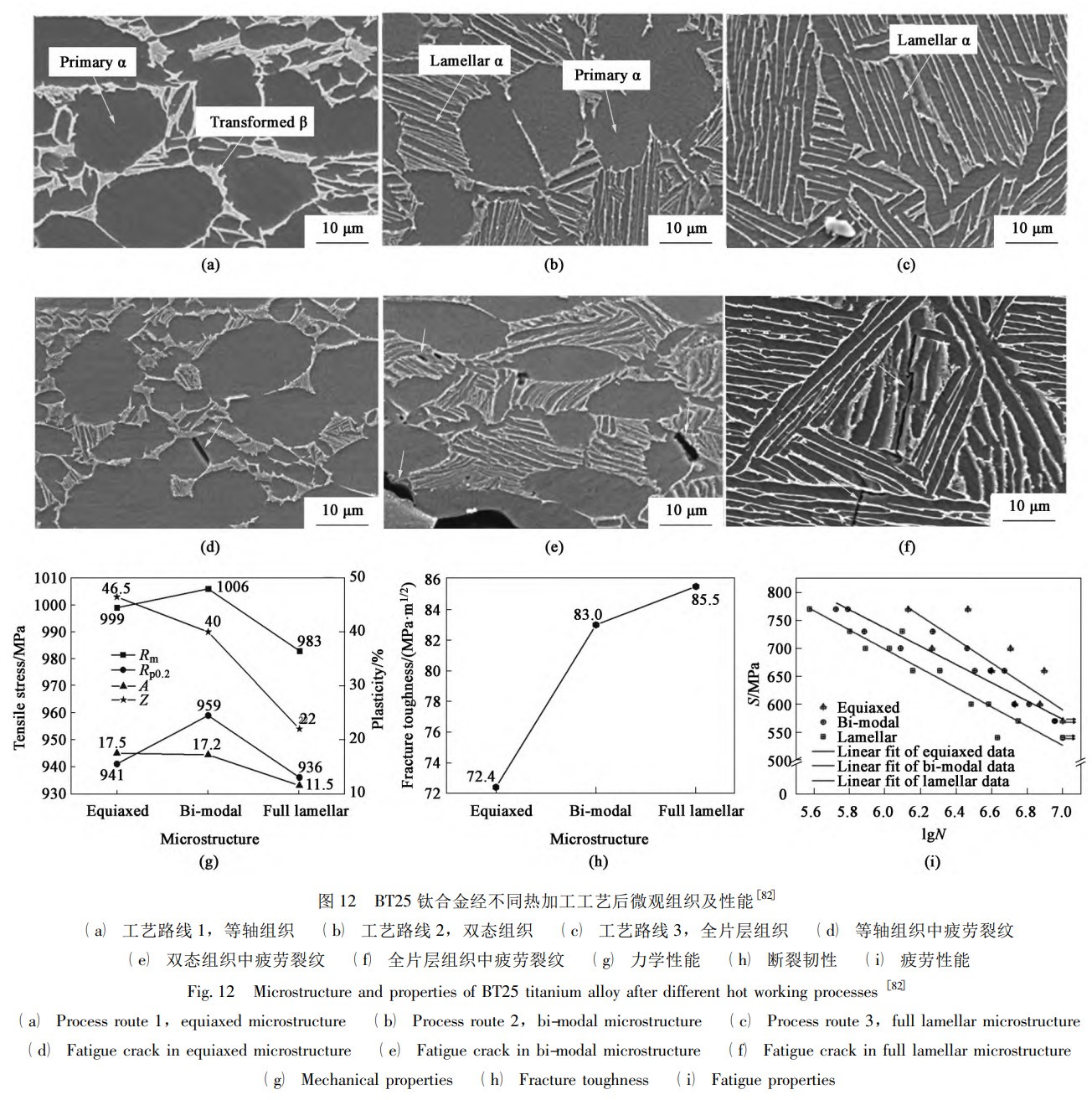
应力比也是造成钛合金疲劳性能改变的另一主要因素。由于钛合金构件在实际应用中承受的载荷形式比较复杂,因此,研究不同应力比下钛合金疲劳性能显得极其必要[83-85]。一般情况下,材料疲劳行为研究的应力比均在R=-1.0的情况下,随后利用Gerber或Goodman关系获得其他应力比下的疲劳强度。文献[85]的研究表明,Ti-6Al-4V钛合金的高周和超高周行为均存在两种疲劳裂纹萌生机制,即解理机制和滑移机制,且两种机制存在竞争关系。且随应力比的增加,疲劳裂纹萌生由滑移机制变为解理机制。
5、总结和展望
航空航天等领域的快速发展对钛合金的服役性能提出了更高的要求,锻造工艺在提高钛合金的机械性能上已取得巨大的进展。与非等温锻造和单向等温锻造相比,多向等温锻造工艺具有显著的优势,其能够同时提高材料的强度和延展性,适合获得超细晶大型锻件的工业化应用。钛合金的锻造工艺参数,尤其是锻造温度、变形量及应变速率对锻件的晶粒尺寸、相组分及织构等微观组织特征有决定性影响。在确定锻造工艺参数时,锻造工艺参数的选择不仅需要考虑合金材料及实际生产条件,还需兼顾材料性能、成本及生产效率。钛合金锻造工艺参数决定其锻件微观组织结构,而微观组织结构对力学性能和服役行为具有极大的影响。未来钛合金锻造工艺的开发与优化,可以从如下几个方面深入研究:
(1)需进一步提高锻造设备的水平,研究更合理且完善的工艺路线,探索适用性更强且后处理或合金化方式,为减少甚至消除钛合金在整个热加工工艺流程中出现的问题提供新思路。
(2)钛合金近β锻造和跨相区锻造可获得组织均匀性好且综合性能优异的锻件,这些锻造方法具有极大的应用前景。进一步扩宽多种类型钛合金的新型锻造工艺,为研发并制备组织且性能更优的钛合金提供实际指导和宝贵经验。
(3)钛合金锻件的组织是否均匀和性能高低主要是钛合金锻造过程中温度场、应变场及金属流动场等多物理场域相互耦合作用的结果。需建立合适的钛合金锻造成形的有限元仿真模型,开发可准确预测钛合金锻造过程的仿真算法及软件,进而实现钛合金锻造过程的工艺参数设计及优化。
(4)钛合金在锻造过程中微观组织演变规律十分复杂,仍需继续深入探究多相组织在热加工过程中的位错、晶体结构等演变对组织及性能影响规律,建立可表征锻造工艺参数和微观组织特征的物理基模型。
(5)钛合金作为综合性能优异的轻质结构材料,研究其在航空领域的服役过程中的力学性能及疲劳性能是开发并扩展高性能航空钛合金构件及其应用的关键课题。关于钛合金构件服役过程中的失效机制仍需进一步探索,其中,疲劳裂纹的萌生及扩展的深层机理尚不清晰,高温蠕变的深层机制同样有待深究等。
参考文献:
[1] BANERJEE D,WILLIAMS J C. Perspectives on titanium science and technology [J]. Acta. Mater.,2013,61 ( 3) : 844-879.
[2] FANG Z Z,FROES F H,ZHANG Y,et al. Extractive metallurgy of titanium: Introduction to the development of processes for primary Ti metal production [M]. Amsterdam: Elsevier,2020.
[3] WILLIAMS J C,BOYER R R. Opportunities and issues in the application of titanium alloys for aerospace components [J]. Metals,2020,10 ( 6) ,705,1-22.
[4] 王亚辉,黄亮,刘翔,等. 基于增材制造和锻造复合成形的TC4 钛合金组织和性能研究 [J]. 稀有金属,2021,45 ( 8) :897-904.
WANG Yahui,HUANG Liang,LIU Xiang,et al. Microstructure and mechanical properties of TC4 alloy formed by additive manufacturing combined with forging[J]. Chin. J. Rare Metals. ,2021,45 ( 8) : 897-904.
[5] 韩鹏,李伯龙,尹嘉明,等. Er 对一种近 α 型高温钛合金蠕 变性能的影响 [J]. 科学技术工程,2012,12 ( 17) : 4124 - 4127.
HAN Peng,LI Bolong,YIN Jiaming,et al. Effect of Er on creep properties of a near-α high temperature titanium alloy [J]. Sci. Technol. Eng.,2012,12 ( 17) : 4124-4127.
[6] ZHAO E T,SUN S C,ZHANG Y. Recent advances in silicon containing high temperature titanium alloys[J]. J. Mater. Res. Technol.,2021,14:3029-3042.
[7] GEY N,BOCHER P,UTA E,et al. Texture and microtexture variations in a near-α titanium forged disk of bimodal microstructure[J]. Acta. Mater.,2012,60: 2647-2655.
[8] MORITA A,HATTORI S,TANI K,et al. Near net shape forging of titanium alloy turbine blade[J]. ISIJ Int.,1991,31 ( 8) : 827 -833.
[9] XIAO G J,HUANG Y,YIN J C. An integrated polishing method for compressor blade surfaces [J]. Int. J. Adv. Manuf. Technol.,2017,88: 1723-1733.
[10] ROMERO J,ATTALLAH M M,PREUSS M,et al. Effect of the forging pressure on the microstructure and residual stress development in Ti-6Al-4V linear friction welds[J]. Acta. Mater.,2009,57 ( 18) : 5582-5592.
[11] WILLIAMS J. Thermo-mechanical processing of high-performance Ti alloys: Recent progress and future needs[J]. J. Mater. Process. Tech.,2001,117 ( 3) : 370-373.
[12] 蔡旺,杨合,李从心. 热力耦合作用下叶片锻造晶粒尺寸的预 测 [J]. 锻压技术,2004,29 ( 6) : 67-69.
CAI Wang,YANG He,LI Congxin. Prediction of grain size in the forging process of blade under the action of coupled thermo-mechanical forming [J]. Forging & Stamping Technology,2004,29( 6) : 67-69.
[13] 王涛,郭鸿镇,张永强,等. 热锻温度对 TG6 高温钛合金显微 组织和力学性能的影响 [J]. 金属学报,2010,46 ( 8) : 913- 920.
WANG Tao,GUO Hongzhen,ZHANG Yongqiang,et al. Effect of hot forging temperature on microstructure and mechanical property of TG6 high temperature titanium alloy [J]. Acta. Metall. Sin.,2010,46 ( 8) : 913-920.
[14] 马济民,贺金宇,庞克昌,等. 钛铸锭和锻造 [M]. 北京: 冶 金工业出版社,2012. MA Jimin,HE Jinyu,PANG Kechang,et al. Titanium ingots and forgings [M]. Beijing: Metallurgical Industry Press,2012.
[15] KIM J Y,PARK K T,SHIM I O,et al. Globularization behavior of ELI grade Ti-6Al-4V alloy during non-isothermal multi-step forging[J]. Mater. Trans.,2008,49 ( 1) : 215-223.
[16] FAN X G,YANG H,GAO P F. Through-process macro-micro finite element modeling of local loading forming of large-scale complex titanium alloy component for microstructure prediction [J]. J. Mater. Process Technol.,2014,214: 253-266.
[17] WANG K X,ZENG W D,ZHAO Y Q,et al. Prediction of dynamic globularization of Ti-17 titanium alloy with initial lamellar microstructure during hot compression [J]. Mater. Sci. Eng.,2010,A527: 6193-6199.
[18] WU C,HUANG L. Hot deformation and dynamic recrystallization of a near-beta titanium alloy in the β single phase region[J]. Vacuum,2018,156:384-401.
[19] ZHU H J,CHEN F,ZHANG H M,et al. Review on modeling and simulation of microstructure evolution during dynamic recrystallization using cellular automaton method [J]. Sci. China Technol. Sci.,2020,63 ( 3) : 357-396.
[20] 方秀荣,邵艳茹,陆佳,等. 锻造工艺参数对 TC4 钛合金锻件 残余应力的影响 [J]. 锻压技术,2021,46 ( 3) : 1-8.
FANG Xiurong,SHAO Yanru,LU Jia,et al. Influence of forging process parameters on residual stress of TC4 titanium alloy forgings[J]. Forging & Stamping Technology,2021,46 ( 3) : 1-8.
[21] NONG Z S,LEI Y N,ZHU J C. Effect of α phase on evolution of oxygen-rich layer on titanium alloys [J]. Trans. Nonferrous Met. Soc. China,2019,29: 534-545.
[22] JOSEPH S,KONTIS P,CHANG Y H,et al. A cracking oxygen story: A new view of stress corrosion cracking in titanium alloys[J]. Acta. Mater.,2022,227: 117687.
[23] JI R J,WANG H Y,WANG B K,et al. Removing loose oxide layer and producing dense α-phase layer simultaneously to improve corrosion resistance of Ti-6Al-4V titanium alloy by coupling electrical pulse and ultrasonic treatment [J]. Surf. Coat. Tech.,2020,384: 125329.
[24] 陈雷,张禹森,张启飞,等. TC18 钛合金模锻件低倍组织分 层机理 及 预 测 [J]. 中国有色金属学报,2023,33 ( 2) :343-352.
CHEN Lei,ZHANG Yusen,ZHANG Qifei,et al. Mechanism for macrostructure delamination of TC18 tianium alloy die forging and its prediction [J]. Chin. J. Nonferrous Met.,2023,33 ( 2) : 343 -352.
[25] AHMED M,SAVVAJIN D G,IVASISHIN O M,et al. The effect of cooling rates on the microstructure and mechanical properties of thermo-mechanically processed Ti-Al-Mo-V-Cr-Fe alloys [J]. Mater. Sci. Eng.,2013,A576: 167-177.
[26] TAMIZIFAR M,OMIDVAR H,SALEHI T,et al. Effect of processing parameters on shear bands in non-isothermal hot forging of Ti-6Al-4V [J]. Mater. Sci. Technol.,2002,18 ( 1) : 21-29.
[27] SALISHCHEV A,VALIAKHMETOV R,GALEYEV R M. Formation of submicrocrystalline structure in the titanium alloy VT8 and its influence on mechanical properties [J]. J. Mater. Sci.,1993,28 ( 11) : 2898-2902.
[28] 张方,王林岐,赵松. 航空钛合金锻造技术的研究进展 [J].锻压技术,2017,42 ( 6) : 1-7.
ZHANG Fang,WANG Linqi,ZHAO Song. Research development on forging technology for aviation titanium alloys [J]. Forging & Stamping Technology,2017,42 ( 6) : 1-7.
[29] WILLIAMS C,BOYER R. Opportunities and issues in the application of titanium alloys for aerospace components [J]. Metals,2020,10 ( 6) ,705: 1-22.
[30] ZHANG F Z,WANG B,CAO Q H,et al. Effect of deformation degree on microstructure and mechanical properties evolution of TiBw/Ti60 composites during isothermal forging [J]. Trans. Nonferrous Met. Soc. China,2023,33 ( 3) : 802-815.
[31] JIANG H Y,FENG C. Experimental study on isothermal forging technology for a complex-shaped titanium alloy wing [J]. Rare Metal Mat. Eng.,2017,46 ( 11) : 3182-3187.
[32] 李凯,林莺莺,陈由红,等. 等温锻造和双重退火对 TC11 钛 合金显微组织和力学性能的影响 [J]. 热加工工艺,2021,50( 11) : 35-37,44.
LI Kai,LIN Yingying,CHEN Youhong,et al. Effect of isothermal forging and duplex-annealing on microstructure and mechanical properties of TC11 titanium alloy[J]. Hot Work. Technol.,2021,50 ( 11) : 35-37,44.
[33] FANG X R,WU J,OU X,et al. Microstructural characterization and mechanical properties of Ti-6Al-4V alloy subjected to dynamic plastic deformation achieved by multipass hammer forging with different forging temperatures [J]. Adv. Mater. Sci. Eng.,2019. DOI: 10. 1155 /2019 /6410238.
[34] BAO X,CHEN W,ZHANG J,et al. Achieving high strength-ductility synergy in a hierarchical structured metastable Î2-titanium alloy using through-transus forging [J]. J. Mater. Res. Technol.,2021,11: 1622-1636.
[35] CHOUHAN D K,BISWAS S. Microstructure and texture evolution during multi-direction forging of titanium [J]. Mater. Today:Proc.,2021,44: 3102-3105.
[36] TANG B,XIANG L,YAN Z,et al. Effect of strain distribution on the evolution of α phase and texture for dual-phase titanium alloy during multi-pass forging process[J]. Mater. Chem. Phys.,2019,228: 318-324.
[37] ZHANG Z X,QU S J,FENG A H,et al. Microstructural mechanisms during multidirectional isothermal forging of as-cast Ti-6Al4V alloy with an initial lamellar microstructure [J]. J. Alloys Compd.,2019,773: 277-287.
[38] 陈玉勇,崔宁,孔凡涛. 变形 TiAl 合金研究进展 [J]. 航空材 料学报,2014,34 ( 4) : 112-118.
CHEN Yuyong,CUI Ning,KONG Fantao. Progress of deformed TiAl alloys[J]. J. Aeronaut. Mater.,2014,34 ( 4) : 112-118.
[39] HE W W,TANG H P,LIU H Y,et al. Microstructure and tensile properties of containerless near-isothermally forged TiAl alloys[J]. Trans. Nonferrous Met. Soc. China,2011,21: 2605-2609.
[40] ZHU K,QU S J,FENG A H,et al. Microstructural evolution and refinement mechanism of a beta-gamma TiAl-based alloy during multidirectional isothermal forging [J]. Materials, 2019, 12( 15) ,2496: 1-15.
[41] 张志雄,王涛,林鹏,等. 钛合金多向锻造工艺研究进展 [J].塑性工程学报,2020,27 ( 8) : 1-9.
ZHANG Zhixiong,WANG Tao,LIN Peng,et al. Recent advances on multi-directional forging of titanium alloy [J]. Journal of Plasticity Engineering,2020,27 ( 8) : 1-9.
[42] 周璇,王克鲁,鲁世强,等. 加工参数对 Ti2041 合金热变形行 为及组织演变的影响 [J]. 稀有金属,2022,46 ( 5) : 554 - 563.
ZHOU Xuan,WANG Kelu,LU Shiqiang,et al. Hot deformation behavior and microstructure evolution of Ti2041 alloy with processing parameters[J]. Chin. J. Rare Metals. ,2022,46 ( 5) : 554- 563.
[43] LI C M,HUANG L,LI C L,et al. Research progress on hot deformation behavior of high-strength β titanium alloy: Flow behavior and constitutive model [J]. Rare Met.,2022,41 ( 5) : 1434 - 1455.
[44] ZHAO Q Y,SUN Q Y,XIN S W,et al. High-strength titanium alloys for aerospace engineering applications: A review on meltingforging process[J]. Mater. Sci. Eng.,2022,A845: 143260.
[45] FANG X G,ZHANG Y,GAO P F,et al. Deformation behavior and microstructure evolution during hot working of a coarse-grained Ti-5Al-5Mo-5V-3Cr-1Zr titanium alloy in beta phase field [J]. Mater. Sci. Eng.,2017,A694: 24-32.
[46] 赵永庆,辛社伟,陈永楠,等. 中国战略性新兴产业-新材料-新型合金材料—钛合金 [M]. 北京: 中国铁道出版社,2017. ZHAO Yongqing,XIN Shewei,CHEN Yongnan,et al. China's strategic emerging industries-new materials-new alloy materials—Titanium alloys [M]. Beijing: China Railway Publishing House,2017.
[47] 朱红,廖鸿. 锻造温度对 TC11 钛合金组织和性能的影响 [J].热加工工艺,2013,( 13) : 128-130. ZHU Hong,LIAO Hong. Effect of forging temperature on the microstructure and mechanical properties of TC11 titanium alloys[J]. Hot Work. Technol.,2013,13: 128-130.
[48] JACKSON M,JONES N G,DYE D,et al. Effect of initial microstructure on plastic flow behaviour during isothermal forging of Ti10V-2Fe-3Al[J]. Mater. Sci. Eng.,2009,A501: 248-254.
[49] 田伟,伏宇,钟燕,等. 锻造工艺对 TC17 钛合金的显微组织和 力学性能的影响[J]. 材料热处理学报,2016,37 ( 9) : 57-61.
TIAN Wei,FU Yu,ZHONG Yan,et al. Transactions of materials and heat treatment [J]. Trans. Mater. Heat Treat.,2016,37( 9) : 57-61.
[50] ZHOU Y G,ZENG W D,YU H Q. An investigation of a new nearbeta forging process for titanium alloys and its application in aviation components[J]. Mater. Sci. Eng.,2005,A393 ( 1) : 204- 212.
[51] 刘瑞,郭鸿镇,张永强,等. 跨相区等温锻造对 TC18 合金组 织和性能的影响 [J]. 金属铸锻焊技术,2012,41 ( 9) : 26- 28.
LIU Rui,GUO Hongzhen,ZHANG Yongqiang,et al. Effect of cross-region forging on microstructure and mechanical properties of TC18 titanium alloy [J]. Cast. Forg. Weld.,2012,41 ( 9) : 26- 28.
[52] MA F C,LU W J,QIN J I,et al. Microstructure evolution of nearαtitanium alloys during thermomechanical processing [J]. Mater. Sci. Eng.,2006,A416: 59-65.
[53] 黄定辉,周俊,洪鑫,等. 准 β 锻造工艺对 TC18 钛合金组织 与性能的影响 [J]. 锻压技术,2014,39 ( 8) : 125-128.
HUANG Dinghui,ZHOU Jun,HONG Xin,et al. Influence of quasiβ forging on microstructure and mechanical properties of TC18 Ti alloy [J]. Forging & Stamping Technology,2014,39 ( 8) : 125- 128.
[54] SEMIATIN S L,LAHOTI G D. Deformation and unstable flow in hot forging of Ti-6Ai-2Sn-4Zr-2Mo-0. 1Si [J]. Metall. Mater. Trans.,1981,12A: 1705-1717.
[55] JUN T S,ZHANG Z,SERNICOLA G,et al. Local strain rate sensitivity of single α phase within a dual-phase Ti alloy [J]. Acta Mater.,2016,107: 298-309.
[56] LIN P,HAO Y G,ZHANG B Y,et al. Strain rate sensitivity of Ti22Al-25Nb( at%) alloy during high temperature deformation [J]. Mater. Sci. Eng.,2018,A710: 336-342.
[57] YANG X M,GUO H Z,YAO Z K,et al. Effect of isothermal forging strain rate on microstructures and mechanical properties of BT25y titanium alloy [J]. Mater. Sci. Eng.,2016,A673: 355- 361.
[58] SU Y,KONG F T,YOU F H,et al. The high-temperature deformation behavior of a novel near-α titanium alloy and hot-forging based on the processing map [J]. Vacuum,2020,173: 109135.
[59] GU B,CHEKHONIN P,XIN S W,et al. Effect of temperature and strain rate on the deformation behavior of Ti5321 during hotcompression[J]. J. Alloys Compd.,2021,876: 159938.
[60] FUJITSUNA N,OHYAMA H,MIYAMATO Y,et al. Isothermal forging of TiAl-based intermetallic compounds [J]. ISIJ Int.,1991,31 ( 10) : 1147-1153.
[61] GAO P F,FU M W,ZHAN M,et al. Deformation behavior and microstructure evolution of titanium alloys with lamellar microstructure in hot working process: A review [J]. J. Mater. Sci. Technol.,2022,39:56-73.
[62] WU C,YANG H,LI H W. Substructure and texture evolution and flow behavior of TA15 titanium alloy compressed in the alpha+beta two-phase field [J]. J. Mater. Process. Technol.,2013,213:2033-2041.
[63] WU C,YANG H,LI H W. Substructure evolution of Ti-6Al-2Zr1Mo-1V alloy isothermally hot compressed in α+β two-phase region[J]. Acta Metall. Sin.,2013,26 ( 5) : 533-544.
[64] LU T,DAN Z H,LI T J,et al. Flow softening and microstructural evolution of near β titanium alloy Ti-35421 during hot compression deformation in the α + β region [J]. J. Mater. Res. Technol.,2020,19: 2257-2274
[65] ZHANG Z X,QU S J,FENG A H,et al. Achieving grain refinement and enhanced mechanical properties in Ti-6Al-4V alloy produced by multidirectional isothermal forging[J]. Mater. Sci. Eng.,2017,A692: 127-138.
[66] 陶国强,祁 广 源,曲 寿 江,等. 多 向 等 温 锻 造 Ti-44Al-4Nb1. 5Cr-0. 5Mo-0. 1B-0. 1Y 合金高温压缩变形行为研究 [J]. 钛 工业进展,2018,35 ( 3) : 11-15.
TAO Guoqiang,QI Guangyuan,QU Shoujiang,et al. Study on high temperature compressive deformation behavior of multi-directional isothermally forged Ti-44Al-4Nb-1. 5Cr-0. 5Mo-0. 1B-0. 1Y alloy [J]. Titan. Ind. Progr.,2018,35 ( 3) : 11-15.
[67] 纪小虎,李萍,时迎宾,等. TA15 钛合金等温多向锻造晶粒 细化机理与力学性能 [J]. 中国有色金属学报,2019,29( 11) : 2515-2523.
JI Xiaohu,LI Ping,SHI Yingbin,et al. Grain refinement mechanism and mechanical properties of TA15 alloy during multi-directional isothermal forging [J]. Chin. J. Nonferrous Met.,2019,29( 11) : 2515-2523.
[68] 周义刚,曾卫东,李晓芹,等. 钛合金高温形变强韧化机理 [J]. 金属学报,1999,35 ( 1) : 45-48.
ZHOU Yigang,ZENG Weidong,LI Xiaoqin,et al. An investigation of high-temperature deformation strengthening and toughening mechanism of titanium alloy [J]. Acta. Metall. Sin.,1999,35( 1) : 45-48.
[69] 张启飞,金淼,陈雷,等. 近 α 型钛合金航空锻件宏观清晰晶 形成机理及预测模型 [J]. 机械工程学报,2021,57 ( 8) : 133 -145.
ZHANG Qifei,JIN Miao,CHEN Lei,et al. Formation mechanism and prediction model of macro clear grains in near α titanium alloy aviation forgings[J]. J. Mech. Eng.,2021,57 ( 8) : 133-145.
[70] ZHANG Q F,JIN M,ZHANG Y S,et al. Experimental investigation on kinetic behavior of the deformation-induced α β transformation during hot working of Ti-6Al-2Zr-1Mo-1V alloy below theβ-transus[J]. Mater. Sci. Eng.,2022,A843: 143110.
[71] LUO S Y,WANG Q,ZHANG P,et al. Effect of friction conditions on phase transformation characteristics in hot forging process of Ti-6Al-4V turbine blade[J]. J. Mater. Res. Technol.,2020,9( 2) : 2107-2115.
[72] ZHENG G M,MAO X N,TANG B,et al. Evolution of microstructure and texture of a near α titanium alloy during forging bar into disk [J]. J. Alloys Compd.,2020,831: 154750.
[73] MENG L,KITASHIMA T,TSUCHIYAMA T,et al. Effect of αprecipitation on β texture evolution during β-processed forging in a near-β titanium alloy [J]. Mater. Sci. Eng.,2020, A771:138640.
[74] SUN Z,YANG H. Microstructure and mechanical properties of TA15 titanium alloy under multi-step local loading forming [J]. Mater. Sci. Eng.,2009,A523: 184-192.
[75] 胡轶嵩,王凯旋,姜葳,等. β 锻造工艺对 TC17 钛合金组织和力学性能的影响 [J]. 热加工工艺,2020,49 ( 9) : 41-44.
HU Yisong,WANG Kaixuan,JIANG Wei,et al. Effect of β forging process on microstructure and mechanical properties of TC17 titanium alloy [J]. Hot Work. Technol.,2020,49 ( 9) : 41-44.
[76] PETERS J,LÜTJERING G. Comparison of the fatigue and fracture of α+β and β titanium alloys [J]. Metall. Mater. Trans.,2001,32A: 2805.
[77] 刘汉青,何超,黄志勇,等. TC17 合金超高周疲劳裂纹萌生 机理 [J]. 金属学报,2017,53 ( 9) : 1047-1054.
LIU Hanqing,HE Chao,HUANG Zhiyong,et al. Very high cycle fatigue failure mechanism of TC17 alloy [J]. Acta. Metall. Sin.,2017,53 ( 9) : 1047-1054.
[78] 杨瑞,马英杰,雷家峰,等. 高强韧钛合金组成相成分和形态 的精细调控 [J]. 金属学报,2021,57 ( 11) : 1455-1470.
YANG Rui,MA Yingjie,LEI Jiafeng,et al. Toughening high strength titanium alloys through fine tuning phase composition and refining microstructure [J]. Acta. Metall. Sin.,2021,57 ( 11) :1455-1470.
[79] WU G Q,SHI C L,SHA W,et al. Effect of microstructure on the fatigue properties of Ti-6Al-4V titanium alloys [J]. Mater. Des.,2013,46: 668-674.
[80] HUANG C W,ZHAO Y Q,XIN S W,et al. Effect of microstructure on high cycle fatigue behavior of Ti-5Al-5Mo-5V-3Cr-1Zr titanium alloy [J]. Int. J. Fatigue,2017,94: 30-40.
[81] 张赛飞,赵兴东,徐强,等. β 锻 TC17 钛合金的高周疲劳研 究 [J]. 热加工工艺,2015,19 ( 4) : 123-126.
ZHANG Saifei,ZHAO Xingdong,XU Qiang,et al. Study on high cycle fatigue of β-forged TC17 titanium alloy [J]. Hot Work. Technol.,2015,19 ( 4) : 123-126.
[82] ZHANG S F,ZENG W D,ZHAO Q Y,et al. High cycle fatigue of isothermally forged Ti-6. 5Al-2. 2Mo-2. 2Zr-1. 8Sn-0. 7W-0. 2Si with different microstructures[J]. J. Alloys Compd.,2016,689:114-122.
[83] SUN C Q,LI Y Q,XU K L,et al. Effects of intermittent loading time and stress ratio on dwell fatigue behavior of titanium alloy Ti6Al-4V ELI used in deep-sea submersibles [J] J. Mater. Sci. Technol.,2021,77: 223-236.
[84] LIU F L,PENG H T,LIU Y J,et al. Crack initiation mechanism of titanium alloy in very high cycle fatigue regime at 400℃ considering stress ratio effect [J]Int. J. Fatigue,2022,163: 107012.
[85] 刘小龙,孙成奇,周砚田,等. 微结构和应力比对 Ti-6Al-4V高周和超高周疲劳行为的影响 [J]. 金 属 学 报,2016,52( 8) : 923-930.
LIU Xiaolong,SUN Chengqi,ZHOU Yantian,et al. Effect of microstructure and stress ratio on high-cycle and very-high-cycle fatigue behavior of Ti-6Al-4V alloy [J]. Acta. Metall. Sin.,2016,52 ( 8) : 923-930.
相关链接