1、 序言
钛合金因其特殊属性成为在航空航天领域应用广泛的零件材料,但硬度高、切削性能差,故属于难加工材料,加工中易产生零件表面硬化,给机械加工带来了很大挑战。
通常用于加工钛合金的刀具材料对硬度和耐磨性要求较高,且需要具备极好的耐热性。在高温下仍能保持较高强度、韧性、一定的抗冲击性和抗破坏性,满足以上要求的刀具有:陶瓷刀具、涂层硬质合金刀具、立方氮化硼(CBN)刀具和金刚石(PCD)刀具等。其中涂层硬质合金刀具价格低,且具有较好的导热性和较高的硬度,虽然其耐热性和化学稳定性较陶瓷刀具、立方氮化硼刀具和类金刚石刀具差一些,但较强的抗冲击性和抗破坏性使其成为加工钛合金的首选刀具。选用刀具的几何角度时,要求具有较小前角、刃倾角负倒棱、主偏角和负偏角同时拥有较大后角。
2、 钛合金材料切削参数优化与应用
图1所示零件材料为TC11钛合金,悬臂与接头为一体结构,零件部位划分如图2所示,加工过程实体如图3所示。
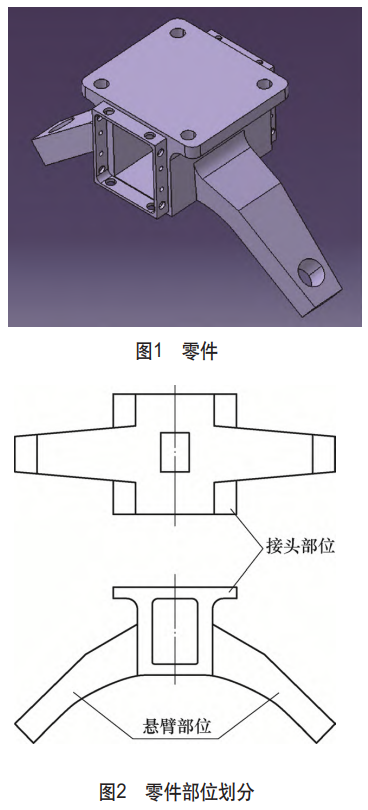
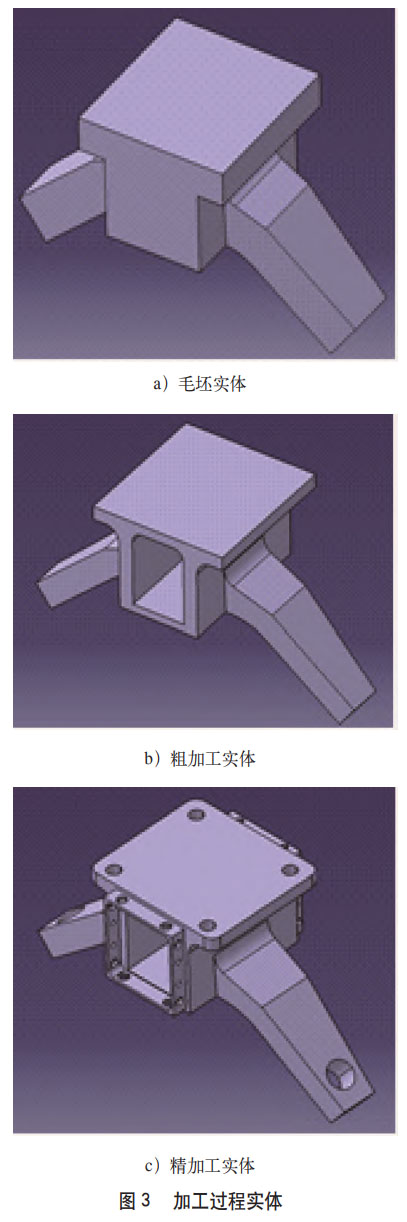
加工难点如下所述:
毛坯为重型自由锻件,表面有较硬的硬化层,形状不规则,加工完成后材料去除率超过80%,加工余量大、难度高。
中间槽腔较深,约400mm,且槽腔尺寸精度高,加工中切削参数不合理,无法保证尺寸精度。
悬臂部分悬伸>600mm,加工中切削参数不合理,易产生振动,影响零件表面质量。
由于是首次加工TC11钛合金材料,加工此类材料的刀具种类和数量有限,同时考虑新进刀具会增加加工成本,导致加工过程中不易设置精加工切削参数,粗加工初始阶段的刀具寿命与加工效率较低。
TC11钛合金属于难加工材料,通过对钛合金材料加工性能的研究,结合零件的结构特征以及较大的去除率,从刀具选用、加工策略选择及加工参数摸索3个方面进行切削优化[4]。
3、刀具选用
结合钛合金机械加工特性,优先使用涂层硬质合金可转化立铣刀加工钛合金材料,去除大部分机械加工余量。由于零件表面有较硬的硬化层,严重影响刀具寿命,因此选择合适的涂层刀具尤为重要,对刀具成本的影响也最大[5]。
在刀具性能的提升策略中,涂层技术无疑占据着至关重要的地位,刀具涂层犹如为刀具披上了一层坚固而精密的“铠甲”,显著增强了在切削过程中的耐磨、耐热和抗腐蚀能力。
目前,先进的涂层工艺层出不穷,常见的涂层材料包括类金刚石(DLC)涂层、氮化钛(TiN)涂层和碳化钛(TiC)涂层等。DLC涂层具有极低的摩擦系数和出色的耐磨性,能够有效减少刀具与工件之间的摩擦,降低切削力,减少热量产生,从而延长刀具的使用寿命。TiN涂层以其良好的硬度和化学稳定性,为刀具提供了可靠防护,使其在高速切削中依然能保持优异的性能[6]。TiC涂层虽然硬度略低于DLC涂层,但高温稳定性优于TiN涂层,对高温稳定性要求高以及需要避免切削液污染(如医疗零件加工)的干式切削场景来说,该涂层的应用至关重要。
涂层的制备方法也多种多样,如物理气相沉积(PVD)技术和化学气相沉积(CVD)法。PVD技术能够在低温下实现涂层的沉积,有效避免刀具基体高温变形的同时可以精确控制涂层的厚度和成分;CVD法则适用于制备较厚的涂层,具有较高的沉积率和良好的结合强度。
通过了解不同涂层技术,结合刀具成本分析,最终采用物理气相沉积(PVD)技术制备的氮化钛铝(TiAlN)涂层刀具进行零件的粗、精加工。
现有能用于钛合金加工的四边形刀片,经尝试发现寿命均较短。通过查阅大量的相关刀具资料,联系相关刀具企业,在粗加工过程中选定了较为适合钛合金加工的圆形刀片(外径12mm)进行尝试,粗加工实体如图4所示,圆形刀片相较之前所选刀片,同样的背吃刀量,切削刃与工件的接触面积更大,相对散热性更好,且此形状刀片每旋转120°使用1次,1个刀片可旋转3次,即可使用3次,刀具寿命相对提高。
精加工实体如图5所示,图中着色区域代表工序加工内容。精加工过程中,选用高铣类合金钻头,此类钻头与钛合金亲和力小,导热性能良好,强度较高。较孔时分两部分进行,粗铰选用普通铰刀(留余量0.1mm),精铰选用合金铰刀。铣外形选用Φ12mm整体硬质合金立铣刀分层加工,该铣刀相比普通立铣刀,具备导热性好、硬度高、不易变形且切削性能稳定等优点,适合加工钛合金材料。
4、加工策略选择
无论是粗加工还是精加工,在加工悬臂部分(见图4a和图5b红色区域)时,由于刀具悬伸长,刚性下降,故刀具与零件之间极易产生振动,严重时甚至会导致刀具崩刃或损坏,影响零件表面质量,若合理选择加工刀路,就可以避免振动。粗加工阶段采取大直径刀具分层加工,按照一定深度分多个层次、逐层进行铣削,能够有效降低单次铣削的切削力,减少刀具负载,从而延长刀具寿命。对精加工而言,由于悬臂存在多个倾斜平面(见图5b、图5c深蓝色区域),故需采用五轴定平面加工,刀具轴垂直于加工平面,使切削力分布更加均匀,刀具与工件间的接触更加平滑,减少切削热产生和避免刀具局部过度磨损的同时,降低刀具的热疲劳损伤。五轴加工还能使用更短的刀具,增加刀具的刚性,进一步减少刀具的振动和变形,有助于延长刀具的使用寿命。
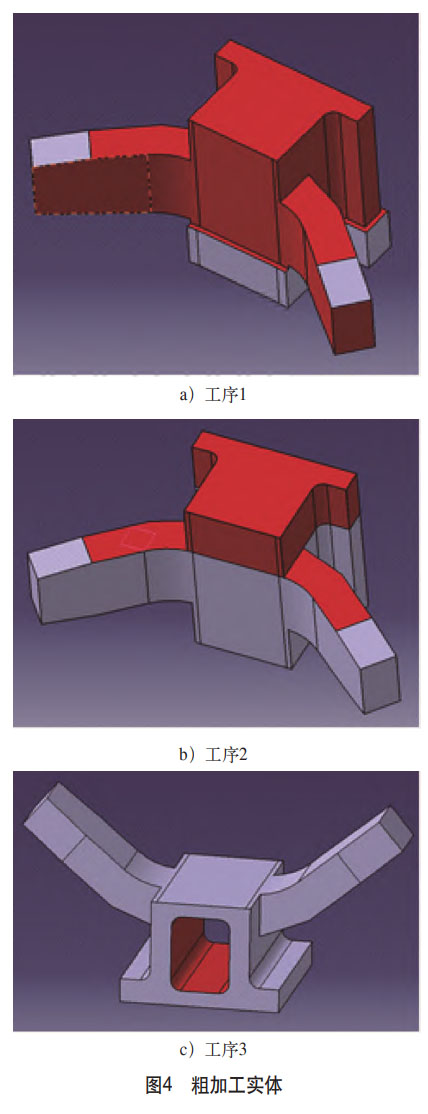
中间部位贯通封闭槽腔(见图4c),容易出现刀具因挤屑而损坏的情况,需采取卧式加工方法,切屑在重力作用下能更顺畅地排出,减少切屑堆积对加工的影响,使排屑更为高效,同时也降低了刀具与切屑之间的摩擦和热量,有助于延长刀具寿命。由于槽的深度达到350mm,因此需先选择悬伸短、再选择悬伸长的刀具进行加工,同时要防止悬伸长的刀具产生振动。粗加工主要考虑加工刀路对表面质量的影响,同样采用分层铣削的方式提高加工表面质量。由于切削力减少,加工过程中的振动和变形也相应减少,因此加工表面会更加光滑。
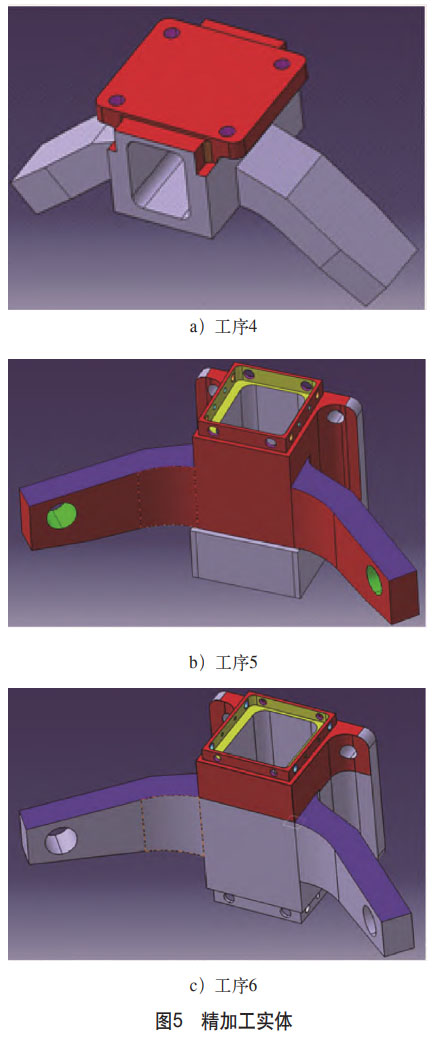
5、加工参数设置
5.1 粗加工切削参数
试切初期由刀具前提供初始切削参数,刀具寿命不是很理想,技术人员和操作人员通过相关数据分析和搜索,得到加工零件用的合理切削参数,设备选用VMC1700立式加工中心(见图6)。
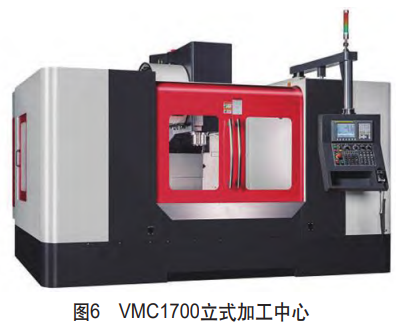
选用山特维克可乐满刀具,分别为Φ50mm可转位立铣刀片,型号:490R-08T308M-MM/S30T;Φ52mm可转位立铣刀片,型号:R300-1240E-PMS30T;Φ80mm可转位立铣刀片,型号:R300-1240E-PMS30T。
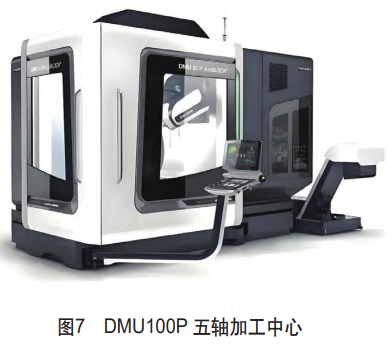
粗加工过程中,由于零件大部分为毛坯表面,导致刀具磨损进一步加强,现场测试时刀具切削参数见表1。初始加工时,刀具加工出来的切屑为卷状,表面光滑,仅2h后,切屑变为长条状,表面褶皱似挤压状,加工磨损出现在一瞬间,前一分钟还正常加工,后一分钟刀具已经不能再使用,需要更换刀片。为节约成本,提高效率,将转速、进给速度和背吃刀量进行测试调节,生产效率得到了一定提高,加工寿命由原来的最长2h(同时考虑不可预料的刀具磨损),变为较稳定的3h,加工后换刀的定时损耗比生产不至于停滞。继续调整参数,最终测试出较完善的参数,优化后的刀具切削参数见表2,更换刀片的时间可以延长至6~7h,大大降低了刀具成本。
表1 现场测试时刀具切削参数
刀具直径/mm | 刀片类型 | 加工位置 | 转速(r/min) | 进给速度(mm/min) | 背吃刀量/mm |
80 | 圆弧 | 圆弧 | 180 | 105 | 2 |
52 | 圆弧 | 圆弧 | 200 | 120 | 2 |
50 | 方角 | 方角 | 300 | 150 | 2 |
表2 优化后的刀具切削参数
刀具直径/mm | 刀片类型 | 加工位置 | 转速(r/min) | 进给速度(mm/min) | 背吃刀量/mm |
80 | 圆弧 | 圆弧 | 110 | 110 | 2 |
52 | 圆弧 | 圆弧 | 150 | 150 | 2 |
50 | 方角 | 方角 | 150 | 150 | 2 |
5.2 精加工切削参数
相比粗加工阶段,精加工阶段由于加工余量减少,相同直径的刀具,其转速、进给速度和背吃刀量均有所提高,但不能与粗加工一样维持恒定数值,存在一定变化幅度,在加工时需不断调整。精加工阶段还需考虑钻孔、铰孔时刀具的选用,由于切削参数不合理,因此相比铰刀更容易产生硬化现象,导致加工孔径变形,造成零件报废。精加工的槽腔宽度尺寸精度高,还需考虑切削参数尺寸精度的影响。
DMU100P五轴加工中心如图7所示。以φ50mm可转位立铣刀为例,选用瓦尔特刀具,型号WALTER 116166,刀片类型:ADMT120430R-F56 WSM35,加工外形、型腔等。φ50mm飞刀部分切削参数见表3,精加工部分刀具切削参数见表4。
在加工过程中,克服加工经验少以及现有刀具的不足,通过对粗、精加工刀具参数(转速、进给速度和背吃刀量)的不断尝试和优化,确定出合理的切削参数。
表3 φ50mm飞刀部分切削参数
刀柄型号 | 加工位置 | 转速/(r/min) | 进给速度/(mm/min) | 背吃刀量/mm | 切削宽度/mm | 刀片寿命/min |
HSKA100 |
| 150~250 | 130~170 | 1~3 | 25~35 | 450~500 |
SK40 | 图5红色区域 | 150~250 | 130~170 | 1~3 | 25~35 | 400~450 |
HSKA63 |
| 150~250 | 130~170 | 1~3 | 25~35 | 400~450 |
表4 精加工部分刀具切削参数
刀具 | 加工位置 | 转速/(r/min) | 进给速度/(mm/min) | 背吃刀量/mm |
φ25mm飞刀 | 图5b~图5c深蓝色区域 | 300~500 | 100~200 | 1~3 |
φ12mm立铣刀 | 图5b~图5c黄色区域 | 200~500 | 80~150 | 3~7 |
φ12mm倒角刀 | 图5所有孔口倒角 | 500~800 | 80~150 | 1~3 |
φ48mm镗刀 | 图5b绿色区域 | 100~250 | 10~40 | 1 |
φ52mm飞刀 | 图5b~图5c深蓝色区域 | 200~300 | 150~300 | 1~3 |
φ25mm合金立铣刀 | 图5b绿色区域 | 200~500 | 100~200 | 2 |
φ20mm合金立铣刀 | 图5a红色区域 | 200~500 | 100~200 | 10 |
φ10mm立铣刀 | 图5a绿色区域 | 200~500 | 30~70 | 5 |
φ80mm飞刀 | 图5a红色区域 | 100~300 | 100~300 | 1~3 |
φ50mm飞刀 | 图5a红色区域 | 105~300 | 100~300 | 1~3 |
φ19.8mm钻头 | 图5a紫色区域 | 200~500 | 10~50 | — |
φ20mm铰刀 | 图5a绿色区域 | 50~100 | 10~30 | 0.2 |
φ3.3mm钻头 | 图5a绿色区域 | 500~800 | 10~50 | — |
φ5mm合金钻头 | 图5b浅蓝色区域 | 200~500 | 10~50 | — |
φ7.2mm合金钻头 | 图5b浅蓝色区域 | 200~500 | 10~50 | — |
φ8mm合金钻头 | 图5b绿色区域 | 200~500 | 10~50 | — |
φ10mm合金钻头 | 图5b绿色区域 | 200~500 | 10~50 | — |
φ6.8mm钻头 | 图5b绿色区域 | 200~500 | 10~50 | — |
φ27mm U形钻头 | 图5b绿色区域 | 100~300 | 10~30 | — |
6、结束语
通过介绍钛合金材料机械加工性能,结合关键零件在机械加工过程中的难点问题,不断尝试和优化切削参数,有效提高了数控加工效率,提高了刀具寿命并减少了刀具成本。为公司今后加工此类钛合金材料零件积累了宝贵的机械加工经验,也使公司先进制造技术水平有所提高。
参考文献:
[1] 陈日曜. 金属切削原理[M]. 2版. 北京:机械工业出版社, 2013.
[2] 刘鸿文. 材料力学[M]. 6版. 北京:高等教育出版社, 2017.
[3] 黄旭, 朱知寿, 王红红. 先进航空钛合金材料与应用[M]. 北京:国防工业出版社, 2012.
[4] 赵永庆. 中国有色金属丛书:钛和钛合金相图谱[M]. 长沙:中南大学出版社, 2011.
[5] 陈宏钧. 实用机械加工工艺手册[M]. 3版. 北京:机械工业出版社, 2009.
[6] 尹成滢. 机械加工工艺手册[M]. 北京:化学工业出版社, 2023.
相关链接