钛合金板凭借轻量化、高强度、耐腐蚀等核心特性,在航空航天、海洋工程、化工新能源、医疗电子等领域广泛应用,但国内外技术差距显著:国内以热轧为主,大尺寸板材依赖进口,表面处理(如微弧氧化、激光熔覆)与焊接技术(电子束焊国产化率不足30%)落后国际5-8年,航空航天领域宽幅薄板(如C919机身TC4板材厚度1-3mm,对比波音787的0.8mm级)和高温合金(WS-15发动机TA15耐温600℃ vs GE9X的650℃+)存在代差;海洋工程中深海耐压壳体焊接缺陷率较高,船舶管路成形技术待突破,但国内宝钛集团已实现3.2m宽幅TC4板材量产,并在钛-钢复合板等低成本制备(成本降40%)上取得进展。医疗领域3D打印多孔钛板逐步推广,但生物活性涂层技术仍落后,消费电子超薄板(<0.2mm)轧制尚未突破。国际市场由美俄日主导,国内依托成本优势(TC4价格低20%)和中低端产能,正加速布局氢能储运、海上风电等新兴领域,未来需攻克宽幅薄板轧制、高强β合金(如Ti-5553强度1250MPa)、表面功能化三大瓶颈,并拓展太空超低温(-253℃)等极端环境应用,预计2025年全球市场规模将超50亿美元,国内政策驱动下有望在高端市场实现技术突围与产业链升级。
一、钛合金板的核心特性与加工技术对比
维度 | 国内技术现状 | 国际技术现状 | 差距与趋势 |
板材制备工艺 | 以热轧为主,大尺寸板材(宽度>3m)依赖进口 | 超宽幅轧制(宽度>4m)、冷轧精密板材技术成熟 | 国内在轧制设备精度与稳定性上存在短板 |
表面处理技术 | 常规酸洗、喷砂为主,高端涂层技术尚在研发 | 微弧氧化(MAO)、激光熔覆等先进表面改性普及 | 功能性涂层(抗菌、耐磨)应用滞后5-8年 |
焊接工艺 | TIG焊为主,电子束焊应用受限 | 真空电子束焊、激光焊普及,自动化焊接率达60% | 高能束焊接设备国产化率不足30% |
二、航空航天领域应用对比
应用场景 | 国内典型应用 | 国际典型应用 | 技术差距与突破方向 |
机身蒙皮板 | C919机身局部采用TC4板材(厚度1-3mm) | 波音787机身50%使用Ti-6Al-4V板材(整体减重15%) | 国内宽幅薄板(<0.8mm)成形精度不足 |
发动机燃烧室 | WS-15发动机使用TA15板材(耐温600℃) | GE9X发动机采用Ti-6242S板材(耐温650℃+) | 高温钛合金板材持久强度低10%-15% |
航天器储箱 | 长征五号液氢储箱用TB5板材(β钛合金) | SpaceX星舰液氧储箱采用Ti-3Al-2.5V板材 | 超低温(-253℃)韧性控制技术待突破 |
案例对比:
国内突破:宝钛集团研制出宽幅3.2m的TC4板材,用于C919机翼结构。
国际前沿:美国ATI公司开发出Ti-5553(Ti-5Al-5Mo-5V-3Cr)板材,强度达1250MPa,用于F-35机身框架。
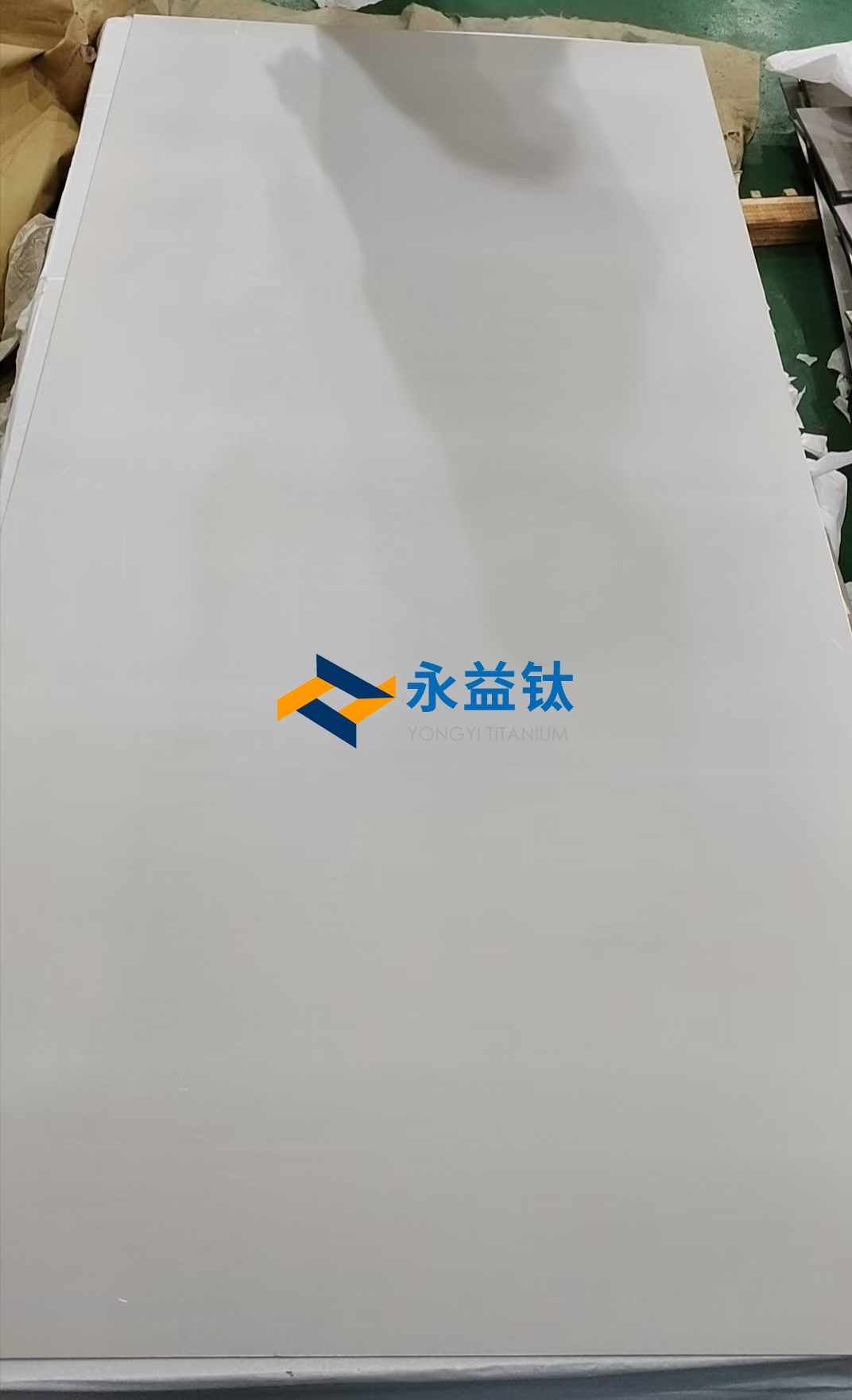
三、海洋工程与船舶制造应用
应用方向 | 国内应用现状 | 国际应用现状 | 核心挑战 |
深海耐压壳体 | “蛟龙号”载人舱使用TA5板材(厚度80mm) | 美国“阿尔文号”采用Ti-6Al-4V ELI板材 | 大厚度(>100mm)板材焊接缺陷率较高 |
船舶海水管路 | 055型驱逐舰部分管路采用TA2板材 | 俄罗斯“北风之神”核潜艇全钛合金管路系统 | 国内弯管成形技术导致壁厚均匀性差 |
海洋平台结构 | 南海油气平台使用TA10(Ti-Mo)防腐板材 | 挪威Equinor平台采用Gr.29(Ti-6Al-4V ELI) | 抗微生物腐蚀涂层技术未规模化应用 |
技术纵深:
国内突破:中国船舶725所开发出钛-钢复合板爆炸焊接技术,成本降低40%。
国际趋势:日本JFE钢铁推出钛-不锈钢三层复合板,实现管路系统轻量化与耐蚀性平衡。
四、化工与新能源领域应用
应用场景 | 国内典型案例 | 国际典型案例 | 材料创新方向 |
PTA反应器 | 恒力石化200万吨/年装置使用TA9(Ti-0.2Pd)板 | 韩国乐天化学采用Gr.7(Ti-0.15Pd)板材 | 低钯(Pd)含量合金开发(如Ti-0.05Pd) |
氢能储运 | 国富氢能35MPa储氢罐用TC4板材 | 日本川崎重工液氢运输船采用Ti-3Al-2.5V板材 | 抗氢脆板材(如Ti-6Al-4V ELI)研发加速 |
核电站冷凝器 | 宁德核电使用TA10(Ti-Mo)板式换热器 | 法国EPR机组采用Gr.12(Ti-0.3Mo-0.8Ni)板材 | 抗缝隙腐蚀合金设计(如Ti-0.5Ni-0.01Ru) |
成本对比:
国内TA9板材成本约¥800/kg,国际Gr.7板材¥1200/kg,但寿命差距达2-3倍。
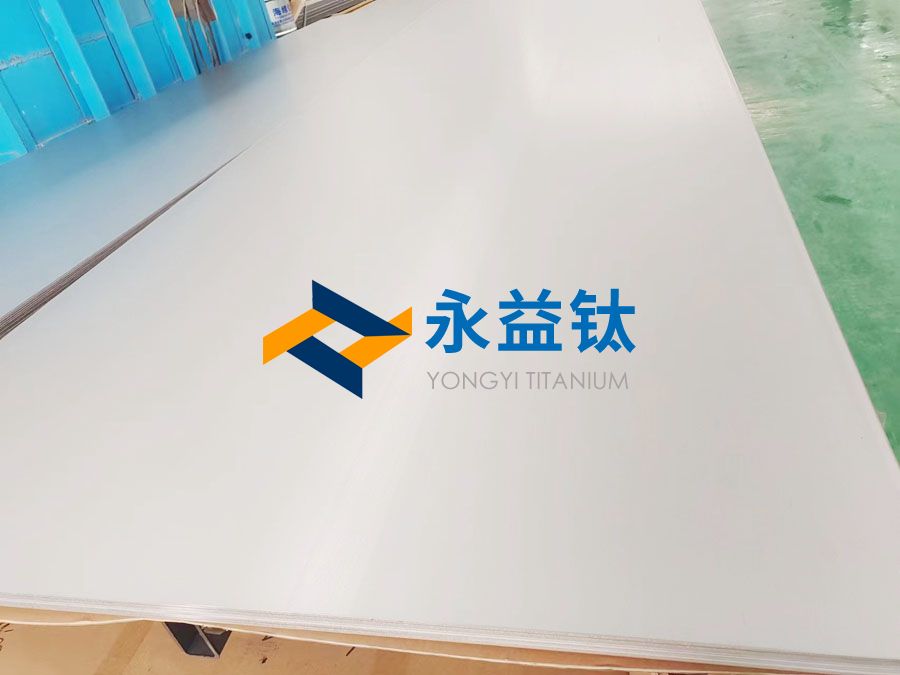
五、医疗与消费电子领域应用
应用方向 | 国内进展 | 国际进展 | 技术代差 |
骨科植入板 | 威高骨科推出3D打印多孔TC4骨修复板 | 美国Zimmer公司纳米晶Ti-13Nb-13Zr板材 | 生物活性表面处理技术差距显著 |
消费电子外壳 | 小米MIX Fold2铰链采用TC4超薄板(0.3mm) | 苹果Apple Watch Ultra表壳使用Grade 5板材 | 超薄板(<0.2mm)轧制技术尚未突破 |
牙科种植板 | 创英医疗纯钛(TA2)基台板材 | 瑞士Straumann Roxolid®(Ti-15Zr)板材 | 高强牙科合金(屈服强度>800MPa)缺失 |
创新案例:
国内突破:西北院开发出Ti-2448(Ti-24Nb-4Zr-8Sn)板材,弹性模量接近人骨。
国际前沿:德国Heraeus推出抗菌钛板(Ag/TiO₂涂层),杀灭率>99.9%。
六、国内外市场格局与未来趋势
维度 | 国内市场特征 | 国际市场特征 | 发展预测 |
头部企业 | 宝钛股份(产能2万吨/年)、西部超导 | VSMPO-AVISMA(俄)、Timet(美)、东邦钛(日) | 国内企业加速海外并购(如宝钛收购美国Tico) |
价格竞争 | TC4板材¥300-400/kg(较国际低20%) | 国际均价$60-80/kg(受航空航天需求拉动) | 国内低成本制备技术(如氢化脱氢法)突破 |
新兴应用 | 氢能储运、海上风电支撑结构需求激增 | 太空旅游装备(如维珍银河飞船钛板用量+200%) | 2025年全球钛板市场规模将突破$50亿 |
政策驱动:
中国《新材料产业发展指南》将高端钛板列为重点攻关方向。
欧盟“清洁天空2.0”计划推动航空钛板减重30%目标。
总结与建议
国内优势:成本竞争力强,中低端板材产能充足;
突破重点:攻克宽幅薄板轧制、高强β合金板材、表面功能化三大技术瓶颈;
市场机遇:氢能、海洋工程、3C电子领域将催生百亿级增量需求;
国际合作:引进高能束焊接设备技术,共建太空用超低温钛板标准体系。
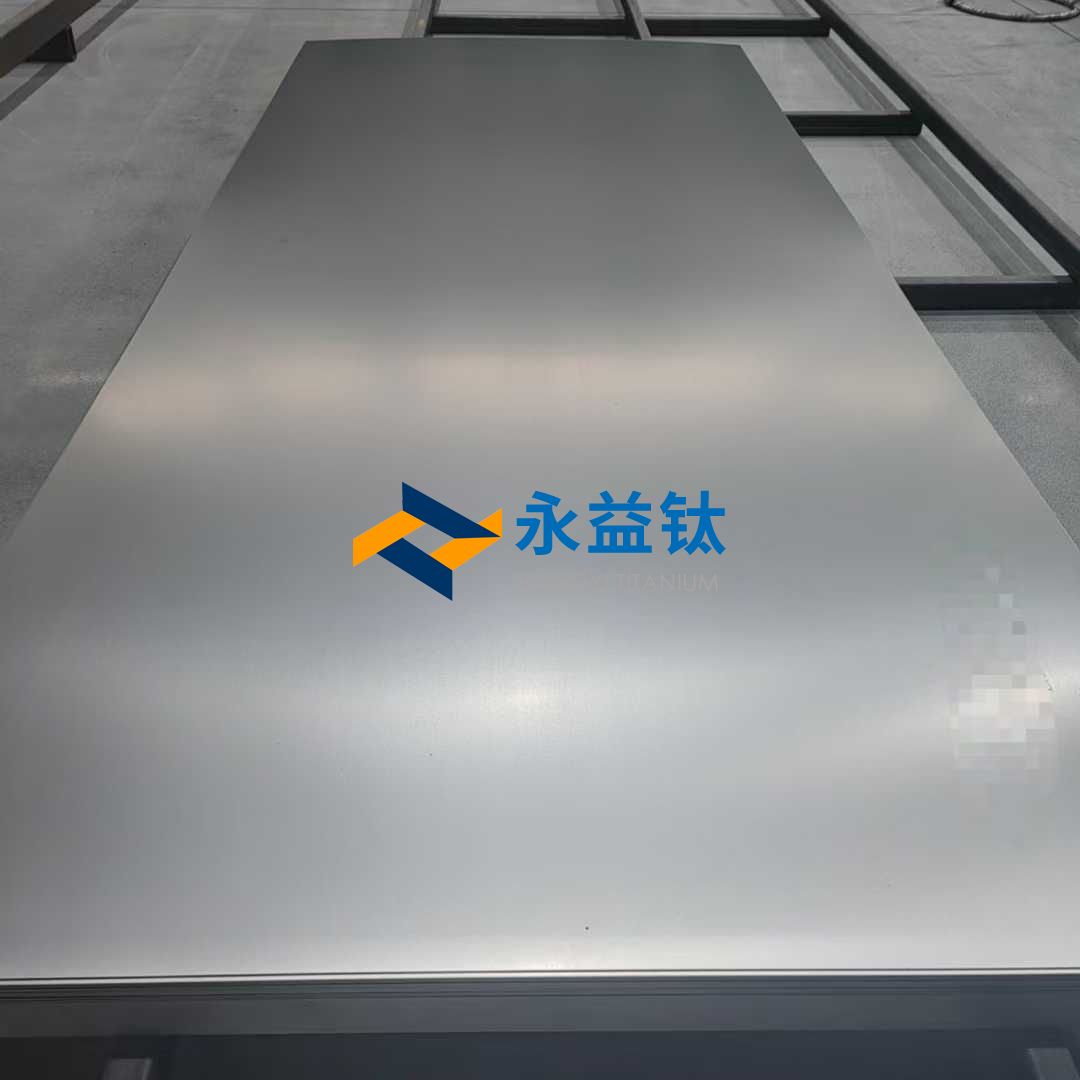
通过纵深分析可见,钛合金板的应用正从“规模扩张”向“高附加值”转型,国内外技术代差逐步缩小,但在高端应用领域仍需持续突破。
相关链接