航空钛合金锻件作为现代航空器的核心承力结构,其性能直接决定飞行器的安全边界与效能极限。国产大飞机C919起落架采用TC4-DT(损伤容限型)钛合金锻件,通过β热处理形成网篮组织,使断裂韧性KIC≥75MPa·m¹/²,较传统TC4提升40%,支撑30万次起降寿命要求;而歼-20战机的机身主承力框采用Ti-6Al-4V ELI超低间隙元素锻件,经等温锻造后疲劳强度达600MPa(R=0.1),较常规锻造件提高35%。据中国航发集团数据,新一代涡扇发动机中钛锻件占比已超25%,其中高压压气机盘采用Ti-6242S合金,在550℃/650MPa条件下持久寿命突破300小时,较镍基合金减重30%。西部超导依托6吨级真空自耗炉(VAR)熔炼的TA19(Ti-6Al-2Sn-4Zr-2Mo)合金锻棒,成功应用于长江-1000A发动机风扇盘,实现晶粒度ASTM 7级均质化,打破普惠对宽弦叶片的垄断。
一、航空钛合金锻件制造正经历三大技术范式转型:
1. 多场耦合精密成形
中航重机针对TC18合金开发“电磁场辅助等温锻”技术:在α+β两相区(920±15℃)施加10T稳恒磁场,使β相织构强度从7.5降至2.3,解决大型机翼接头各向异性难题,疲劳寿命离散度缩小50%。
2. 组织遗传性破译
中科院金属所揭示初生α相(≥15%)对β晶界钉扎效应是微织构遗传主因,据此优化TC25G合金“三火次跨相区锻造”工艺:
β区开坯(Tβ+50℃/变形量80%)破碎铸态晶粒
α+β区改锻(Tβ-30℃/三向镦拔)细化初生α相
近β终锻(Tβ-10℃)形成5–8μm条状α相
使发动机涡轮盘650℃蠕变速率降至1×10⁻⁸/s,达国际领先水平。
3. 增材-锻造复合制造
航天一院采用激光沉积成形(LDED)+等温锻组合工艺制造长征九号氢氧发动机喷管支撑环:
先打印Ti-6Al-2Zr-1Mo-1V近净形坯体
在760℃/应变速率0.001s⁻¹条件下等温精锻
将传统23个零件集成为1件,减重40%且疲劳强度提升50%。
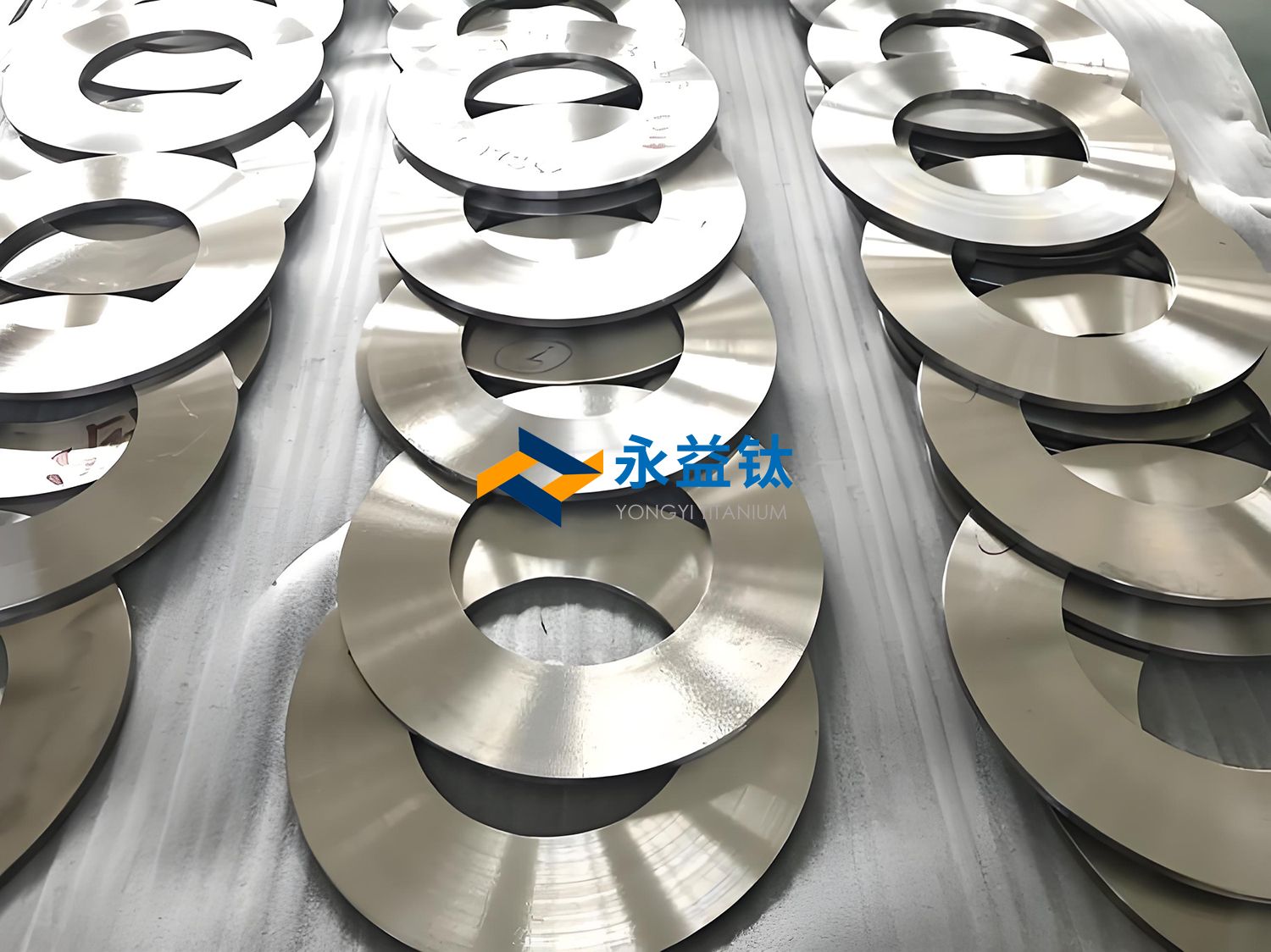
二、当前航空钛合金锻件面临三重技术鸿沟:
1. 超高温持久瓶颈
现有Ti-1100合金在600℃以上出现β相粗化,导致持久强度骤降40%。中国航发航材院通过Y₂O₃弥散强化(0.3wt%),将Ti-Al-Sn-Zr-Mo-Si系合金使用温度提至650℃(100h持久强度≥450MPa),满足第六代发动机需求。
2. 大尺寸构件均质化挑战
φ800mm以上锻件心部晶粒度波动达ASTM 3级。上海交大开发多向模锻+梯度控冷技术:在TC11合金φ850mm盘件锻造中采用芯部水冷+边缘风冷策略,使全截面晶粒差≤1.5级,超声探伤杂波降低20dB。
3. 疲劳性能与成本平衡
航空级TC4锻件成本达40万元/吨。宝钛集团创新EBCHM(电子束冷床炉)残钛再生工艺:将机加工屑料氧含量从2500ppm降至800ppm,制成TA15合金锻件疲劳极限达500MPa(ΔK=25MPa·m¹/²),成本降30%,已用于ARJ21机翼挂架。
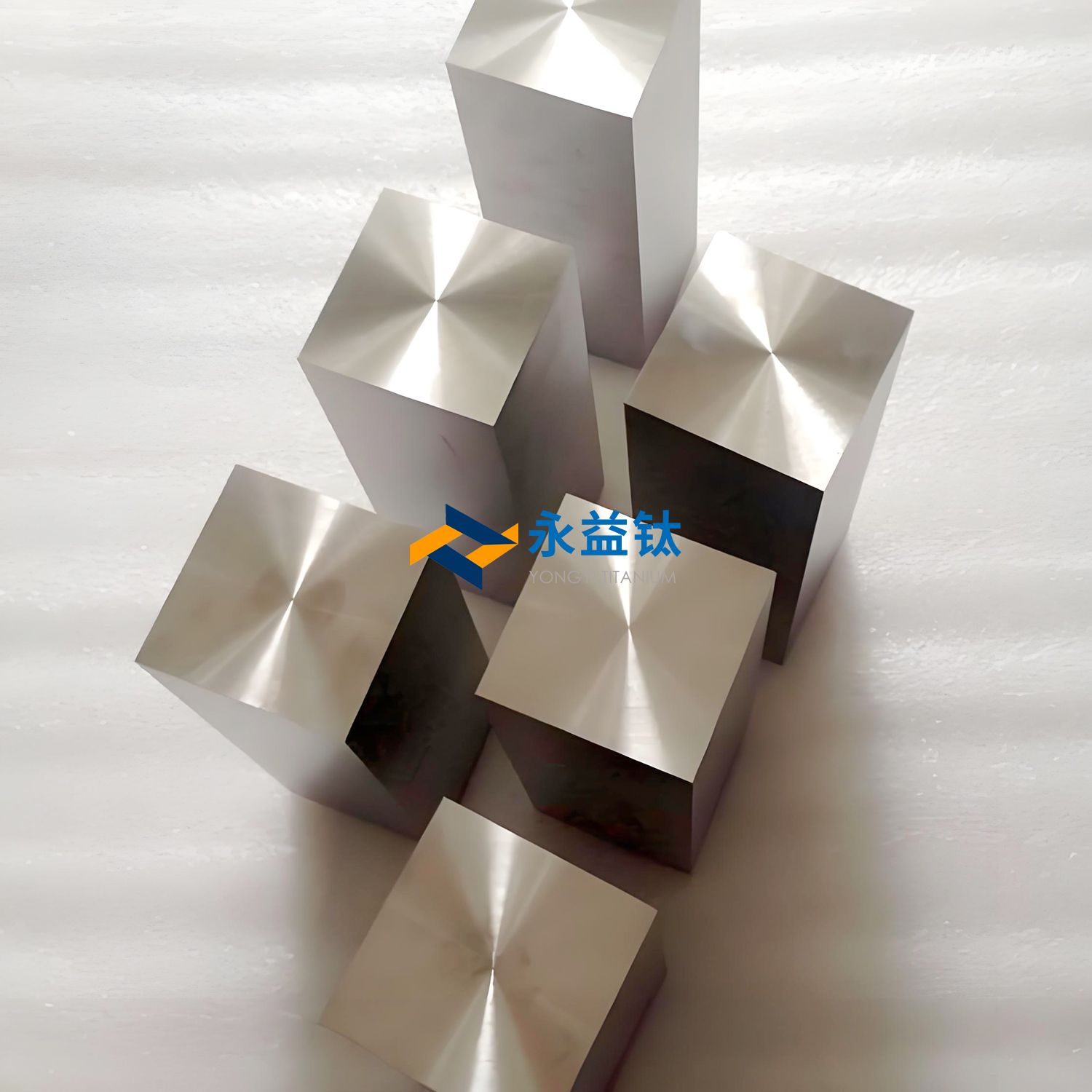
三、航空钛合金锻件产业正向三大方向演进:
1. 全流程数字化
航发科技建立锻造-热处理-检测数字孪生平台:通过DICT(衍射晶粒成像)技术实时监测TC4-DT锻件β晶粒尺寸,动态调整锻造参数,使批次稳定性提升90%。
2. 超塑性成形普及化
西工大开发780℃高应变速率(10⁻²s⁻¹)SPF/DB技术:将Ti-4Al-2V合金蒙皮扩散连接温度从920℃降至800℃,成形时间缩短70%,用于C929机翼前缘整体成形。
3. 低碳冶金突破
金天钛金建成全球首条绿氢供电VAR熔炼线:通过光伏制氢燃烧供热,使Ti-6Al-4V熔炼碳排放从18tCO₂/t降至2.3tCO₂/t,2025年将覆盖30%航空锻件产能。
四、熔炼与铸锭制备
真空自耗电弧熔炼(VAR)
采用三次熔炼工艺确保成分均匀性:首次熔炼(5–8 kA/20–30 V)去除挥发物;二次熔炼(8–15 kA/25–32 V/0.03–0.06 Pa真空度)深度提纯;三次熔炼(15–20 kA/25–35 V)实现成分微调,氧含量精确控制于0.20%–0.25%以提升强度。
典型案例:高强改性Ti-6Al-4V铸锭(直径Φ500mm)经此工艺后,棒材抗拉强度>960 MPa,探伤达GB/T 5193 A级标准。
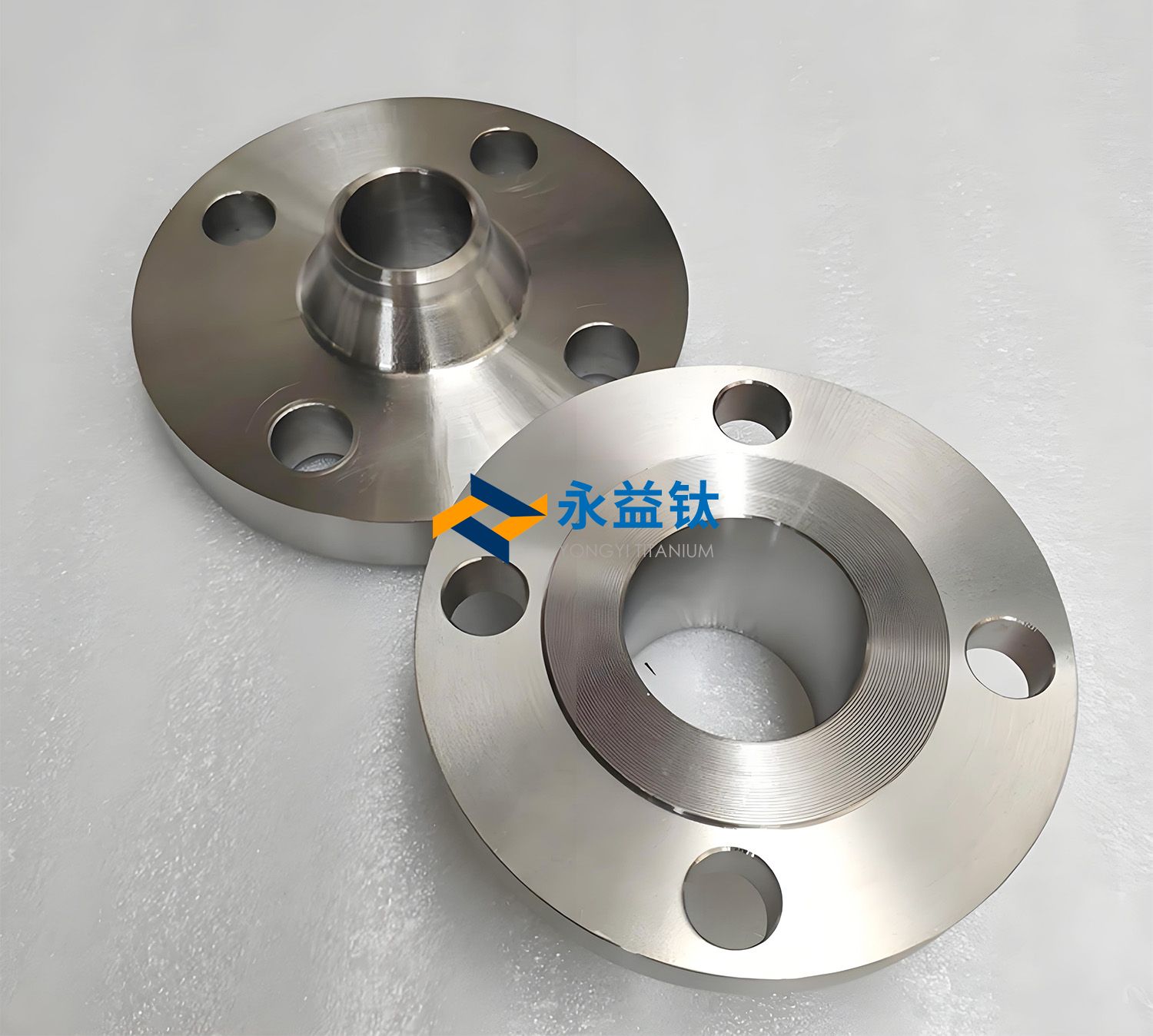
五、锻造工艺关键控制
(1)开坯锻造
温度控制:在β相变点(Tβ)以上100–160℃(如1150℃)进行大变形量(>80%)开坯,破碎铸态粗晶。
缺陷预防:高合金化牌号(如Ti2AlNb)需避免表面温降导致的横向开裂,冬季作业时需增加保温措施。
(2)改锻与组织调控
跨相区锻造:
两相区改锻(Tβ-50~-20℃):通过多火次镦拔(总锻比≥6.5)细化晶粒,如TC25G合金经此工序后初生α相≥20%。
β锻造(Tβ+10~40℃):针对高温部件(如发动机盘件),变形量40–80%形成网篮组织,使TC25G锻件的650℃蠕变抗力提升30%。
大规格棒材工艺:Φ300mm以上棒材易现心部粗晶,需采用“小变形-大压下-多道次”轧锻结合工艺(如中冶京诚BDM850轧机),实现Φ900mm铸锭直接轧至Φ85–350mm棒材。
(3)精密成形技术
等温模锻:模具与坯料同温(300℃预热),减少流动应力。例如钛合金盆形锻件采用“镦饼→冲孔→扩孔→模锻”4火次成形,比传统工艺减少6火次,材料利用率提高至85%。
复杂构件成形:陕西宏远航空针对TC18合金开发分模面优化技术,采用纺锤状荒形设计,解决三角形区流线不对称问题,提升发动机壳体疲劳寿命50%。
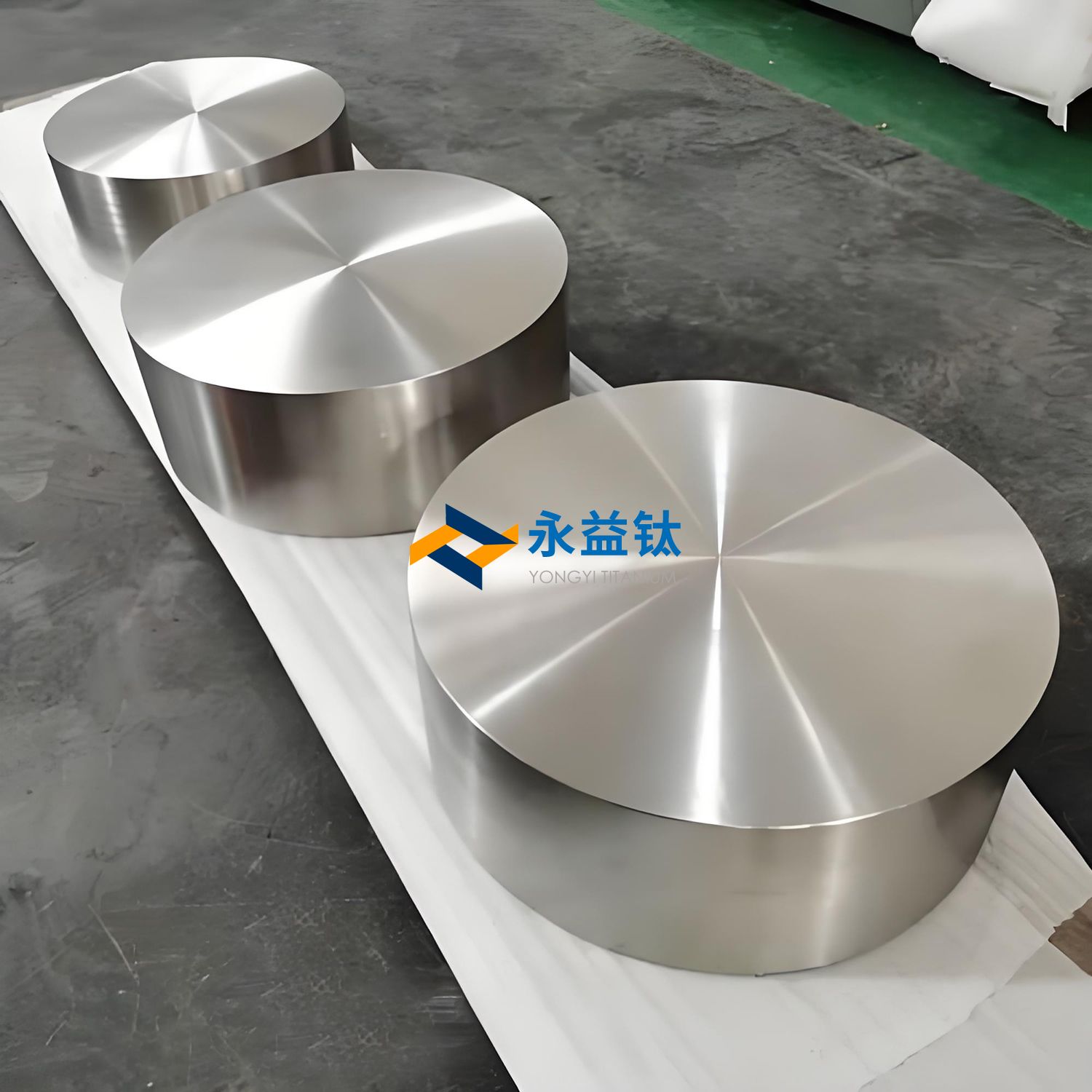
六、热处理与组织优化
固溶+时效双重处理
TC25G采用β固溶(Tβ-60~-20℃)后空冷+540–590℃时效,使网篮组织的断裂韧性KIC达70 MPa·m¹/²。
三态组织制备
Ti-6242合金经近β固溶→重复固溶→时效,形成初生α相(5–35%)+条状α相(10–30%)+β转变组织的三态结构,破解强度与持久性能匹配难题,用于航空发动机高压压气机盘7。
七、先进制造技术应用
激光增材制造(3D打印)
直接制造大型主承力构件:如歼-15的“眼镜式”钛合金加强框(投影面积>12m²),较锻造减重40%,成本降至传统工艺5%。
智能微铸锻技术:铸造与锻压同步,使歼-20起落架零件数由23件减至1件,疲劳强度反升50%3。
以轧代锻技术
航空级钛合金“一火成材”:中冶京诚开发近恒温轧制(±50℃控温),将单卷盘重由70kg提至200kg,生产线效率提升300%。
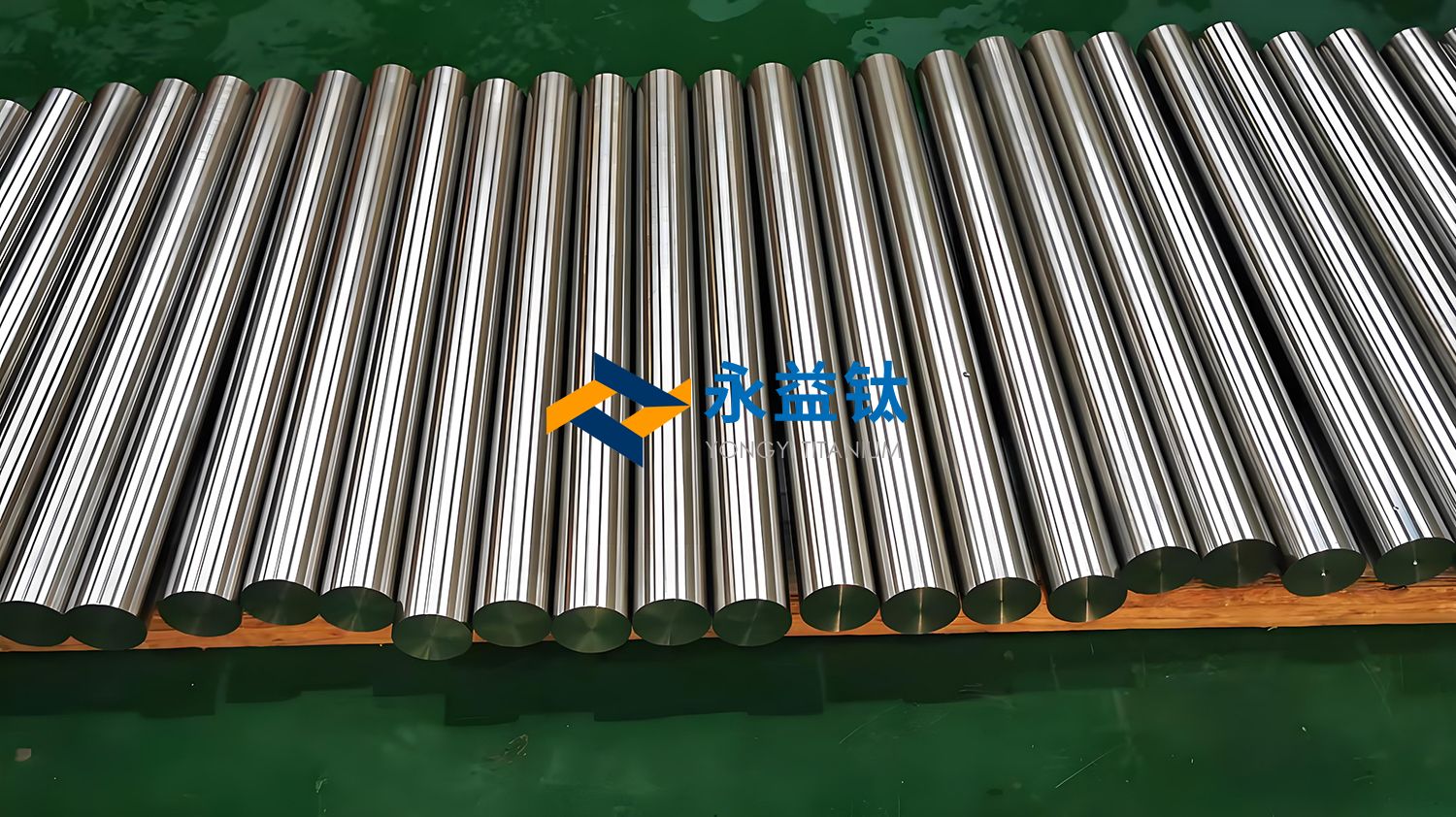
八、质量控制与缺陷防治
缺陷类型 | 成因 | 解决方案 |
心部粗晶 | 大规格锻件心部变形不足+温升过热 | 跨相区锻造+快速水冷存储畸变能8 |
细晶亮带 | 边部降温快导致晶粒破碎不充分 | 控制单火变形量<30%+均匀加热2 |
十字形内裂 | 高氧TC4合金(O>0.20%)棱角温降 | 倒棱频率提升+锤锻改液压机缓变形2 |
超声波杂波超标 | 组织不均匀或残余应力 | β锻造+固溶细化β晶粒1 |
九、技术演进趋势
大尺寸化:西部超导6吨级VAR炉支撑Φ500mm均质Ti5331棒材制备,满足核电紧固件需求。
绿色智造:金天钛金EB冷床炉(EBCHM)使废钛回收率达30%,再生TA1氧含量≤800ppm。
性能极限突破:中广核研发ODS强化钛合金(Y₂Ti₂O7弥散相),目标将快中子辐照耐受剂量提升至10²⁶ n/cm²。
航空钛合金锻件工艺正向超纯净熔炼、控形控性一体化锻造及增材-等温锻复合制造方向跨越。未来需进一步攻克φ1000mm+锻件偏析控制、聚变堆材料750℃耐温极限等挑战,支撑航空发动机与空天飞行器的极端服役需求。
相关链接